Creating the Next Generation of Flexible Reclosable Packages
David J. Anzini, Zip-Pak, an ITW Company, Duluth, GeorgiaAbstract
Reclosure features have been available on flexible
packaging for decades. The reclosure has to a great extent
become a standard feature versus an option. End user
expectations for a positive package experience have led to
the creation of reclosures and technology that can address
the unmet needs that remain a concern of the consumer.
New developments in reclosable technology are presented
that extend the capabilities of the reclosure to further
engage the end user.
Introduction
Zipper type reclosures have been available for many
years, finding their way from the child's zippered pencil
case to consumer food storage bags and then on to flexible
food packaging. It has been literally decades since the first
examples of reclosable cheese and hot dog packages made
their appearance on the grocery store shelves. Since their
introduction into form fill seal(FFS) packaging, zippers
have been placed into many styles of flexible package,
across multiple machine formats. Today, one can find
reclosures on almost anywhere one looks in a grocery
store, whether it is on shredded cheese, pre-packaged
sliced deli meats, pet food or even salty snacks.
Along with the proliferation of the variety of food
types and package styles containing a reclosure, the zipper
has morphed into multiple styles, some of which are
relatively utilitarian in design, while others are more
specialized and adapted to specific package types or
situations. Today, one can find reclosures ranging from a
simple press to close "webless" zipper, an example of
which can be found on tortilla packages, all the way to a
slider zipper for heavy duty usage, an example of which
can be found on a 10kg dog food bag. In between the
extremes are the ubiquitous "press to close" style(PTC)
zippers, that will typically consist of integral profiles and
carrier webs(flanges), supplied as a discreet profile
extrusion. Figure 1 highlights this range of zipper styles
but is by no means an exhaustive representation of the
possibilities.
Now that the years have passed since the introduction
of zippers and they are well entrenched in flexible
packaging and in the hearts and minds of the consumer, the
question becomes one of "What have you done for me lately?" With the general acceptance of the zipper, comes
the higher expectation for something new and different. In
the past, the package designer/developer would come up
with an idea, develop it, and release it to the public, with
the expectation that "if we build it they will come." As we
have all become painfully aware during the recent
economic slowdown, "they" will not necessarily come
anymore just because the designer thinks he has a good
idea. The new thinking is to engage the customer first, to
determine their pain points, and then to act upon those
unmet needs. This "Outside-In" thinking is in stark
contrast to the old "Inside-Out" methods (i.e., build it and
they will come). So, where do we start with this new
development strategy? A survey of current trends in
flexible packaging was used to determine what the next
generation of zippered packages may look like.
Trend Analysis
Romanik[1] recently published an article identifying
eleven trends that he felt were relevant and developing
influences on flexible packaging. The list:
1. More easy-open, easy-reclose options
2. Clear high-barrier films
3. Penetration into entirely new categories
4. Viscous liquids in flexible pouches
5. Slow conversion of cereal from bag-in-box
6. More layers in coextrusion
7. Shaped flexible packaging
8. More retortable pouches
9. Pouches containing a wider range of liquid,
viscous, powdered, granulated and
particulate products
10. Sustainability in packaging
11. Waste-to-Energy
Interesting to note here that the number one item listed is
More easy-open, easy-reclose options on flexible
packaging. A further study performed by Zip-Pak[2] on
key trends in global packaging seems to corroborate
Romanik's number one finding - the world has changing
demograhics and an aging population. One of the
conclusions of the study was that "packaging must
accommodate an aging consumer base with more easier-toopen
packaging formats." It would seem to be a simple
extension of this thought to conclude that this same
packaging must also be easier to reclose. Anthony[3]
confirms this notion in his discussion of the importance of
easy-to-open packaging.
There are yet other trends that have been gaining
ground -
- The rise of the store brand as a rival to the
national brand - the store brands are using
packaging enhancements as a way to compete
head to head with the CPGs for the consumers'
dollar - Globalization - innovations can originate from
anywhere in the world, and turn up on the other
side of the planet in the blink of an eye - Consumers' desire for bolder, richer experiences
by achieving a more intense experience to any or
all of the senses[4]
Based on the studies cited above, it appears that the
consumer still would like additional reassurance that their
package will open and reclose simply and efficiently. Add
to that the desire to engage more of the senses in this
process, and we have the criteria to begin designing the
next generation reclosure. We will approach this as a three
step process, looking first individually and then
collectively at ease of opening; ease of reclosing; and
engagement of the end user in a multisensory fashion.
Redesigning Easy-to-Open
The first step in our new package will be to address
ease of opening concern. While there are several methods
for providing ease of opening, some designs are preferred
over others. While simple perforations will allow the user
to tear the top off of a flexible package without needing
scissors to cut it open, the perforated package is not air
tight and will not properly protect many products that
require a hermetically sealed package until being opened
by the consumer. So, perforations are out. Laser scoring
of the package film can be an option, as well the new
generation of film structures available that exhibit straight
line tear features. Use of these features in a flexible
package can become problematic, depending upon how the
package will be produced. If the package is produced in a
vertical form fill seal arrangement, that would require the
easy tear feature to be placed in the cross direction of the
film. This is not a good arrangement for straight line tear
film, nor is it optimal for laser scored film. While a laser
score can be placed in the cross direction, the process must
be monitored carefully to assure that excessive web tension
does not cause premature tearing of the score.
Peelable seals are another tool that the package
designer has at their disposal to achieve ease of opening.
Everyone is familiar with the salty snack bag that can be
gripped and pulled open at the top with relative ease. This
method of opening may not work as well on a heavier
gauge film structure, plus the addition of a zipper just
below the bag top will also make this method of opening
more difficult. Without some more positive way of
gripping the package film above a closed zipper, this
method of opening becomes extremely difficult.
A final option would be to consider utilizing the
zipper closure itself as the means for achieving ease of
opening. Indeed, after the film at the top of a package is
either opened or removed above the zipper, the zipper in
effect becomes the "fourth side" of the package. So, one
would ask, why cannot the zipper function in this fashion
for the initial opening of the package as well? One way in
which the zipper can achieve this is shown in Figure 2.
Here the zipper has incorporated into its construction a
peelable seal above the zipper profiles. This seal can be
pre-activated on the zipper prior to it being placed into the
package to ensure a uniform hermetic seal. The peel
strength of this seal can be adjusted in order to balance the
force needed to open the seal with the need for that seal to
remain unopened until such time as the end user wishes to
open it.
Any of the design options listed above can produce
the easy open feature so desired by the Consumer;
however, for maximum flexibility an easy open peelable
seal pre-applied to the zipper flanges is the most versatile
of the choices. This type of construction has been
demonstrated to effectively function as the fourth side of
the package, maintaining hermeticity from point of
manufacture through initial opening. Force required to
pull this seal open can be tailored to the package designer's
requirements, assuring a pleasant experience for the end
user.
Ease of Reclosure
Beyond the question of how to open it, one of the
more frustrating aspects of reclosable packaging occurs
when the consumer is done taking product out of the
package, goes to reclose the pack, and then finds that they
have failed in their attempt to reclose the zipper. There are
multiple reasons that this can happen, but at the end of the
day the failure of the zipper to reclose will be due to the
zipper profiles not re-aligning as the consumer presses the
zipper together to reseal the pack. This can be especially
frustrating in packages with wider mouth openings, where
the flexibility of the package film seemingly is working
against the consumer who is trying to re-align the zipper
and get it to close correctly. The trend has been further
accelerated by recent advances that have allowed for
thinner gauge film constructions, which become even more
flexible.
One answer to the alignment issue is the use of a
double profile zipper, such as is shown in Figure 3. The
addition of the second profile effectively stiffens the zipper and the film substrate that it is attached to. This allows the
user to more easily re-align the two profiles when closing
the package, plus it has an added sensory benefit - as the
consumer slides their finger across the package to finish
reclosing the zipper, they can feel their finger resting in the
space between the two profiles, so they know that they are
closing the package correctly.
The advent of the double profile closure has gone a
long way toward resolving the ease of closure issue;
however, as good a solution as it is, it can still be misaligned
- it is not foolproof. Christoff[5] had proposed a
solution to this problem that recently has been adopted by
several producers or reclose solutions. The self-aligning or
multi-align reclosure can be looked at as an evolution of
the hook-and-loop style of closure. This has become a
closure style that has been variously described as "hook to
hook", "self mating micro-hooks", or a "resealable matrix".
Typical examples of this closure are shown in Figure 4. In
any case, this closure option provides the package designer
with a solution that is as close to foolproof as one can get,
for it will reclose even if it is not totally re-aligned, plus it
takes relatively little effort to close this feature. These
solutions presented will allow the package designer to
create an improved easy-to-open and easy-to-close
package, but there are further enhancements possible that
allow the package designer and the package to engage
more of the Consumers' senses with unique features.
Engaging the Senses
The zippered package has become a standard part of
the packaging landscape, and we as end users have become
almost oblivious to the reclose feature(except if it fails!).
The development of double profile and multi-align
closures now provides the package designer the unique
opportunity to engage several of the consumers senses
simultaneously, with what can be described here as
Interactive Packaging. We had seen earlier that the
double profile zipper can give the user a subtle tactile cue
that the zipper is aligned and closing correctly, by the way
the finger fits against the package. With the new
generation of closures, it is possible to improve upon that
experience with a much more positive use of tactile and
audible cues.
Addition of audible and tactile features can be
accomplished in several ways, two of which are shown in
Figure 5. In a post extrusion step, the closure profiles can
be reshaped, either via a mechanical deformation step or by
the simple removal of material. This post forming does not
and should not impede the ability of the zipper to function
as a closure. Rather, these deformations increase the
tactile feedback to the user, as well as provide an distinctly
audible "clicking" sound. As one would expect, the degree
of closure deformation will have an impact upon the
resultant tactile and audible response that the end user will
experience. These features have been successfully added
to both double profile and multi-align closures, giving the
designer yet another opportunity to engage their customers.
Conclusions
While the zipper closure has been available to the
package designer for decades, there are still opportunities
to improve upon that feature. A survey of consumer and
packaging trends reveals that ease of open/reclose remain a
consumer priority, while a more engaging experience is
desired. Closure developments will now allow the package
designer to consider the zipper as the legitimate fourth side
of the package, providing ease of initial package opening
along with a simple and secure reclose experience. The
addition of audible and tactile features gives the designer
the ability to provide a truly Interactive Package
experience - the consumer can see the package is open or
closed, and they can hear and feel the package opening and
closing, giving them the peace of mind that their package
is functioning correctly.
References
1. Ron Romanik, "Eleven Trends Shaping Flexible
Packaging", Packaging World (April 2013)
2. Lisa McTigue Pierce, "10 Key Trends in Global
Retail Packaging", Packaging Digest, (June 2013)
3. Sterling Anthony, "The Importance of Easy-to-Open
Packaging", Packaging World (July 2013)
4. Jeremy Lagomarsino, "Consumer Megatrends and
Packaging: a Quantitative Study", Packaging World
(June 2013)
5. Paul B. Christoff, US Patent 4,617,683
Key Words
Flexible Packaging; Zipper; Reclosures
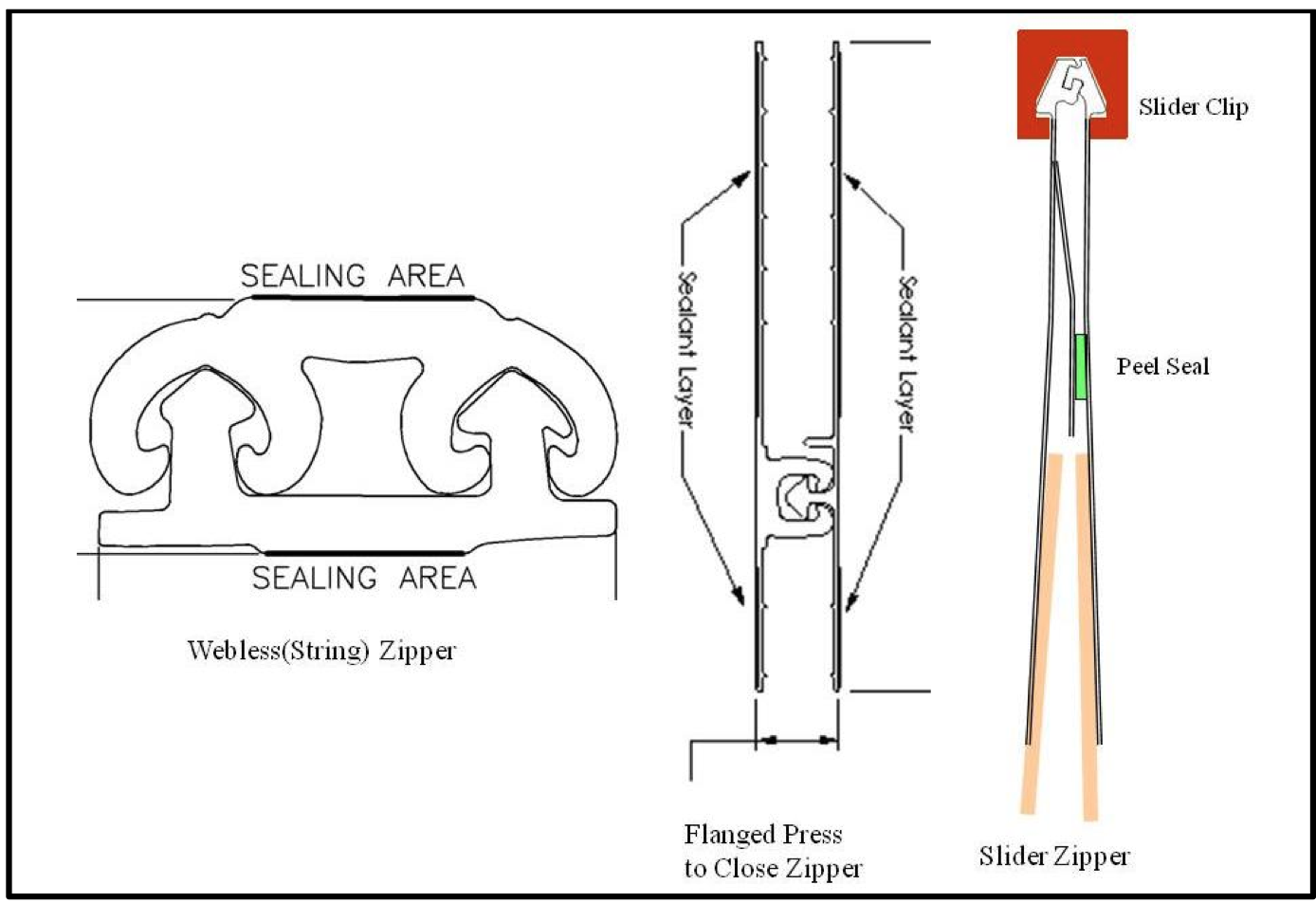
Figure 1: Representative styles of zipper reclosures
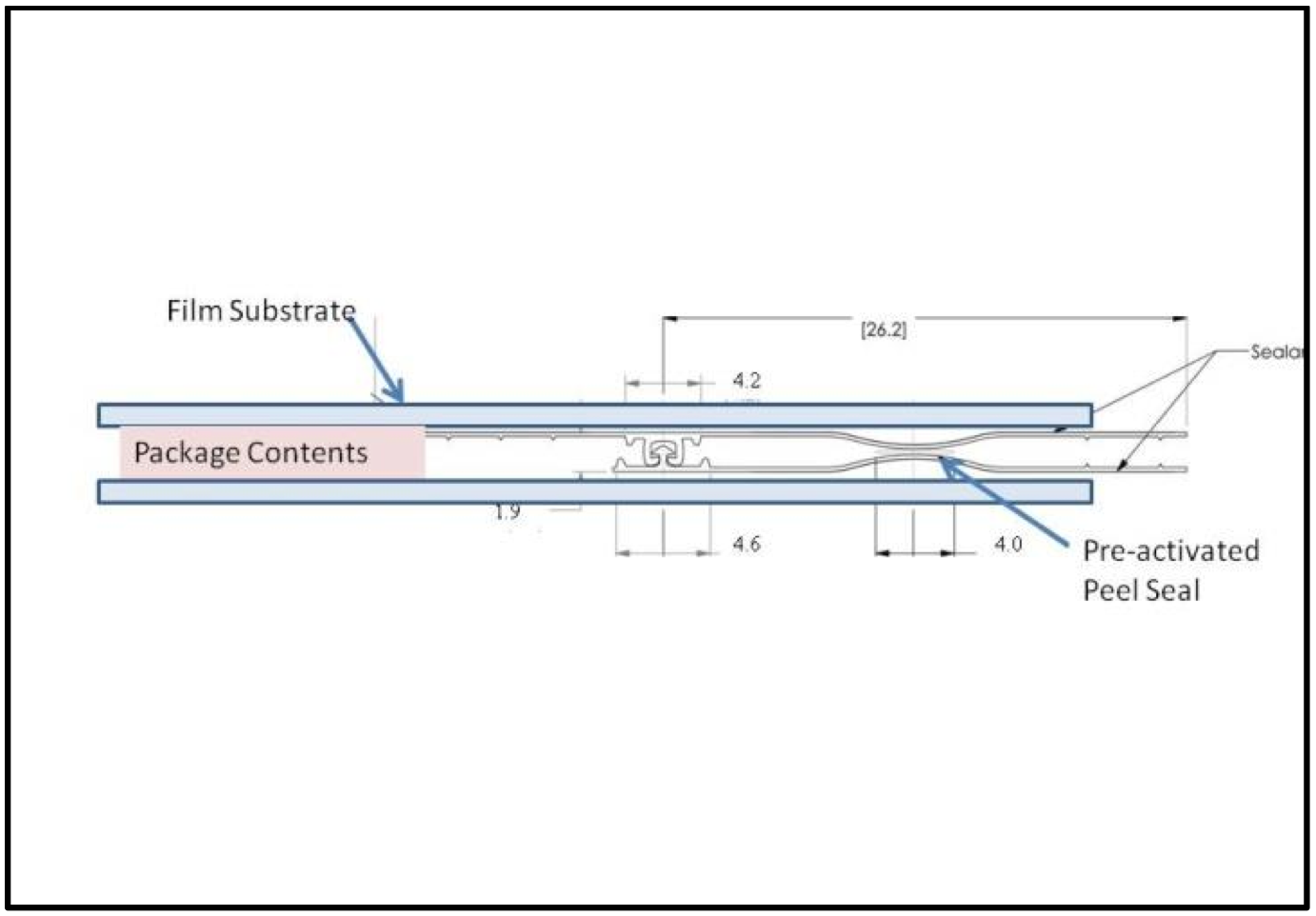
Figure 2: Example of an Easy-to-Open package, utilizing a peelable seal integral to the zipper
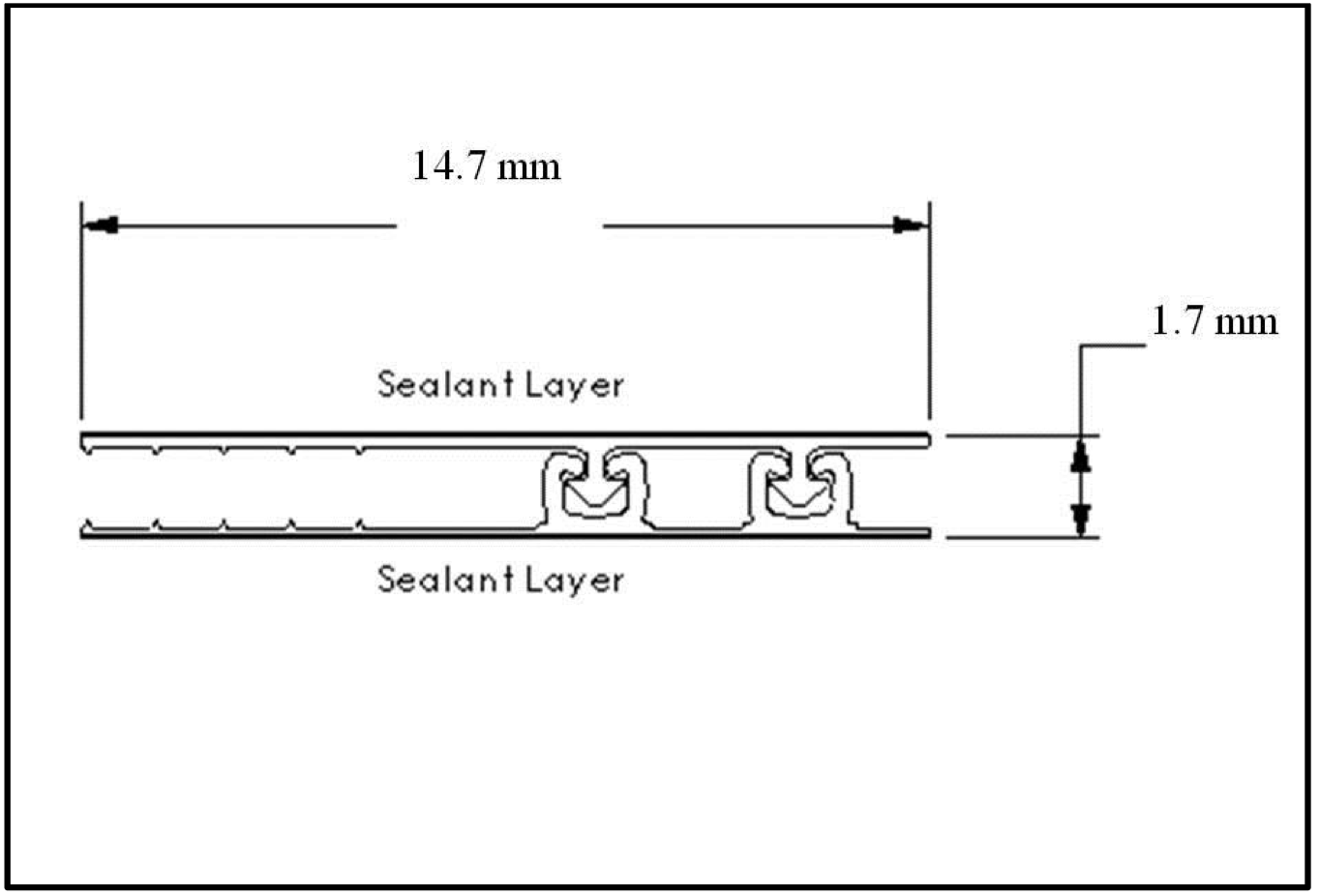
Figure 3: Example of a double profile zipper
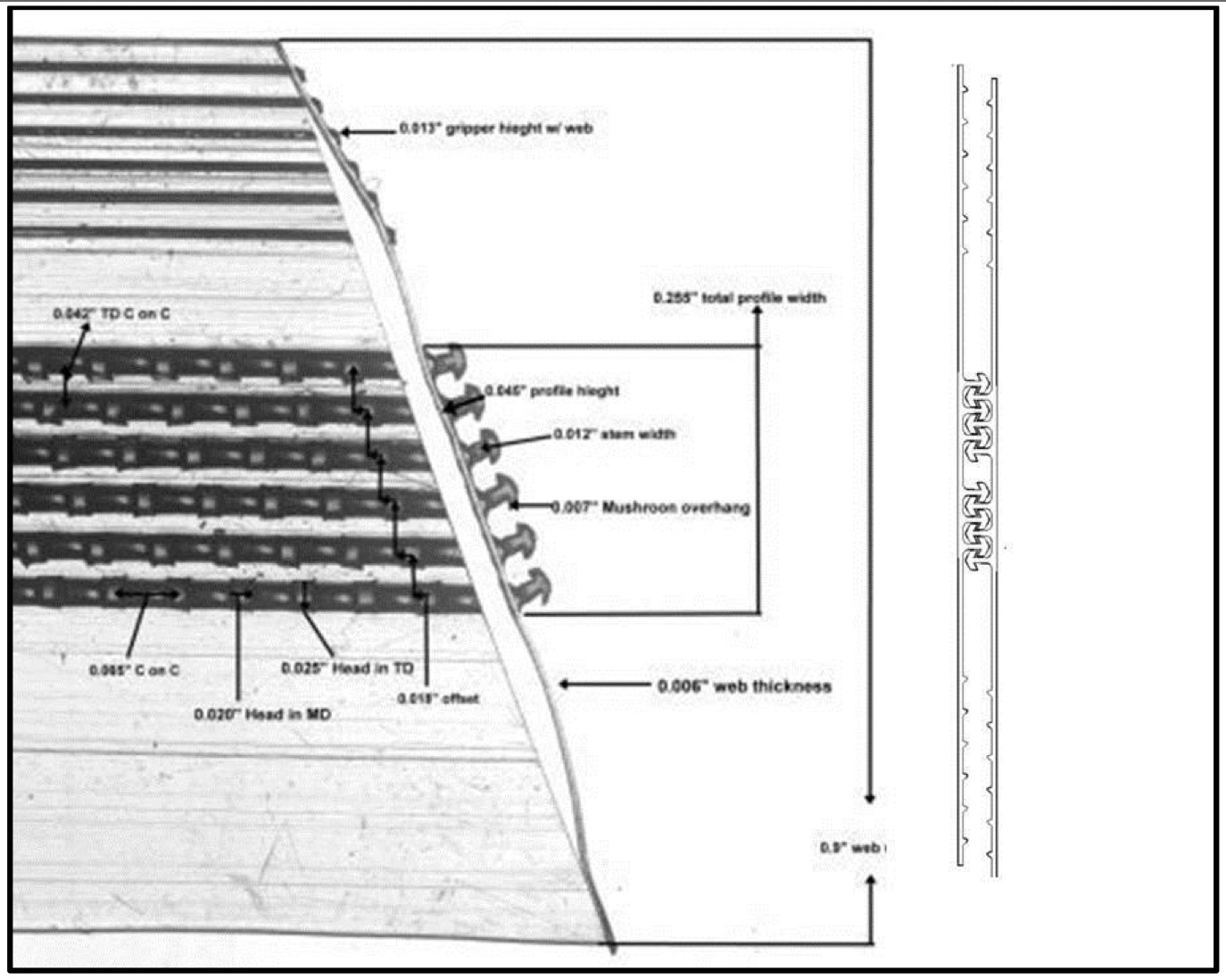
Figure 4: Multi-align styles of reclosure
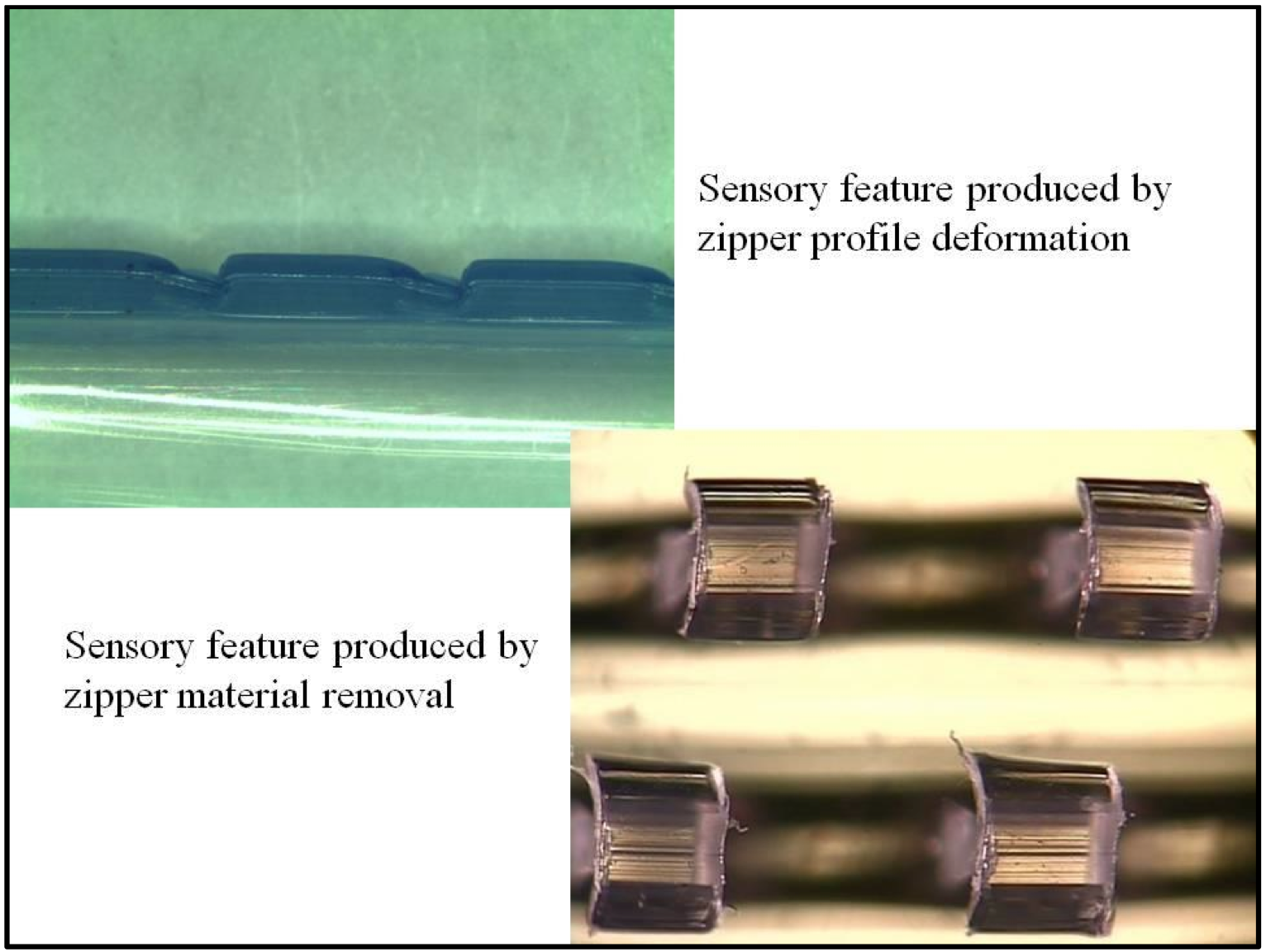
Figure 5: Enlarged view of audible/tactile features added to a reclosure
Return to
Paper of the Month.