Observations of Liquid-Liquid Encapsulation in Coextrusion of Inelastic Newtonian Fluids
Jonathan Lee, Jeffrey S. Allen, and Mahesh Gupta
Michigan Technological University, Houghton, MI 49931, USAAbstract
The conditions under which liquid-liquid
encapsulation can occur in coextrusion of polymers have
been experimentally studied. The objective of this study
was to determine if liquid-liquid encapsulation is a viscous
phenomenon, viscoelastic phenomenon, or a combination
of the two. The experimental observations discussed herein
focus on the role of viscous stresses on encapsulation in the
absence of viscoelastic behavior. Experiments with two
inelastic Newtonian fluids flowing side-by-side in a
transparent channel were conducted. Different
combinations of glycerol, silicone oil, and motor oil were
employed for the bi-layer flow experiments. Irrespective of
the difference in the viscosity, no core-annular
encapsulation was observed for bi-layer flows of glycerol
and silicone oil. In two of the experiments with bi-layer
flow of motor oil and silicone oil, motor oil encapsulated
the silicone oil, even when the viscosity of motor oil was
higher than the viscosity of the silicone oil. Since the flow
behavior remained unaffected even with large variation in
the viscosity of the fluids employed, it is concluded that
other fluid properties besides viscosity, such as wettability
of the fluid, may play an important role in reaching the
core-annular encapsulation often observed in bi-layer
flows. When gravity was acting perpendicular to the flow
direction the difference in the density of the fluids also
affected the layer arrangement.
Introduction
Liquid-liquid encapsulation is used to describe the
tendency of a liquid to displace another liquid in a
direction perpendicular to the flow direction, often along
the channel walls. This can result in one liquid forming an
annulus by completely wrapping around a core of another
fluid. Encapsulation has been observed in several fluidic
transport applications including the coextrusion of
viscoelastic polymers [1] as well as the lubricated
pipelining of crude oil and water, which are purely viscous
in nature [2]. There is disagreement in the literature on
whether viscosity difference alone result in encapsulation
or if other fluid properties need to be considered as well.
Some experimental observations report encapsulation is
driven by viscosity differences, but no model has been
shown to properly explain the behavior [3]. Multiple
unsuccessful attempts have been made at numerical
prediction of the encapsulation phenomenon using
generalized Newtonian formulations [4-6]. This indicates that a fluid property other than viscosity difference may
affect the initiation and development of encapsulation. The
results of an experimental parametric study of bi-layer flow
of several different fluid combinations are reported in this
paper.
Experimental Setup
Transparent channels were constructed to observe the
interaction of two fluids in a bi-layer flow. A 115 mm long
1 mm by 1 mm groove was micro-milled out of a smooth
12.5 cm thick polycarbonate plate such that two fluids
enter the channel at separate ports and converge at an angle
of 60° in a Y configuration. The machined surface of the
plate was clamped to another polycarbonate plate to form
the fourth wall of a square channel.
Transparent fluids were necessary in order to see
through the entire depth of the channel. Liquid-liquid
diffusion was avoided by running the experiments with
immiscible fluid pairs. One fluid pair was glycerol (Sigma
Aldrich) with polydimethylsiloxane (PDMS) silicone oil
(Gelest, Inc.). Another fluid pair was motor oil (Valvoline)
with the same PDMS silicone oil. Four different viscosity
grades of PDMS silicone oil were used with the glycerol
and motor oil to experiment with different viscosity ratios
between the fluids. All of these fluids are Newtonian with
fluid properties listed in Table 1.
Viscosities of the fluids were determined using
Cannon-Fenske viscometers. Specific gravity values in
Table 1 are based on manufacturer specifications. The
contact angle of glycerol was measured by placing a drop
of the liquid onto a polycarbonate surface and observing
the angle, θ, that the fluid formed at the solid-liquid-air
interface. Figure 1 shows an illustration of this contact
angle measurement. The contact angles for the motor oil
and the silicone oils were too small to be accurately
measured by viewing a liquid drop on a polycarbonate
plate from the orientation indicated in Figure 1.
Approximations of the contact angles for these fluids are
shown in Table 1. Accurate measurements of the contact
angle for motor oil and silicone oil are currently being
performed.
Accurately visualizing the three-dimensional bi-layer
flow required an ability to focus on different planes at
various depths within the channel. To achieve a variabledepth
focus, fluorescent microparticles were added to the
fluids. A fluorescent light source was used for excitation of
the fluorescent microparticles and a stereomicroscope with
fluorescent filters allowed the particles to be focused upon
at different depths of the channel.
All experiments were performed at room temperature
with syringe pumps moving the fluids through the channel
at matched flow rates. The fluids were introduced into the
channel by first filling the channel with one fluid, and then
introducing the second fluid to generate a layered flow
condition. All experiments were repeated by alternating
which fluid was introduced to the channel first to observe
any difference in the final flow configuration. The
experiments were repeated with the channels oriented
horizontally and vertically to verify that gravity was not
inducing or hindering any encapsulation effects in any of
the experiments. The fluids were pumped over a range of
flow rates from 0.12 to 3.58 mm
3/sec. All of the reported
observations are based on repeated results from multiple
experiment trials.
Experimental Observations
The configuration of the two fluids at the initial
contact with each other at the Y intersection is referred to
as a side-by-side configuration and is illustrated in Figure
2. As the side-by-side co-flow fluids travelled down the
channel the final flow configuration at the exit either (i)
remained unchanged, (ii) remained side-by-side with the
fluid interface oriented in a new direction with respect to
gravity, or (iii) evolved to fully encapsulated flow as
illustrated in Figure 3.
Values of Reynolds, capillary, and Bond numbers are
listed in Table 2 to quantify the relations of inertia to
viscosity, viscosity to surface tension, and gravity to
surface tension observed in each experimental set.
Approximate values of dimensionless numbers from
coextrusion of polyethylene performed by Dooley and
Rudolph [1] are included in Table 2 for comparison with
the conditions and fluids used in these experiments. The
Reynolds and Bond numbers indicate that inertia and
gravity have small influence on the liquid-liquid systems as
in a typical polymer coextrusion. However, the capillary
numbers indicate that surface tension effects here are more
prevalent relative to viscous effects here than in polymer
coextrusion. Despite the capillary number differences,
encapsulation as observed in polymer coextrusion has also
been observed in some of the experiments in this work.
Glycerol and PDMS Silicone Oil¶
The glycerol-silicone oil experiments never exhibited
encapsulation regardless of the viscosity difference
between the two liquids. The initial side-by-side flow
configuration was maintained throughout the length of the channel even though glycerol was much more viscous than
the silicone oils A, B, C, and D as listed in Table 1.
In the set of experiments where gravity acted
perpendicular to the flow direction, buoyancy-induced
layer rearrangement was observed. The lighter silicone oil
displayed a tendency to gravitationally stratify on top of
the heavier glycerol while the large contact angle of the
glycerol resisted deformation and limited the development
of the buoyancy driven layer rearrangement. Additionally,
the order in which the liquids were introduced affected the
extent of the development of gravitational stratification
relative to the initial side-by-side configuration. As the
thinner and more wetting fluid, silicone oil did not displace
the glycerol as easily as the glycerol displaced the silicone
oil. Figures 4 and 5 illustrate a situation in which different
final flow configurations were observed by changing only
the order in which the fluids were introduced to the system.
Motor Oil and PDMS Silicone Oil¶
Encapsulation was observed for certain motor oilsilicone
oil combinations. When the high viscosity silicone
oil (A) was used, the less viscous motor oil fully
encapsulated the more viscous silicone oil regardless of the
orientation of gravity. Images of encapsulated flow from
the motor oil-silicone oil (A) experiments are shown in
Figures 6 and 7.
When silicone oil (B), which has a smaller viscosity
than that of the motor oil, was used, the more viscous
motor oil fully encapsulated the less viscous silicone oil
regardless of the orientation of gravity. Figures 8 and 9
show the encapsulated flow from these experiments.
When either silicone oils (C) or (D) were used with
motor oil and the gravity was along the flow direction, in
spite of the large difference between the viscosities of the
motor oil and the two silicone oils the initial side-by-side
flow configuration was maintained for the length of the
channel. The side-by-side flow configuration in the
absence of buoyancy driven layer rearrangement is
depicted in Figures 10 and 11. When the gravity acted
perpendicular to the flow direction gravitational
reorientation occurred in both of these sets of experiments.
The buoyancy-induced layer rearrangement that occurred
in these experiments is illustrated with Figures 12 and 13.
Discussion
Glycerol and PDMS Silicone OilThe relatively large contact angle of glycerol was an
important factor in the final flow configuration in these
experiments. Figure 5 illustrates that the gravitational layer
rearrangement never reached a fully stratified state in the
glycerol-silicone oil experiments when gravity acted perpendicular to the flow direction. In contrast, Figures 12
and 13 illustrate that in the motor oil-silicone oil
experiments the gravitational layer rearrangement always
reached a fully stratified state. These differing observations
can be explained by the large contact angle of the glycerol.
The forces necessary to deform the glycerol contact line
perpendicular to the flow direction had an apparent
minimizing effect on the extent to which any gravitational
layer rearrangement occurred. Subsequently, the less
viscous silicone oil did not encapsulate the more viscous
glycerol as expected. The absence of encapsulation may
have been due to contact line pinning at the liquid-liquid-solid
interface.
Motor Oil and PDMS Silicone OilEncapsulation as reported by the literature claims that
the less viscous liquid will encapsulate the more viscous
liquid [1-6]. With silicone oil (A) this encapsulation was
observed. The experiments with silicone oil (B) and motor
oil resulted in the more viscous liquid encapsulating the
less viscous liquid. Because this “inverse encapsulation”
occurred in purely viscous fluids, an analysis suggests that
at least one property of Newtonian liquids other than
viscosity plays a role in the onset of liquid-liquid
encapsulation. The experiments with silicone oils (C) and
(D) with motor oil resulted in no encapsulation. Just like
with the glycerol experiments it is suggested that the larger
contact angle of the motor oil could have been resisting the
displacement by the thinner silicone oils along the channel
walls.
Conclusions
Transparent Newtonian fluids pumped through a
polycarbonate channel were visualized through a
stereomicroscope via fluorescent excitation of
microparticles. Either side-by-side or encapsulated flow
were observed as the final flow configuration in all of the
experimental combinations. Gravitational influence was
observed in all experiments in which gravity was acting
perpendicular to the direction of flow. However, the effect
of gravity did not change the final flow configuration from
the type which was observed when the gravity was acting
parallel to the direction of flow.
Encapsulation did not occur between glycerol and any
of the silicone oils. The relatively large contact angle of the
glycerol is expected to have been nullifying any force imbalance that would otherwise have initiated
encapsulation.
Encapsulation as described by the literature occurred
between motor oil and silicone oil (A). In this situation the
more viscous fluid was encapsulated by the less viscous
fluid. However, the opposite type of encapsulation
occurred between motor oil and silicone oil (B). Here the
less viscous fluid was encapsulated by the more viscous
fluid. There is currently no suggested explanation for this
phenomenon. In the experiments of motor oil and silicone
oils (C) and (D) a side-by-side configuration was the
resultant flow configuration. The apparent contact angle
difference between the fluids could once again lead to the
explanation for the lack of encapsulation in these trials.
Acknowledgements
This research was supported by the Department of
Mechanical Engineering - Engineering Mechanics at
Michigan Technological University. The authors would
like to thank Dr. Morrison and Jithendar Gujja for
assistance with fluid viscosity measurements.
References
1. J. Dooley and L. Rudolph, “Viscous and Elastic Effects
in Polymer Coextrusion”, Journal of Plastic Film &
Sheeting, 19, 111 (2003).
2. D. D. Joseph, “Lubricated pipelining”, Powder
Technology, 94, 211 (1997).
3. P. Yue, C. Zhou, J. Dooley, and J. Feng, “Elastic
encapsulation in bicomponent stratified flow of
viscoelastic fluids”, Journal of Rheology, 52, 1027
(2008).
4. A. Karagiannis, A. N. Hyrmak, and J. Vlachopooulo,
“Three-dimensional studies on bicomponent extrusion”,
Rheologica Acta, 29, 71 (1990).
5. K. B. Sunwoo, S. J. Park, S. J. Lee, K. H. Ahn, and S. J.
Lee, “Three-dimensional numerical simulation of
nonisothermal coextrusion process with generalized
Newtonian fluids.” Korea-Australia Rheology Journal,
12, 165 (2000).
6. M. Gupta, “Mesh Partitioning Technique for ThreeDimensional
Simulation of Coextrusion”, SPE ANTEC
Tech. Papers, 54, 217 (2008).
Keywords: Newtonian, encapsulation, contact angle,
fluorescent.

Table 1. Properties of fluids employed in experiments

Table 2. Dimensional analysis of experiments
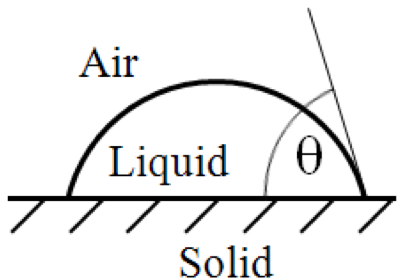
Figure 1. Depiction of solid-liquid-air contact angle measurement θ.
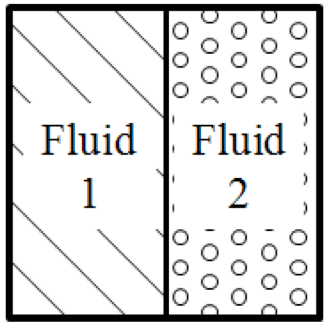
Figure 2. Side-by-side flow configuration.
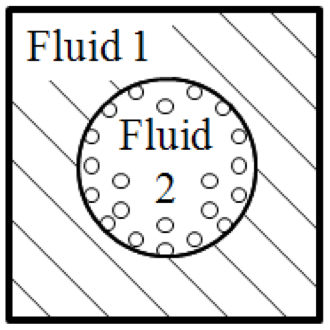
Figure 3. Fully encapsulated flow configuration. Fluid 1 forms an annulus and Fluid 2 forms a core.
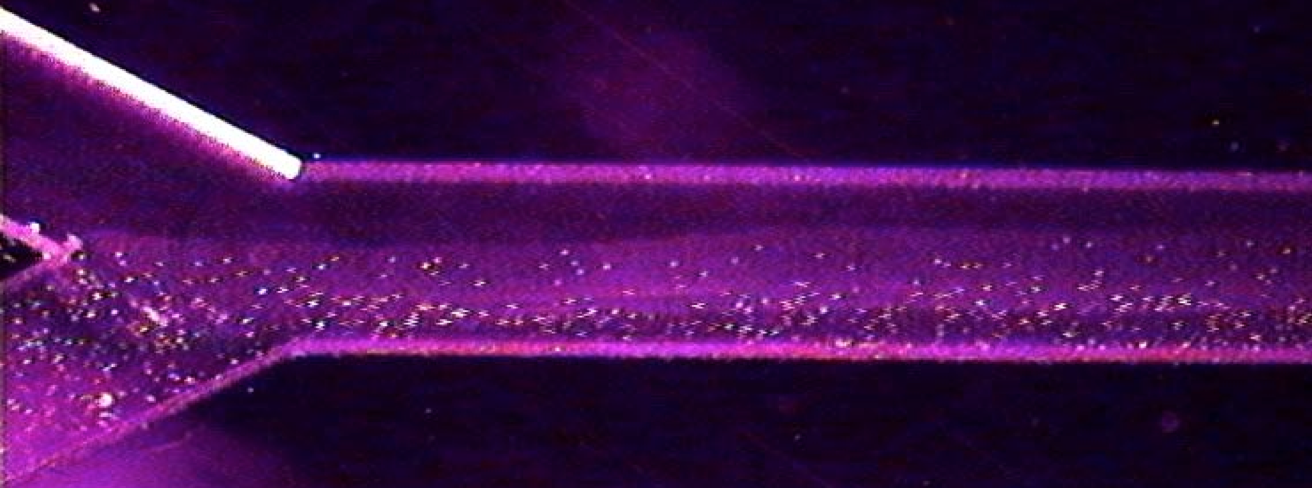
Figure 4. Silicone oil (A) (bottom) and glycerol (top) extruded left to right through the converging channel. Microparticles in the silicone oil are highlighted with the fluorescent light. Here gravity is oriented perpendicular to the page and buoyancy- induced stratification was observed. In this image buoyancy has altered the initial side-by-side configuration by moving one liquid-liquid-solid interface line up the page and the other down the page. The cross-sectional view shown in Figure 5(b) illustrates the final flow configuration of this image.
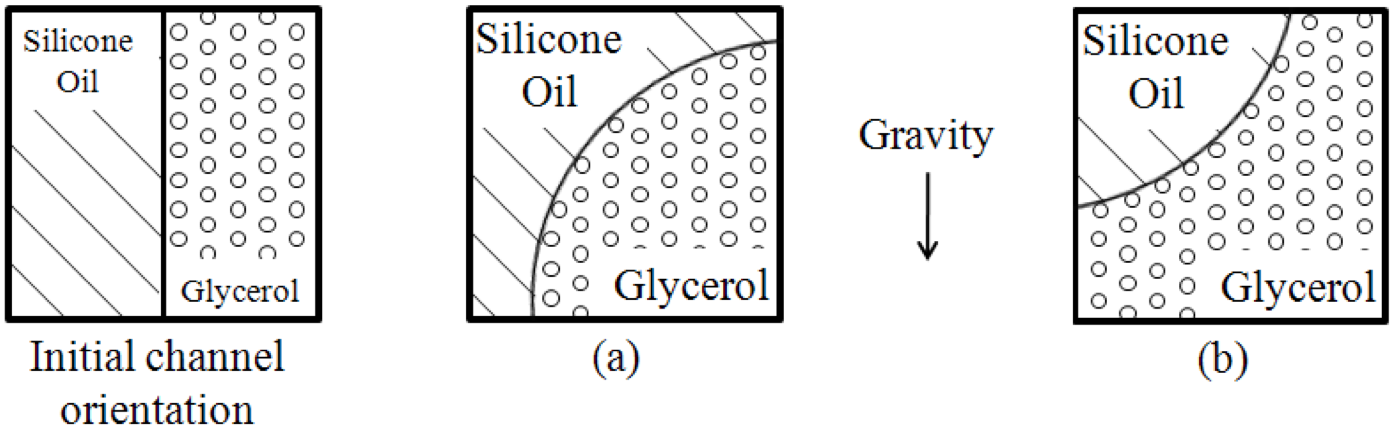
Figure 5. The final flow configuration of glycerol and silicone oil depicted in (a) resulted when the silicone oil was the first fluid in the channel and was displaced by glycerol. Provided that the exact same initial orientation was repeated, the flow configuration in (b) resulted when the glycerol was the first fluid in the channel and was displaced by silicone oil.
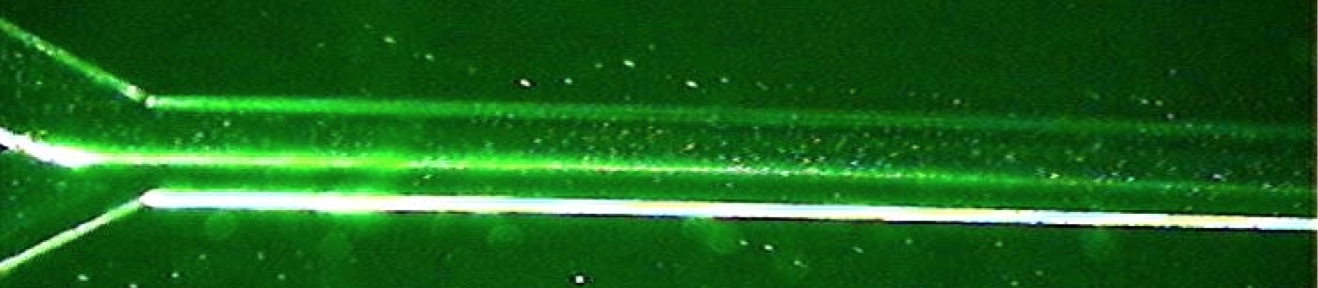
Figure 6. Silicone oil (A) (bottom) and motor oil (top) extruded left to right in the converging channel. Microparticles in the motor oil are highlighted with the fluorescent light filter. Here encapsulation was observed regardless of the orientation of gravity. The liquid-liquid-solid interface line seen in this image approached the side of the channel as the motor oil encapsulated the silicone oil.
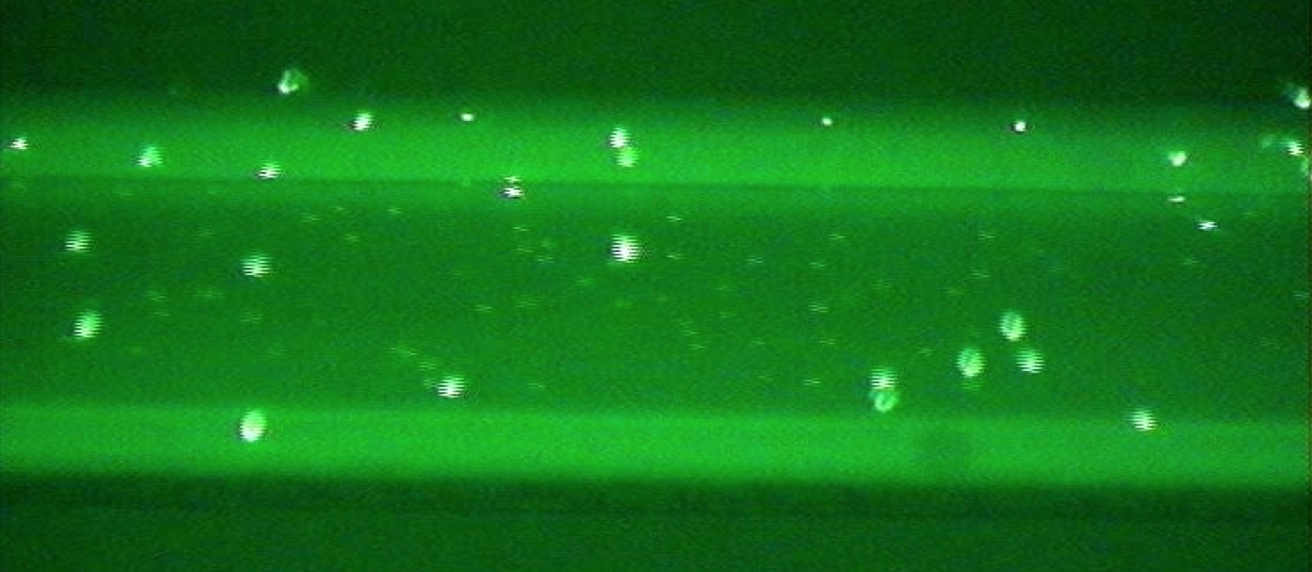
Figure 7. Silicone oil (A) (core- dark) and motor oil (annulus- light) extruded left to right. This magnification shows the fully encapsulated flow configuration with the silicone oil completely separated from all channel walls. Here the microparticles in the silicone oil are dimly visible while the microparticles in the motor oil are highlighted with the fluorescent lighting. In this image some of the microparticles in the motor oil are in focus and others are out of focus. This is an indication that the motor oil had fully encapsulated the silicone oil.
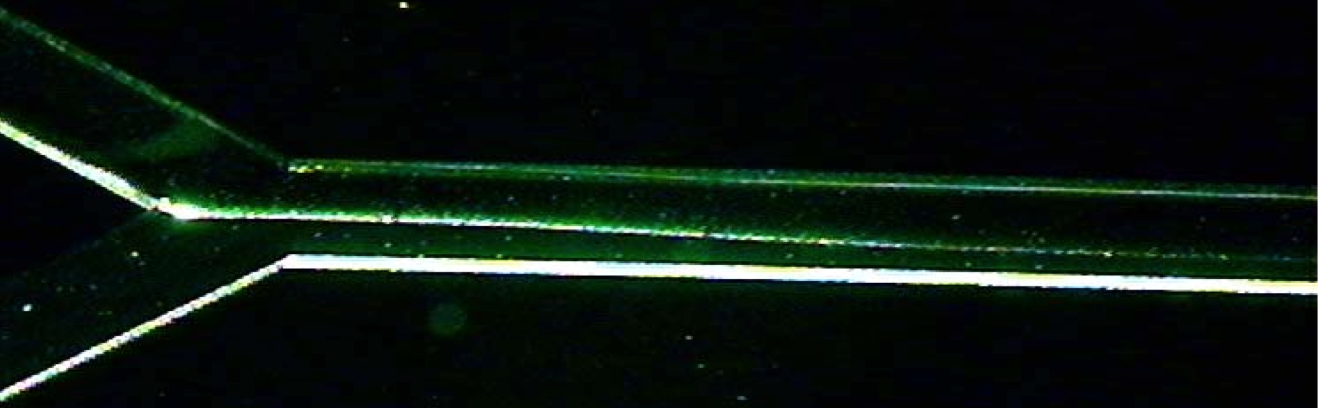
Figure 8. Silicone oil (B) (bottom) and motor oil (top) extruded left to right through the converging channel. Here encapsulation was observed regardless of the orientation of gravity. The liquid-liquid-solid interface line seen in this image approached the side of the channel as the motor oil encapsulated the silicone oil.
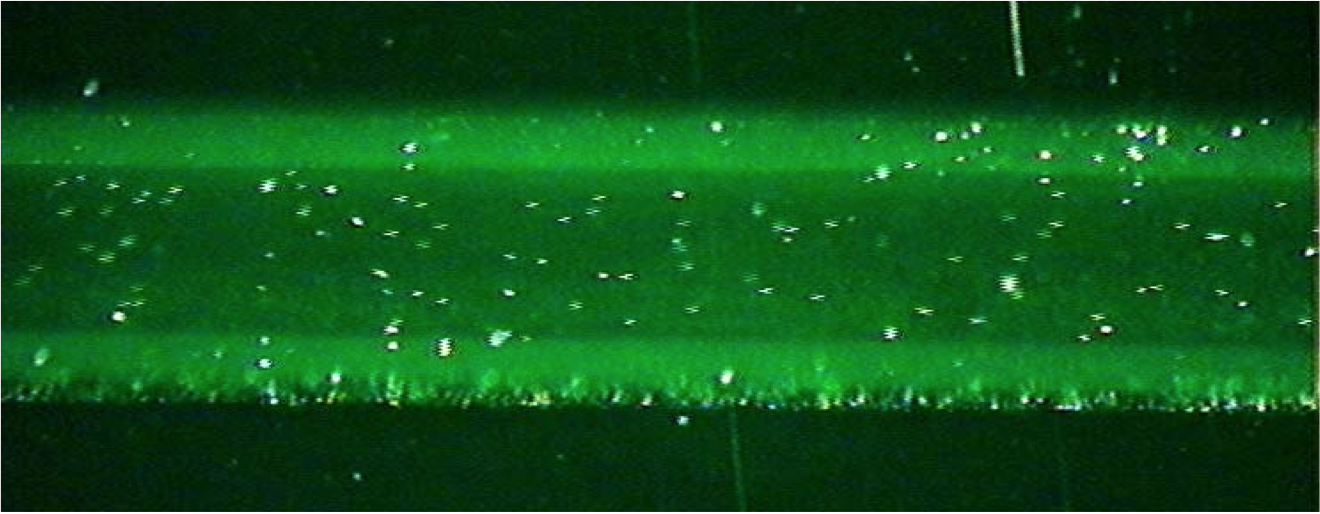
Figure 9. Silicone oil (B) (core- dark) and motor oil (annulus- light) extruded left to right. This magnification shows the fully encapsulated flow configuration with the silicone oil completely separated from all channel walls. Here the microparticles in the silicone oil are dimly visible while the microparticles in the motor oil are highlighted with the fluorescent lighting. In this image some of the microparticles in the motor oil are in focus and others are out of focus. This is an indication that the motor oil had fully encapsulated the silicone oil.

Figure 10. Silicone oil (D) (bottom) and motor oil (top) extruded left to right in the converging channel. Here buoyancy- induced layer rearrangement was not observed as the heavier silicone oil entered the channel already beneath the motor oil. The side-by-side flow configuration is shown here under normal lighting conditions.
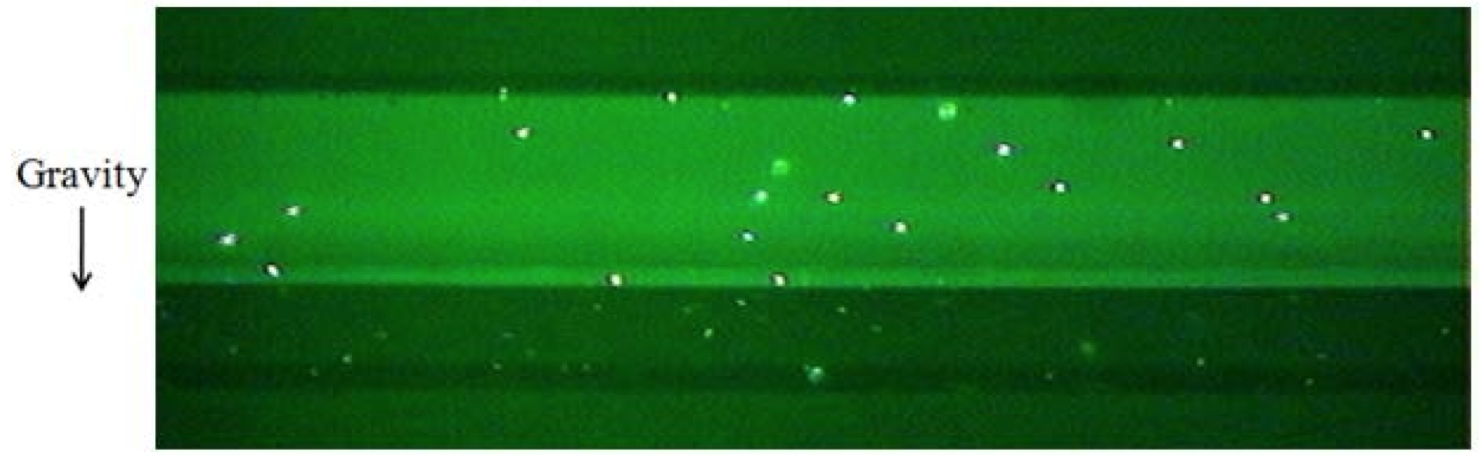
Figure 11. Silicone oil (C) (bottom) and motor oil (top) extruded left to right in the converging channel. Here buoyancy- induced layer rearrangement was not observed as the heavier silicone oil entered the channel already beneath the motor oil. A magnification of the side-by-side flow configuration is shown here with fluorescent lighting highlighting the microparticles in the motor oil.

Figure 12. Silicone oil (C) (top at the intersection) and motor oil (bottom at the intersection) extruded left to right in the converging channel. Here buoyancy-induced layer rearrangement was observed as the heavier silicone oil did not enter the channel in a gravitationally stable arrangement with respect to the lighter motor oil. In the center of this figure the side-by- side configuration has rotated 90° relative to its original orientation. At the right edge of this figure the side-by-side flow configuration has rotated 180° relative to its original orientation. Cross-sectional images in Figure 13 illustrate the flow configuration at points (a), (b), and (c) in this image.
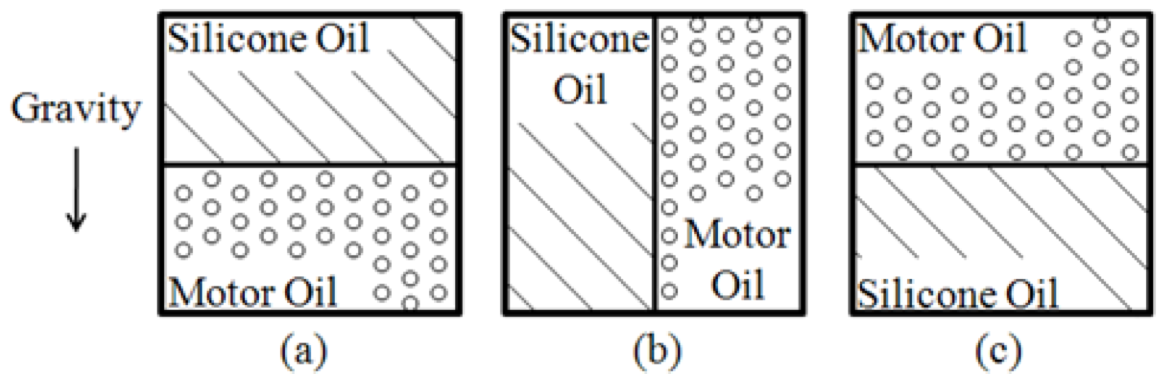
Figure 13. This sequence of cross-sectional images illustrates the gravitational layer rearrangement depicted in Figure 12.
Return to
Paper of the Month.