Using Extreme Barrel Diameters to Verify the Numerical Simulation of Single-Screw Extruders
Mark A. Spalding - The Dow Chemical Company, Midland, MI
Greg A. Campbell, Fredrick Carlson, and Kambiz Nazrisdoust - Clarkson University, Potsdam, NY
Abstract
Numerous models exist for the prediction of pressure profiles in the metering section of single-screw extruders. For the most part, these models were verified using experimental data from small diameter extruders. Verification using data from large diameter machines, however, has not been fully explored due to the lack of experimental data. The analysis here will show the effect of barrel diameter on the ability of a model to predict pressure profiles in the metering channel.
Introduction
The use of numerical simulation for the design of screws for single-screw machines has been limited to date by many factors. For the solids conveying section, limitations exist due to the lack of a full understanding of the physical mechanism and physical property data for the resin (1). Simulation of the melting process is just as complex (2-5) and is also limited by the lack of physical property data for the resin and verified software. Simulation of the metering section where the material is fully molten would appear to be the simplest. This section, however, can be problematic since previous research (6) has shown that the standard assumption of barrel rotation creates unrealistic thermal effects. Moreover, all sections of the extruder are impacted by whether the simulation utilizes a reference frame of barrel rotation or the actual screw rotation.
Obviously, the solids conveying and melting sections of the screw are considerably more complex than the processes that occur in the metering section of the screw where all resin is in the molten state. Here, only the simulation of the metering section or a section that contains only molten material will be considered. Many commercially available models use the Newtonian Tadmor (7) model for metering channel calculations. Other models have been developed using different techniques including three dimensional finite element analysis (FEA) (8), two dimensional FEA with a rotating barrel (9), a channel model with advanced specifications and a rotating barrel (10), and a model with a rotating screw (11). For the most part, these models were verified using extrusion data from relatively small diameter screws. Large diameter extrusion data sets are not readily available and thus they are not used for model development. Moreover, these FEA codes are typically difficult to use and take a long time to run on a fast computer.
The goal of this paper is to show how well current metering channel models (standard flighted channels that contain only molten resin) predict the performance of a machine. The main performance criterion here is the prediction of the pressure gradient or discharge pressure. The analysis will show the effect of barrel diameter on the
model’ s ability to predict experimentally determined pressures.
Resins
Two low density polyethylene (LDPE) resins were used for the experimental work. Both resins had a solid density of 0.922 g/cm
3. The melt indices (MI) for the resins were 0.8 and 2 dg/min (190 °C, 2.16 kg). The melt density, thermal conductivity, and heat capacity at about 210 °C were 0.74 g/cm
3, 0.18 W/(m°C), and 1260 J/(kg°C), respectively. Shear viscosity for the resins are shown by Figures 1 and 2 and were modeled using a power law as follows:

where n is shear viscosity (Pa-s), (y with dot) is the shear rate (1/s), T is the temperature (°C), n is the power law constant, and, b, and T
o are model constants. The model constants for the resins are provided in Table 1.
Experimental Data
In order to determine the quality of any numerical simulation, the calculations must be compared to experimental data. Two experimental data sets will be provided here for extruder diameters of 63.5 and 500 mm. These data will be used to compare the quality of the different numerical methods.
Process Data for a 63.5 mm Diameter Extruder
The experiments were performed previously (8) on a 63.5 mm diameter, 21:1 length-to-diameter (L/D) ratio extruder. The extruder was highly instrumented and had three barrel temperature control zones. These zones were operated at set points of 150, 177, and 205 °C for zones 1 (feed), 2, and 3, respectively. A single-flighted, square- pitched screw was used. This screw had six diameters of constant-depth feed channel at 8.89 mm, eight diameters of taper, and seven diameters of a constant-depth meter at 3.18 mm. The flight width perpendicular to the flight and the flight clearance were 7.94 mm and 0.07 mm, respectively. The flight radii were 6.35 mm and 9.53 mm for the pushing and trailing flights in the metering channel, respectively.
This experiment used the 2 MI resin. At the above barrel set point temperatures, the extruder was allowed to come to a steady state at screw speeds of 40, 60, and 80 rpm. The average pressures and the rates are shown by Figure 3. The extrudate temperatures were about 210 °C at all three screw speeds. As indicated by Figure 3, the pressure gradient in the metering section at 60 rpm was about -2.3 MPa over an axial distance of 2.4 diameters, resulting in an average pressure gradient of -0.96 MPa per diameter. The rate at 60 rpm was 41 kg/h.
Process Data for a 500 mm Diameter Extruder
A 500 mm diameter extruder was melt fed with the 0.8 MI resin at a rate of 11,800 kg/h and a screw speed of 46 rpm. The feed temperature and pressure of the resin were measured at 225 °C and 0.1 MPa, respectively.
The extruder was relatively long, but only the first 5.6 diameters needed to be simulated to demonstrate the effect of diameter on simulation accuracy. For this extruder, the feed pipe was 500 mm in diameter and thus forced the first diameter of the extruder to be at a temperature and pressure of 225 °C and 0.1 MPa. The screw started with a 1.5 diameter long, double-flighted feed section with a depth of 60 mm and a lead length of 750 mm. The next section of the screw was a 1 diameter long, double- flighted transition section with a lead length of 625 mm. The last section was a 3.1 diameters long, double-flighted constant-depth meter section with a depth of 27 mm and a lead length of 500 mm. The flight widths for all sections were 20 mm and the flight clearance was 0.5 mm.
A pressure transducer was positioned in the barrel at 5.6 diameters downstream of the start of the screw. For a screw speed of 46 rpm and a rate of 11,800 kg/h, the pressure at this location was measured at 6.4 MPa. The barrel temperature for this data set was at 190 °C.
Calculation Methods
Several different calculation methods were used for the simulations. These included the most common method used that was developed by Tadmor for Newtonian fluids (7), a three dimensional FEA method with wrapped (8) and unwrapped channels. The T admor method was modified such that the shear viscosity used for the calculation was based on the average shear rate and temperature in the channel. This pseudo-Newtonian method is used by many commercial codes. A commercial FEA code was used for the three dimensional simulations. Barrel rotation was used for all calculations and thermal affects were included. Not all methods were used for both data sets.
Numerical Simulations
The metering section of the 63.5 mm diameter extruder was simulated at 60 rpm and a rate of 41 kg/h using the pseudo-Newtonian Tadmor method and the un- wrapped and wrapped three dimensional FEA methods. For all cases the barrel temperature at the metering section was set at 205oC. The simulated pressure gradients for these methods are shown by Table 2. As shown by the data in this table, the simulated pressure gradients were all very close to the experimentally determined value of -0.96 MPa/diameter. The Tadmor model deviated form the experimental value the most with a pressure gradient of -1.3 MPa/diameter. This predicted pressure gradient, however, is likely acceptable for most design applications.
The 500 mm diameter extruder was simulated using the pseudo-Newtonian Tadmor method and also using the three dimensional, unwrapped FEA method. The axial pressure profiles for these analyses are shown by Figure 4, and the pressures at 5.6 diameters are shown by Table 3. As indicated by Figure 4, the pressure at 5.6 diameters was simulated at 6.4 MPa using the three dimensional FEA method and it matched well with the experimentally determined value of 6.4 MPa. The temperature at the end of the screw segment was simulated at 243°C. Figure 4 also shows the predicted pressure profile using the pseudo-Newtonian Tadmor model. For this model, the pressure at the end of the section was predicted to be 15 MPa, a pressure that was 2.3 times higher than the experimentally determined value. Due to this higher pressure prediction, the standard Tadmor model is unacceptable for designing a screw with a diameter of 500 mm.
Discussion
The numerical and experimental results presented here show that the standard pseudo-Newtonian Tadmormodel must be used with caution when predicting the pressure profiles in extrusion screws. As previously stated, many commercially available codes use this method. Although a complete investigation was not performed here, in general the deviation of the pseudo-Newtonian Tadmor method from the actual process will depend on many factors including barrel diameter, channel depth, number of flights, resin viscosity, and operations. Typically, the deviation becomes larger as the barrel diameter increases.
During the development of the three dimensional unwrapped FEA model for the 500 mm diameter extruder, the calculation was performed using a constant viscosity for the channel. That is, the viscosity was extracted from the power law data shown in Figure 2 at a nominal shear rate of 44 1/s and 230°C, a temperature slightly higher than the inlet temperature of 225°C. For this case, the exit pressure was substantially higher then when the full power law model was utilized. It has been known for a long time (7) that the power law index has an affect on both pressure flow and drag flow. That is, the shape factors for the channel for drag flow (Fd) and pressure flow (Fp) are dependent on the shear thinning nature of the resin. These shape factors represent the reducing effect of flow due to the presence of the flights relative to flow between two parallel plates. The combined flow predictions for pressure and drag terms, however, cannot be quantified from these relationships due to a non-linear interaction. For the three dimensional FEA method, the reduced flow at the flight edges are accounted for through the no-slip boundary conditions at the flight edge and the shear thinning nature of the resin. That is why the FEA method predicts the experimental pressures well at both large and small barrel diameters.
For the 500 mm diameter extruder, the pseudo-Newtonian Tadmor model over predicted the drag flow rate for the channel. This over prediction was caused by the utilization of a drag flow shape factor (Fd) that was too large. Then in order for the sum of the drag and pressure flows to match the actual flow in the channel, the pressure gradient was forced to be higher than actually required by the process. This higher pressure gradient is quite obvious from the simulations shown by Figure 4. The over prediction of the pressure gradient eventually caused the simulation to over predict the pressure at the end of the section by a factor of 2.3 times the measured value.
The pseudo-Newtonian Tadmor model has been used successfully for many years for the design of small diameter screws. Its success has brought considerable value to those designers that understood the method and its limitations. With high-speed computers and the availability of FEA methods, the accuracy of simulations has improved for small diameter machines and has become feasible for large diameter machines.
Thermal affects were included in the simulations although they were not fully discussed. Viscous energy dissipation from the rotating screw depends on the reference frame of the simulation; i.e., barrel rotation or screw rotation. Previous research (11) has shown that there are substantial differences in the experimentally determined temperature increase in a fluid depending on whether the barrel or screw was rotated. The best simulations will occur using a reference frame where the screw is rotated.
Conclusions
We have reported some new experimental data for a 63.5 mm and a 500 mm diameter extruder. The standard method using a pseudo-Newtonian Tadmor model worked well for the 63.5 mm diameter extruder, but over predicted the pressure for the 500 mm diameter machine. This method is used by many commercially available simulation codes and is an unacceptable method for large diameter machines. A full three dimensional FEA model and the appropriate power law viscosity function, however, predicted pressures and pressure gradients that were very close to the experimental values. Also, the experimental data presented here can be used to test the utility of new simulation codes since they represent the boundaries of the working space for most machines.
References
1. K.S. Hyun and M.A. Spalding, SPE-ANTEC Tech. Papers, 43, 211 (1997).
2. T.A. Hogan, M.A. Spalding, K.S. Cho, and C.I. Chung, SPE-ANTEC Tech. Papers, 48, 384 (2002).
3. B.K. Hong, H.S. Kim and C.I. Chung, SPE ANTEC Tech. Papers, 47, 272 (2001).
4. E.M. Mount and C.I. Chung, Polym. Eng. Sci., 18, 711 (1978).
5. M.A. Spalding, K.S. Hyun, and B.R. Cohen, SPE ANTEC Tech. Papers, 43, 202 (1997).
6. G.A. Campbell, H. Cheng, C. Wang, M. Bullwinkel, and M.A. te-Riele, SPE-ANTEC Tech. Papers, 48, 189 (2002).
7. Z. Tadmor and I. Klein, "Engineering Principles of Plasticating Extrusion," Van Nostrand Reinhold Co., New York, 1970.
8. M.A. Spalding, J. Dooley, K.S. Hyun, and S.R. Strand, SPE-ANTEC Tech. Papers, 39, 1533 (1993).
9. E.E. Agur and J. Vlachopoulos, Polym. Eng. Sci., 22, 1084 (1982).
10. H. Potente, “Single-Screw Extruder Analysis and Design,” chapter 5 of “Screw Extrusion,” ed. J.L. White and H. Potente, 2003.
11. G.A. Campbell, P.A. Sweeney, N. Donatula, and Ch. Wang, Int. Polym Process., XI, 199 (1996).
Key Words: Single-Screw Extrusion, Simulation, LDPE.
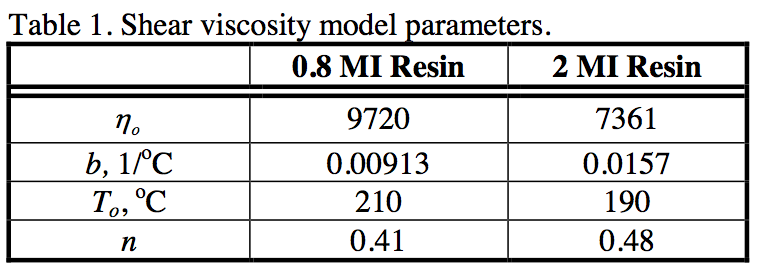
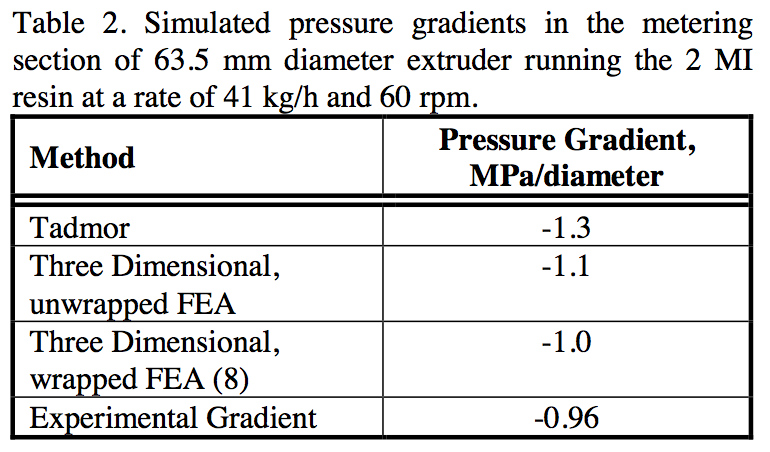
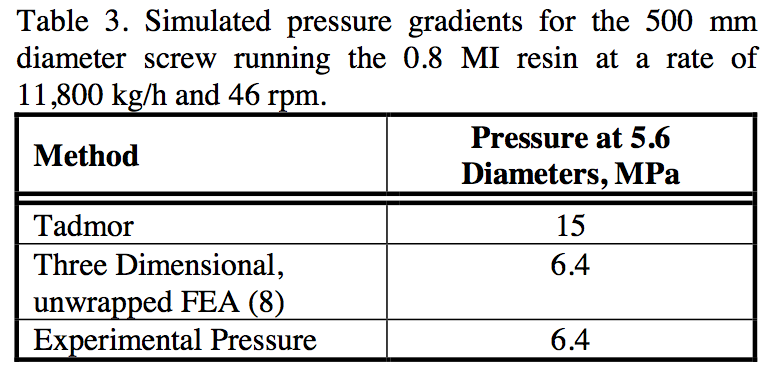
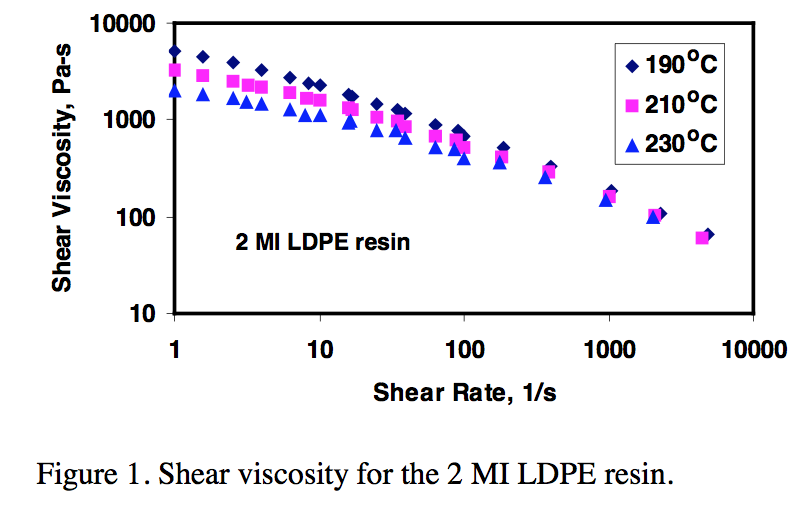
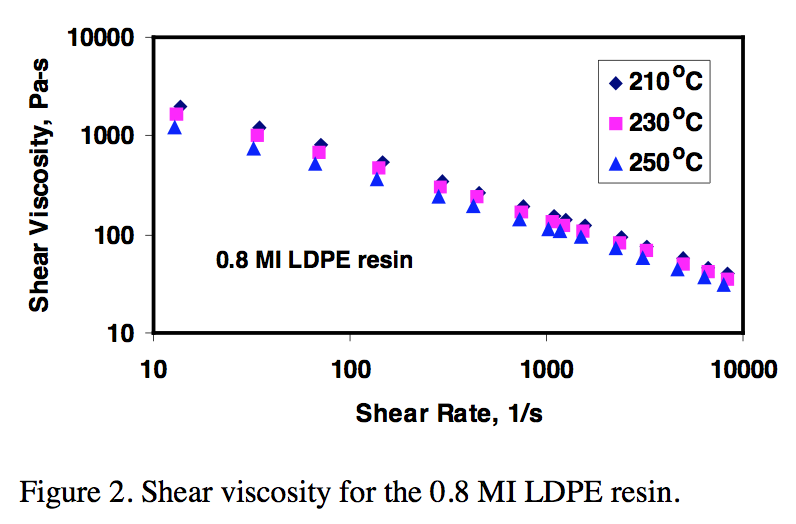
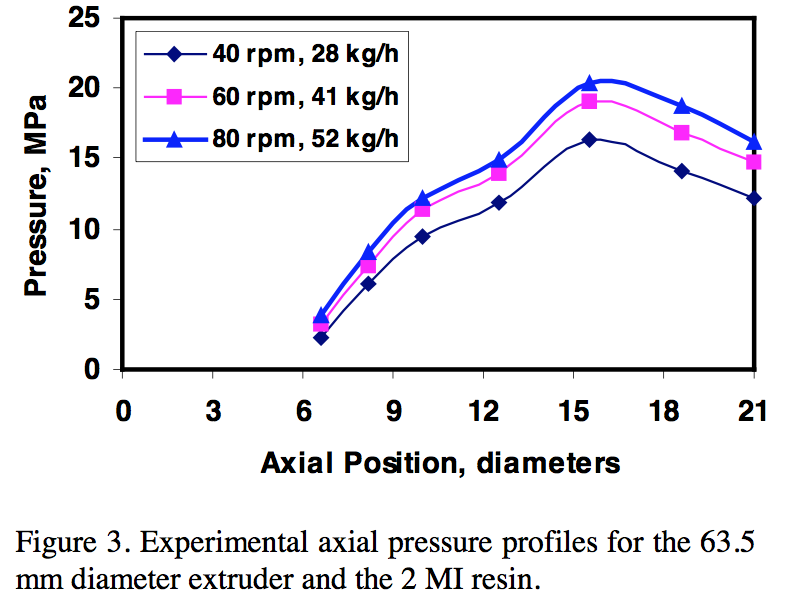
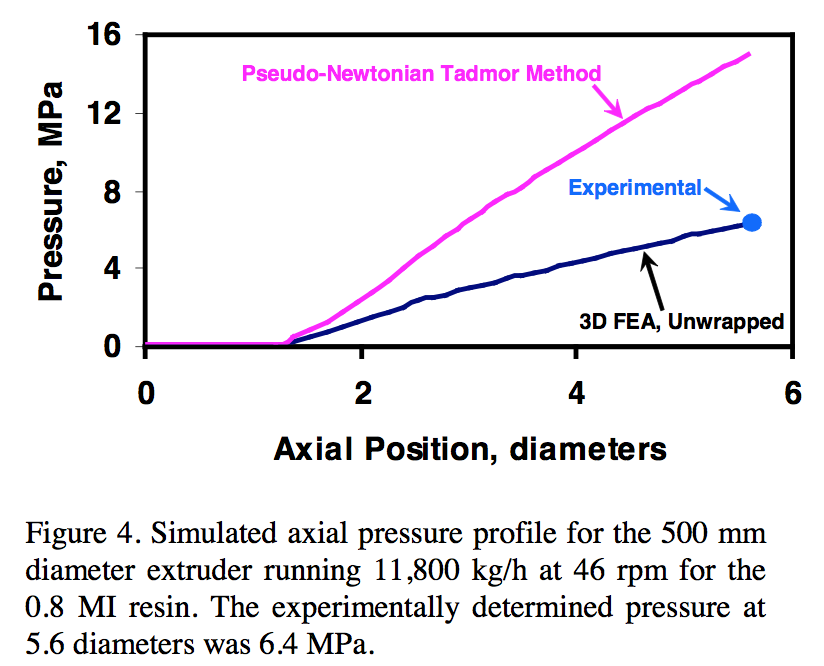
Return to
Best Papers.