Devolatization via Twin Screw Extrusion – Theory, Tips and Test Results¶
Plastics Extrusion Asia 2014
July 16, 2014
Charlie Martin, LeistritzIn a twin screw extruder (TSE), the mixing/blending of polymers/additives and devolatilization are masstransfer
operations dependent upon shear/energy that is being imparted into the materials being
processed by rotating screws. Devolatilization (DV) refers to the removal of unreacted monomer,
solvent, water and other undesirable materials from the process melt stream. There are many devices
that perform DV, including extruders. Almost always, the TSE includes the provision for devolatilization;
sometimes as a critical factor in the process, and sometimes as an after-thought.
Factors that effect devolatilization efficiencies, in any device, include:
1. Residence time under the vent or vents- longer is better but…
- Oxygen, shear, time and temperature may contribute to degradation and side reactions
(understand kinetics of degradation)
2. Surface area of the melt - higher is better
- Rolling pools and film effects
- Function of screw geometry and operating parameters
3. Surface renewal- higher is better
- Renewed surfaces come from rolling pools and partially filled screw channels
4. Bubbles are key: nucleation, growth and rupture
- Stripping agents can be injected to facilitate bubbles
5. Vacuum level applied to vent zone(s) – it can make a big difference
- Low viscosity material may require decreased vacuum levels
Materials are metered into the twin screw extruder and the screws rpm is independent and set to
optimize processing efficiencies. Melt pools are bounded by screw flights and barrel walls, which makes
extrusion, by definition a “small mass” continuous process that results in a high surface area of the
polymer melt. Rotating screws result in rolling pools and thin films, both of which improve DV.

Figure 1: Co-rotating intermeshing twin screw extruder screw set
Process control parameters include screw speed (rpm), feed rate, barrel/die temperatures, and vacuum
level. Typical readouts include melt pressure, melt temperature, motor amperage, and in-line optical
sensors. Depending on how the TSE is configured and operated, residence times can be as short as 5
seconds, as long as 10 minutes, and are typically in the 20 second to 2 minute range.
Starve feeding refers to the extruder being fed at a rate less than the forwarding efficiency of the screws.
The independence of feed rate from screws rpm facilitates control of surface area generation, residence
time, and mixing (to eliminate gradients); and is what makes the TSE an effective tool for stripping
volatiles from polymer melts.
Barrels segments include the provision for venting. The pressure gradient in the twin screw extruder is
controlled and, to a significant degree, determined by the selection of screws. Flighted elements are
strategically placed so that the screw channels are not filled, which results in a zero pressure
underneath vent sections that prevents vent flooding, and also allows downstream feeding of
fillers/fibers+.
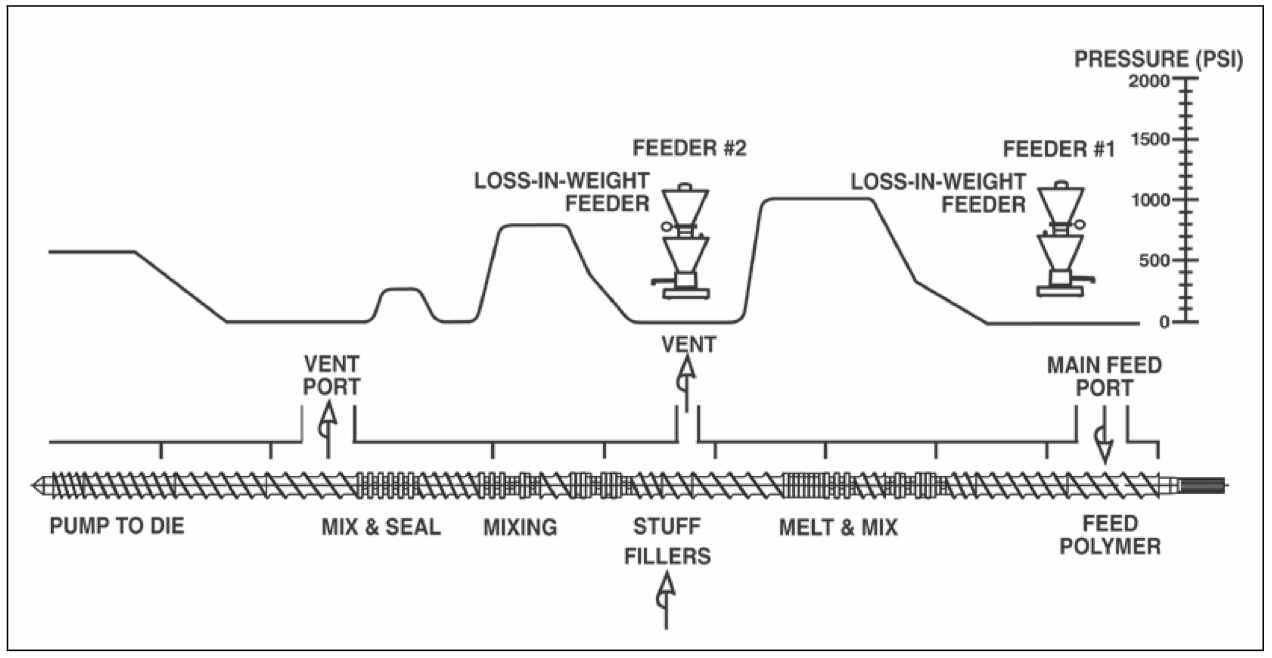
Figure 2: Pressure gradient in a starve fed twin screw extruder
The intense mixing associated with the short inter-screw mass transfer characteristics inherent with a
TSE makes it ideal to perform intimate mixing/blending. Simultaneously, entrapped air, moisture and
volatiles are removed by devolatilization, driven by the superheating of the volatile component and
exposing the melt pool to a rapid decompression under a vent.
The Length/Diameter ratio (L/D) represents the overall length of the process section divided by the
screw diameter. The L/D ratio is matched to downstream unit operations that need to be performed, and
typically ranges from 24/1 to 60/1+. Extended L/D’s allow for multi-stage venting and increased DV
efficiencies, as well as the feeding, mixing and pumping functions inherent with the process.
There are an infinite number of TSE screw element types. There are, however, only three basic types
of screw elements: flighted elements, mixing elements, and zoning elements. Flighted elements are
strategically placed to forward materials. Zoning elements isolate two operations within the extruder,
such as to facilitate a melt seal prior to a vacuum venting zone. Mixing elements can be dispersive
and/or distributive in nature, and often also serve as a dual purpose as a zoning element. Adequate
pumping elements are required under vents and at the TSE discharge to prevent vent flooding.
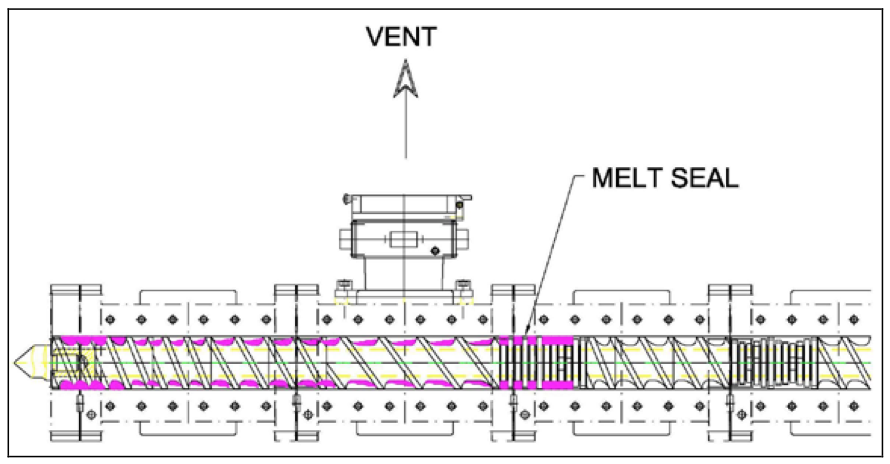
Figure 3: Vent/discharge from TSE
Screws are segmented and assembled on splined shafts. Torque is limited by the cross-section of the
shaft and its design. Free volume is related to the OD/ID ratio, which is defined by dividing the outside
diameter (OD) by the inside diameter (ID) of each screw. Asymmetrical splined shafts isolate the
tangential force vector being transmitted by the motor into the process and results in higher torque
capabilities from a smaller diameter shaft. Therefore, a 1.66/1 OD/ID ratio and deeper flights are
possible without decreased torque. Increased flight depths help prevent the melt from flying up the
vent, and higher free volume results in a higher surface area, which are preferred for DV processes.
See below for a comparison of common OD/ID ratios:
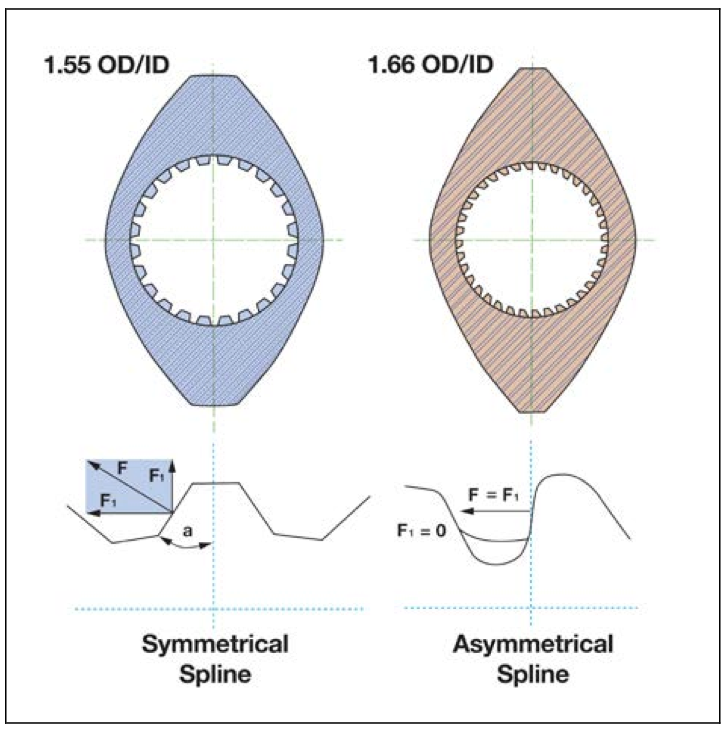
Figure 4: A comparison of TSE OD/ID ratios
Sometimes a stripping agent, such as water or a supercritical CO2, is injected into the TSE to augment
DV efficiencies. The L/D must be lengthened to accommodate this task, and the liquid is injected over
distributive mixers to prevent flashing/ponding. In the decompression zone bubbles grow and rupture,
releasing volatiles.
It’s evident that increasing the screws rpm and/or decreasing the rate generally improves DV
efficiencies, within the constraints of the formulation. Vents can be atmospheric, or vacuum can be
applied to further enhance devolatilization effects.
The following DV tests were performed:
Test #1: Devolatilization of copovidone (Kollidon® VA 64)/API/solvent (Methanol) formulations
A formulation using typical pharmaceutical ingredients was selected and a solvent was injected/removed
via DV to determine the results for different operating conditions. Specifically, a copovidone and
greosulfulvin active pharmaceutical ingredient(API) were metered into the TSE feed throat, and 5% of a
solvent was injected, mixed and then devolatilized in the TSE process section.
Experiments were performed at 2 and 4 kgs/hr and 200 and 400 screws rpm, with and without vacuum.
The temperature zones for the barrels were 60 C at the feed throat, transitioned to between 100-140 C
for the barrels, and 180 C at the die. The motor load was 40-50% for all runs. The melt temperature was
in the 180 deg. C range.
The following is a summary of the equipment: Two (2) loss-in-weight (LIW) metering feeders for polymer
and API, piston pump to inject the solvent, ZSE-27 MAXX co-rotating, intermeshing twin screw extruder
(28.3 mm dia. screws, 1.66/1 OD/ID ratio) with 40 to 1 L/D, 2 atmospheric vents and 1 vacuum vent,
strand die, air quench conveyor and pelletizer. The following represents the TSE process section and
screw design used for the experiments:
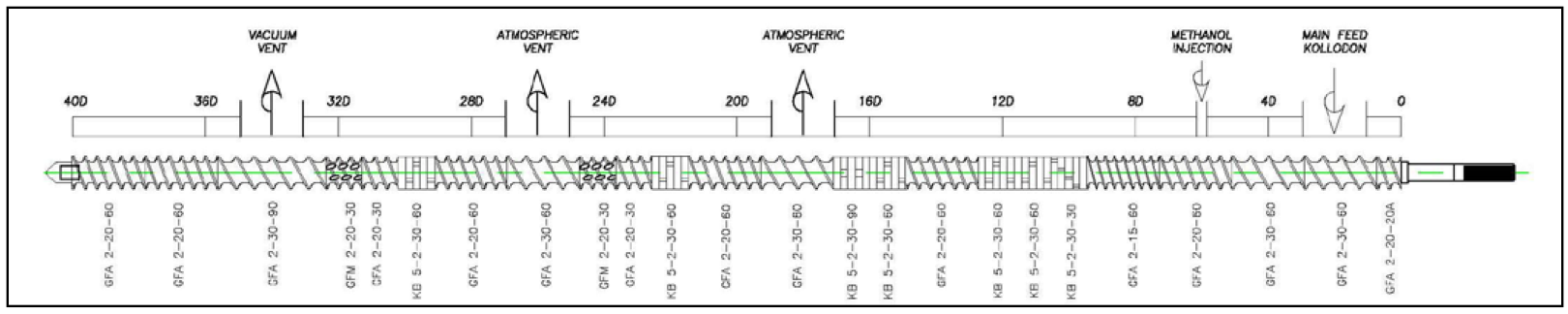
Figure 5: ZSE-27 MAXX screw/process section design
All samples were characterized using Gas Headspace Chromatography and are indicated below:
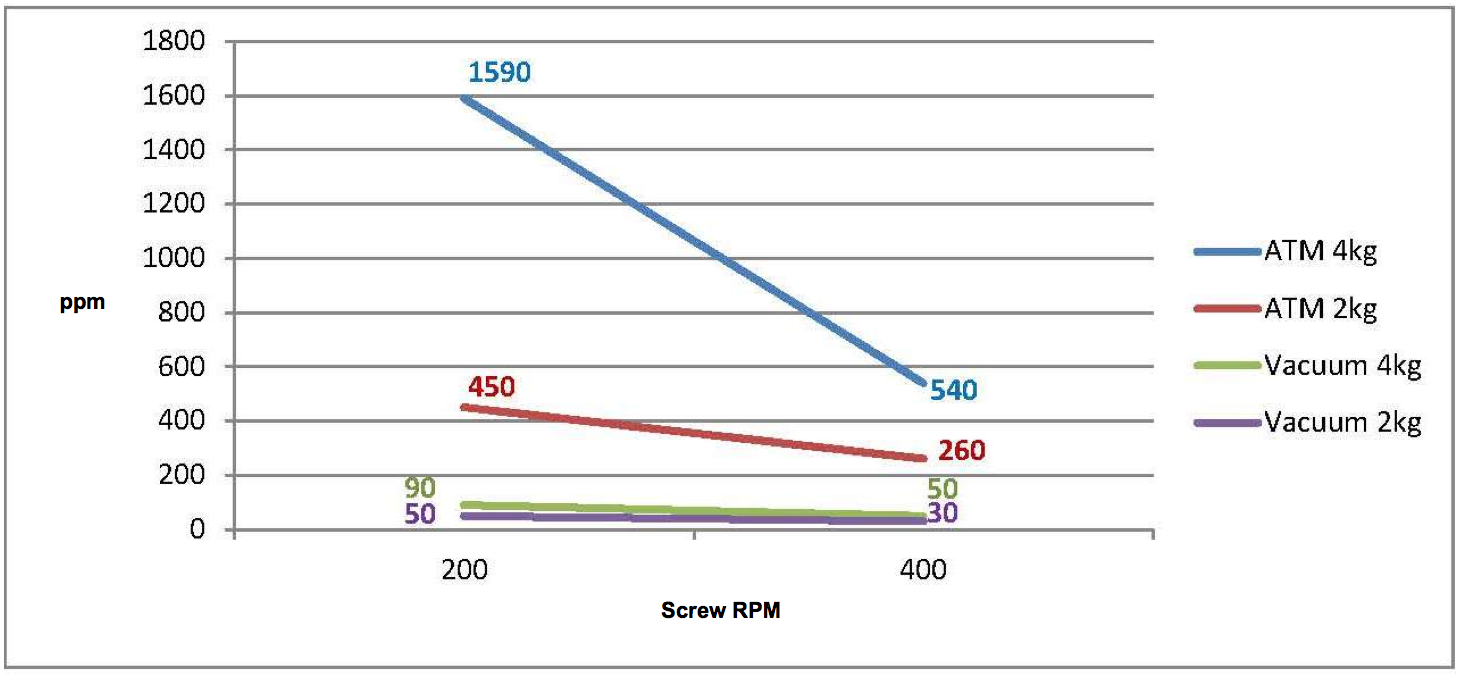
Figure 6: Residual solvent (in PPM) for various operating conditions
From the results the following conclusions may be stated:
1. There is a linear correlation between rpm and feed rate and reduction in volatiles concentration
2. The application of vacuum resulted in a significant reduction in concentration of volatiles
ppm
Test #2- Processing Undried PLA in a Co-rotating Twin Screw Extruder
PLA pellets (50%) and edge-trim (50%) were metered into the extruder at a total rate of 180 kgs/hr and
processed at 250 screws rpm. The temperature zones for the barrels were between 180 and 190 deg.
C. The motor load was approximately 70%. The melt temperature was 200 deg. C. Moisture analysis
indicated the PLA pellets had 1600-2000 PPM moisture content, and the regrind materials between
2800 and 4200 PPM.
The following is a summary of the equipment: (2) loss-in-weight (LIW) metering feeders, ZSE-50 MAXX
twin screw extruder (51.2 mm dia. screws), 1.66/1 OD/ID ratio, 40 to 1 L/D with a screw/barrel design to
optimize venting efficiencies, gear pump front-end attachment, slide plate screen changer (120 mm
diameter breaker plate), 800 mm wide flexible lip sheet die, 3-roll stack with pull roll station and torque
winder. Three (3) venting sections were integrated into the process section, as indicated below:
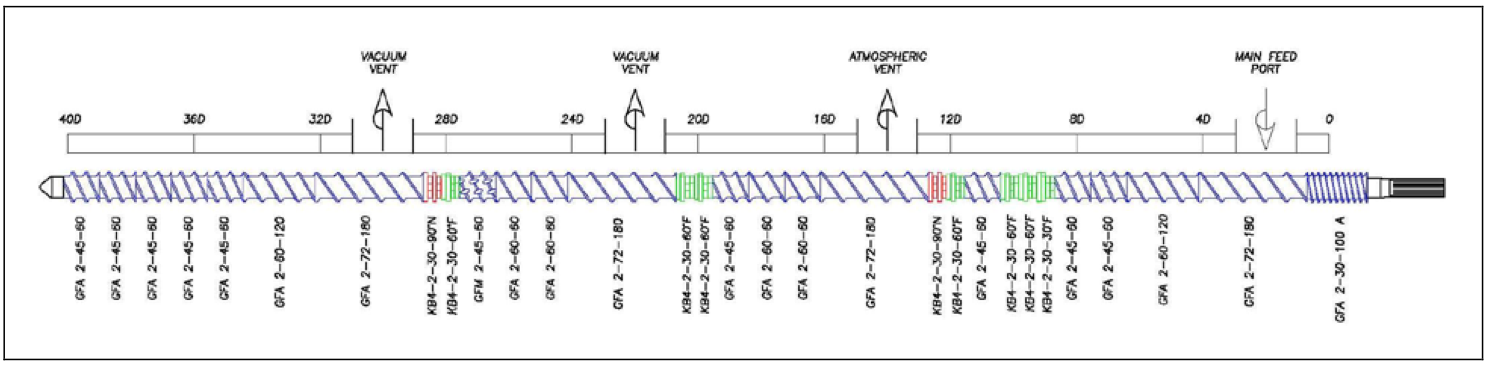
Figure 7: ZSE-50 MAXX screw/process section design
The sheet sample was dimensionally stable with an acceptable appearance. Analysis of the sheet
samples indicated a molecular weight loss of between 5 and 8%, as indicated below, which was deemed
successful for this application.
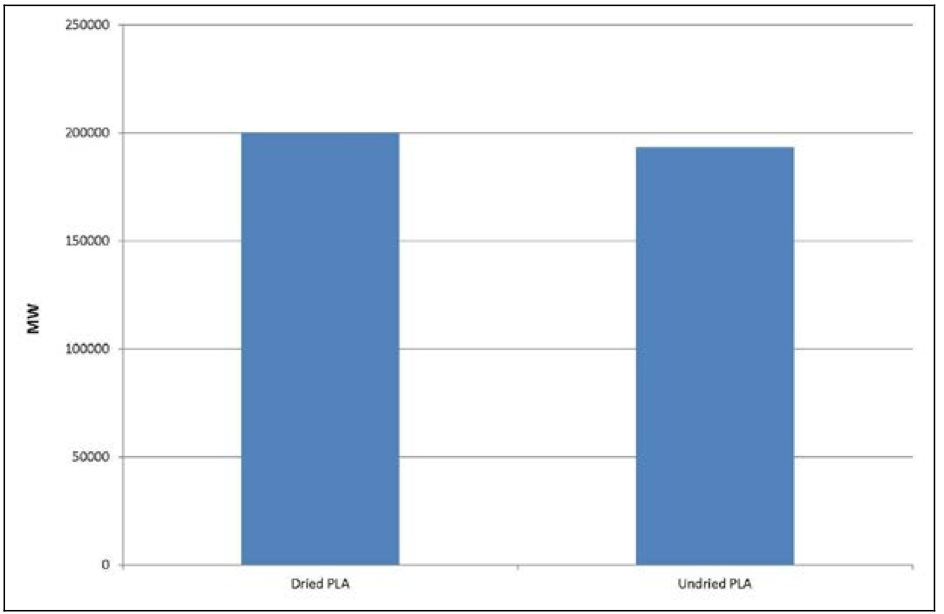
Figure 8: Comparison molecular weights dried vs undried samples
Vacuum System Designs/Applications
Vacuum systems are often maintenance intensive. Each system component must be carefully specified
for the intended purpose with regard to protecting the pump and cleaning/maintenance. These are
typical system components that are part of a vacuum system:
Vent stack: The vent stack is a housing that incorporates several devices, including: sight glass in a
hinged cover, O-ring seal, pipe connection for vacuum hose, connections for air bleed valve, vacuum
transducer, etc. A drool tray should be integrated into the design for housekeeping/maintenance
purposes. At the bottom of the vent stack is a barrel insert, which has one or more slots, and is angled
and contoured to prevent vent flow. The vent stack is usually heated enough by conduction from the
barrel, however for some polymers (i.e. PET) it is heated to make it semi-self-cleaning.
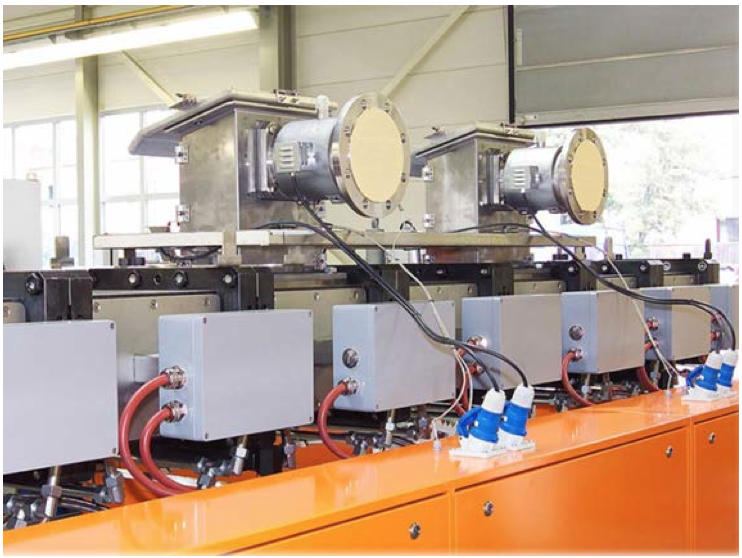
Figure 9: Heated vent stack
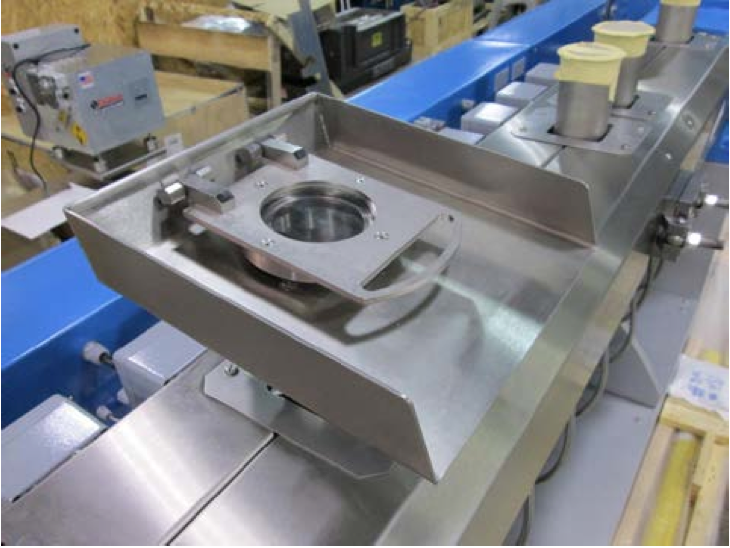
Figure 10: Drool tray
Interconnection plumbing: Typically this is a rubber hose. Sometimes it helps to heat a pipe from the
vent stack to the knock-out pot to prevent the melt from freezing off and blocking the pipe. Plumbing
should be pitched downward toward the knock-out pot to allow materials to fall by gravity into the pot.
Knock-out pot: The “K/O” pot is the 1st vessel the vent-stream encounters after exiting the extruder
vent and will collect the most solids/liquids, if present. A dual-chamber K/O pot with internal baffles is
ideal. Baffles cause the vent stream to change direction that results in materials collecting at the
bottom of the vessel. The K/O pot should be situated as close to the extruder vent as possible.
Liquid condenser: A liquid condenser, typically cooled by water, is required based on the composition
of the vent-stream. Low-viscosity liquids will drain from the housing simply by opening a valve at the
bottom, whereas “gelled” liquids require the vessel to be opened and manually cleaned. To design the
system, it is important to define the residual materials being condensed.
Dry filter: A dry filter is the last line of defense to protect the pump, and is simply a filter element inside
a sheet-metal canister with quick-release clamps. Filter elements are often polyester, with many other
materials of construction also available.
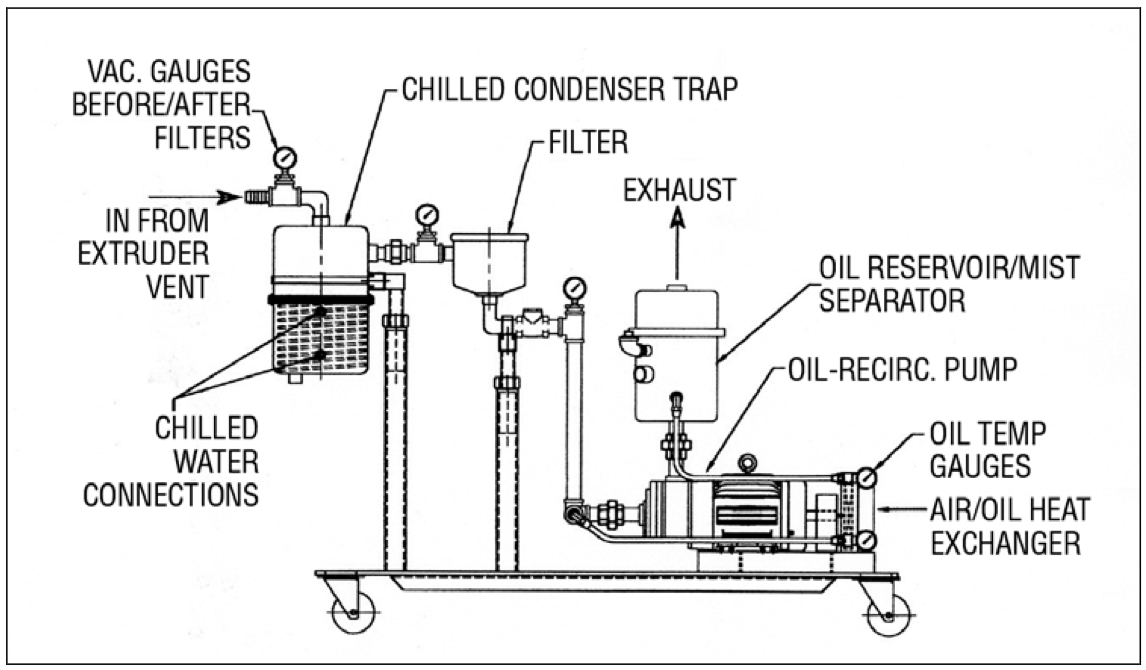
Figure 11: Example of vacuum venting system components
Vacuum pump: The vacuum pump is what pulls the vacuum that removes volatiles from the extruder
vent. There is often confusion about sizing vacuum pumps because there isn’t a calculation to define
the correct size for any given extruder. Larger motors/pumps only increases volumetric pumping
capacities, so beyond a certain capacity there’s little benefit for a larger pump since it is pulling a
vacuum on a finite/closed area. For most processes a moderate vacuum (i.e. 26-28” HG, 100-50 Torr,
130-60 millibar) is generally acceptable. That being said, some processes (such as processing undried
PET) benefit from a higher vacuum levels, in which case a 2-stage pump to facilitate deeper vacuum
levels may be specified.
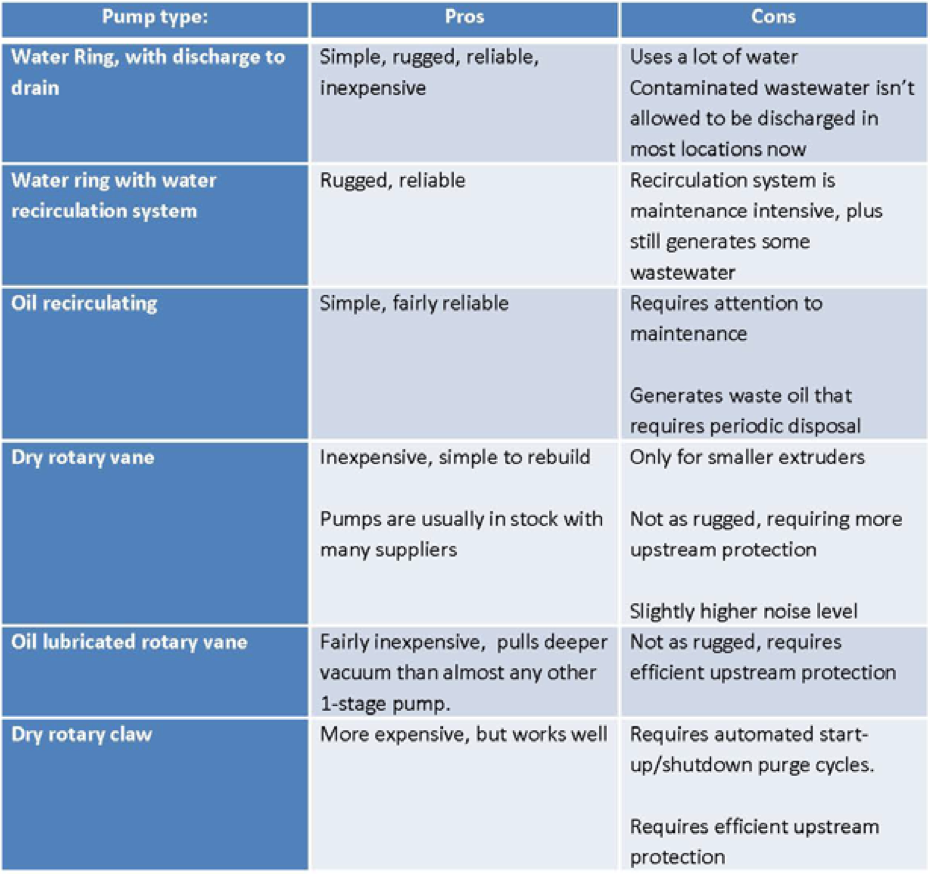
Figure 12: Vacuum pump types
The following are some tips and techniques to assist the venting process:
Vent stuffer: A vent stuffer is co-rotating intermeshing twin screw auger that pushes materials back
into the extruder process section that might “fly out” due to a high vent vapor velocity and/or low melt
viscosity materials being pulled by the vacuum. It can be designed to operate with vacuum, or to allow
downward discharge/draining, as might be the case if 10%+ water is being devolatilized.

Figure 12: Vacuum vent stuffer
Vent position: Thirty years ago most vent ports were located about 6 L/D from the TSE discharge.
Technology developments have allowed higher screws speed so the same diameter screws can process
3 or 4 times previously attainable rates with dramatically reduced residence times. In addition to die
modifications, placing the vent about 10 L/D back from the discharge allows for more stable pumping
and better venting efficiencies.
Multiple vents: Each vent can decrease the level of volatiles by a quantum leap. Early vents are often
atmospheric, while vacuum is often applied to later vents. For each vent the overall L/D of the extruder
must become longer. For co-rotating and counterrotating intermeshing twin screw extruders a 60/1 L/D
is about the practical limit. Non-intermeshing counterrotating twin screw extruders can be longer.
Instrumentation: A vacuum transducer should be integrated into the vent piping. The transducer can
be connected to a PLC system for control, data acquisition and alarming.
Vent cleaning tips: Operators should only use wood or plastic scrapers when cleaning the vent
stack/insert. Many screw shafts and gearboxes have been broken by operators cleaning the vent with
a screw driver or brass scraper with the screws rotating. Also, only use a flashlight and a mirror
attached to a pole to visually check a vent to avoid hazardous vapors and burns.
Summary
Any extruder with a vent is devolatilizing something. Curiously, despite the commercial significance of
devolatilization, there are only three texts on the subject. One is out of print, one is translated from
German, and the 3rd, Devolatilization of Polymers by Dr. Joseph Biesenberger, was published in 1983.
It is generally recognized that there is a lack of current DV modelling available. That being said, TSE’s
are well proven in wide ranging industrial settings and broad know-how exists, as indicated by the
extensive patent literature on the subject.
The test results reflected above are synced with generally accepted DV principles and practices.
Understanding basic thermodynamic principles and functions/maintenance of the vacuum system, as
well as some tricks, goes a long way to ensure successful utilization/improvement of devolatilization via
twin screw extrusion.
REFERENCES
1. Biesenberger J.A.; Devolatilization of Polymers: Fundamentals – Equipment – Applications,
Hanser Publishers (1983).
2. Jerman R.E.; “Devolatilization of Polymers via TSE”, Leistritz Twin Screw Extrusion Workshop
proceedings (2006).
3. Todd D.B., Zhu L.; “Polymer Devolatilization”, Leistritz Twin Screw Extrusion Workshop
proceedings (2011).
4. Martin C.; “Twin Screw Extrusion System Developments to Process Bioplastics”, SPE Bioplastics
(2012).
5. Martin C.; “Devolatilization via Twin Screw Extrusion: Theory, Tips and Results”, PPS (2014).
Return to
Paper of the Month.