Improving Thermal Efficiency of Single Screw Extrusion
A. L. Kelly, J. Vera Sorroche, E. C. Brown, P.D. Coates
IRC in Polymer Engineering, University of Bradford, Bradford, UK, BD7 1DPAbstract
Thermal issues associated with polymer melt
extrusion are important but complex in nature. The
process efficiency associated with melting and conveying
polymers using a rotating screw inside a barrel is highly
dependent upon the frictional, thermal and rheological
properties of the polymer, the selected screw geometry,
and designated extruder operating conditions including
machine set temperatures and screw speed. Melt quality
is also of paramount importance and can be defined in
terms of the value and homogeneity of melt temperature.
In this work, in-process monitoring techniques
incorporating thermocouple grid sensors, infra-red
thermometers and an energy meter have enabled real-time
characterization of thermal dynamics in single screw
extrusion, for a 63.5mm diameter extruder. Two
commercial grades of polyethylene have been investigated
using three extruder screw geometries at different
extrusion operating conditions to gather evidence relating
to process thermal efficiency. Extruder screw geometry,
screw rotation speed, extruder set temperatures and
material properties were each found to have a significant
effect on the thermal homogeneity of the melt and on
process energy consumed.
Introduction
The polymer processing industry is energy intensive
since it involves rapid melting, forming and solidification
of materials at high throughputs. Two mechanisms are
responsible for melting the polymer within the extruder,
namely thermal conduction from electrical heaters along
the length of the barrel and viscous shearing caused by the
rotation of the screw inside the barrel. For each kg of
polymer processed it is necessary to supply, on average,
0.3kW/kg/hr [1]. Typically polymer processing plants
comprise extruders and other processing machinery,
together with polymer drying equipment, chiller units for
cooling water, compressors for conveying materials and
service air and other ancillary equipment. The extrusion
process is central to the industry [1, 2] and this stage
typically represents around 50% of the total process
energy used.
Output quality from the extrusion stage of any
process is an input factor for subsequent stages including
injection molding, film blowing and casting. In addition
to determining final product quality, input variation has a
considerable impact on the efficiency of other stages of
polymer processing. Variation in polymer feedstock is responsible for increased set-up times, and a cumulative
effect on further processing fluctuations. Quality must be
defined in terms of both optimal value and homogeneity
of the product. In order to minimize process variation,
extruders are commonly operated at conservative
throughput rates to minimize process variation. In
addition, extruders are often operated with general
purpose extruder screw geometries which are not suited to
the polymer being used, either through lack of
understanding or financial restrictions. The driver to
operate efficiently within industry has tended to link with
production outputs rather than optimization of process
energy consumption. Extruders are not commonly
equipped with energy monitoring equipment, and as a
result there is little understanding of the links between
processing conditions and energy consumption.
This study aims to consider the effect of extruder
screw design and extrusion operating conditions on
thermal efficiency in terms of both energy consumption
and melt quality, defined in terms of thermal
homogeneity, and contributes to a wider research project
to provide the polymer industry with tools to optimize
energy efficiency using a whole systems approach.
Melt Temperature Measurement
Single screw extruders are controlled by setting
barrel and die temperatures and screw rotation speed.
Melt temperature is widely acknowledged as being one of
the key variables in polymer extrusion which directly
influences process stability and product quality. However,
most extruders are supplied with only wall temperature
measurement capability, usually through a thermocouple
flush mounted at the extruder die wall, the output of
which is heavily dependent upon the temperature of the
metal wall rather than the flowing melt. [4]
Sensors based on grids of thermocouple wires placed
within the melt flow [5] have been used to
comprehensively investigate melt temperature profiles
and temperature variation in extrusion. These
thermocouple meshes employ unsheathed thermocouple
wires of small diameter to minimize any flow disturbance
and cut response time. Wires of opposing polarity are
fused together to form thermocouple junctions whose
e.m.f. is related to measured temperature at that point.
Using this technique, the effect of extruder screw speed,
polymer type and screw geometry have been measured [6.7]. Although not robust in production environments,
such sensors are a powerful research tool.
Experimental
Real-time quantification of energy consumption was
achieved using a 3-phase unbalanced loads energy meter
(Hioki 3169) connected to the 3-phase power supply to
the extruder. This measured total energy consumption of
the extrusion process, including consumption by the
motor, heaters and cooling fans.
Two grades of high density polyethylene (HDPE)
were selected for this study to allow investigation into
material effects on thermal efficiency. The first material
is a linear high density polyethylene copolymer grade
with a narrow molecular weight distribution having a
quoted melt flow index (MFI) of 4.0 g/10min (2.16kg,
190°C). (Rigidex HD5050EA, Ineos) The second
material is a high molecular weight copolymer grade
supplied for blow moulding applications and having a
quoted melt flow index (MFI) of 0.12 g/10min (2.16kg,
190°C). (Rigidex HM5411EA, Ineos)
Measurements were conducted on a 63.5mm
diameter single screw extruder (Davis Standard BC60) in
an instrumented adaptor section of the extruder where
internal diameter was 38mm. A schematic diagram of
this measurement region is shown in Figure 1. Thermal
homogeneity was assessed here using thermocouple grid
and infra-red techniques. The design of the thermocouple
grid incorporated seven junctions located on a central axis
across the flow channel in a non-symmetrical spacing. A
diagram is shown in Figure 2. The thermocouple grid
was located at the entrance to a 6mm diameter rod die. In
addition, measurements from a wall thermocouple (3mm
diameter J-type) and an insulated J-type thermocouple of
0.5mm diameter protruding 1.0mm into the flow were
made in this instrumented adaptor section prior to the die
Melt pressure was monitored in this adaptor section using
a Dynisco PT422A pressure transducer. Melt temperature
in the screw channel close to the end of the extruder
screw was monitored using an infrared temperature sensor
(Dynisco MTX) flush mounted to the barrel surface.
Three extruder screws were used having a length to
diameter ratio of 24:1. Figure 3 provides schematic
representations of the screw designs. These polyolefin
screw designs were selected to provide a comparison of
melting conditions with screws typically used in the
polymer industry. They were not designed specifically
for the materials used in this study.
Experiments were carried out at a range of extruder
screw speeds from 10 – 90 rpm in steps of 20 rpm, and
sufficient time was allowed for conditions to stabilize at
each screw speed. All measurements were made at a frequency of 10 Hz. Three set temperature conditions
were used for each material and are detailed in Tables 1 to
4. Where possible the same set temperatures were used to
for the two polymers and three screw geometries.
However, where this was not possible (for example
because of excessive extruder torque or irregular solids
conveying) set temperatures were adjusted to maintain a
stable extrusion process. Most notably, HM5411EA with
the barrier flighted screw required significantly higher
temperatures in the feed zones than the two single flighted
screws, presumably to allow the polymer to be
sufficiently soft to flow over the barrier flight at the start
of the melting zone.
Results and Discussion¶
Data are presented to show the effects of screw
geometry, set machine temperatures, material properties
(viscosity) and material throughput (controlled by screw
speed) on melt quality, measured in terms of temperature
and temperature homogeneity, and on total energy
consumption. A comparison of complex viscosity of the
two grades of HDPE is shown in Figure 4, from
oscillatory rheometry at a set temperature of 200°C. It is
clear that viscosity is significantly different for each of the
selected materials reflecting a difference in molecular
weight. HM5411EA (pipe extrusion grade) exhibited a
higher viscosity than HD5050EA (injection / blow
molding grade) as could be expected to suit these
processes.
Thermal homogeneity is represented by melt
temperature profiles (averaged over a period of 1 minute)
in the entrance to the extruder die, measured using the
thermocouple grid. Figures 5 and 6 show the effect of set
temperature, screw geometry and screw speed on the melt
temperature of both grades of HDPE. These figures show
that generally melt temperature was highest in the centre
of the flow and increasing with increasing set
temperatures as could be expected. The most noticeable
difference between the three screw geometries was the
inability of the single flighted screws to maintain
temperatures above the set barrel and die temperatures at
high screw speeds, indicating poor or incomplete melting
of the polymer at these conditions. The barrier flighted
screw performed significantly better, highlighting the
improved melting performance of the barrier flight and
spiral mixer. The same general trends were observed with
both grades of HDPE, with slight differences. At
intermediate screw speeds (50rpm) peak melt temperature
measured in the centre of the flow were greater for the
high viscosity HM5411EA grade, although at high screw
speed (90rpm) the same polymer showed a more
significant variation across the flow path and lower
minimum temperatures than HD5050EA (for example
compare figure 5a and 6a).
The effect of screw geometry is compared directly at
low (10rpm) and high (90rpm) screw speeds for both
grades of HDPE at 220°C in figure 7. For HD5050EA
(figure 7a) there was negligible difference between the
measured temperature profiles at low screw speed and
relatively minor differences at high screw speed regions
close to the die wall. At this condition, melt temperature
was highest with the barrier flighted screw and lowest
with the stepped compression screw. For HM5411EA at
low and high screw speeds (figure 7b), melt temperature
was lowest with the gradual compression screw and
highest with the barrier flighted screw, significantly so at
high screw speed. This highlights the dependence of melt
viscosity on the thermal dynamics of the extrusion
process; the high viscosity of this grade of HDPE leads to
a high dependence on screw geometry. A difference in
measured temperature of 80°C was observed at
approximately 12-15mm from the centre of flow between
the barrier flighted and stepped transition screws.
The effect of screw speed on radial melt temperature
profiles measured using the thermocouple grid are
displayed for HD5050EA with the stepped compression
screw at 220°C in figure 8. At low speeds of 10 and 30
rpm the temperature profile generated by the stepped
compression screw was very similar with the bulk of
polymer in the centre of the flow and decreased towards
the die wall. At high screw speeds the temperature profile
exhibited dips in melt temperature near to the die wall.
These results have been explained by poor or incomplete
melting at high screw speeds with this screw and the
gradual compression screw (results not shown here) and
highlight the large variation in melt temperature with
radial position across the flow path.
Stability of melt temperature is also an important
feature which affects melt and product quality. As the
above temperature profiles displayed average temperature
measurements made over a period of one minute, it is
important to also consider temporal variations in melt
temperature. Melt temperature variation is displayed for
both grades of HDPE in figure 9. Levels of temperature
variation were lower for HD5050EA compared to
HM5411EA, reflecting the lower viscosity and relative
ease of melting of this polymer. At high screw speeds
temperature variation was lowest with the barrier flighted
screw for both polymer grades. Variation in melt pressure
for both polymers and three screw types with extruder
screw speed is displayed in figure 10 at a set temperature
of 200°C. Pressure variation for HD5050EA was
approximately 10 times lower than that measured for
HM5411EA at the same conditions, again reflecting the
challenging nature of the highly viscous grade. At high
screw speed, the barrier flighted screw produced lowest
levels of variation for HM5411EA.
Energy consumption per unit output is critical to the
performance and efficiency of the extrusion process.
Figure 11 displays measured energy consumption data for
both polymer grades with each extruder screw and set
temperature. Clearly, lower energy consumption was
required for the lower viscosity HDPE at all screw and set
temperature conditions, reflecting the lower energy
required to melt this grade by viscous shear. The extruder
consumed lower energy with the barrier flighted screw at
low screw speeds for both polymers. With HD5050EA
negligible difference was detected between energy
consumption of the two single flighted screws whereas for
HM5411EA the stepped compression screw required
highest levels of energy consumption per unit output.
These measurements reflect the potential cost implications
of careful selection of screw geometry for a particular
polymer and application. It is envisaged that by further
investigation of the variables considered within this paper,
for a wider range of polymer types and extruder screw
geometries, a greater understanding of the performance of
single screw extruders can be established. With analysis
of scale up and use of CFD simulation, the authors aim to
provide useful optimization tools to aid extrusion
processors.
Conclusions
The thermal efficiency of the single screw extrusion
process has been investigated using a range of in-process
measurement techniques for two grades of high density
polyethylene and three extruder screw geometries. The
results reflected high levels of variation in radial
temperature across the melt flow, dependent on screw
geometry, screw rotation speed and polymer type.
Significant differences in the melt temperature profiles of
two grades of HDPE suggested that melt viscosity played
an important role in the melting process. Energy
consumption per unit mass of polymer was significantly
higher for the higher viscosity grade of HDPE, and was
dependent upon screw geometry.
References
1. R. Kent, Plast., Rubb. Comp. 37 96-104 (2008)
2. M.J. Stevens and J.A. Covas, Extruder Principles and
Operation, 2nd ed., Chapman and Hall, London
(1995).
3. C. Rauwendaal, Polymer Extrusion, 2nd ed., Hanser,
Munich (1990).
4. X. Shen, R. Malloy, J. Pacini, SPE ANTEC Tech.
papers 918-926 (1992)
5. E. C. Brown, A. L. Kelly, P. D. Coates, Rev.Sci.
Instrum. 75 (11) 4742-748 (2004)
6. A. L. Kelly, E. C. Brown, P. D. Coates, Polym. Eng.
Sci. 46 (12) 1706-1714 (2006)
7. A. L. Kelly, E. C. Brown, K. Howell, P. D. Coates,
Plast. Rubb. Comp. 37, 151-157 (2008)
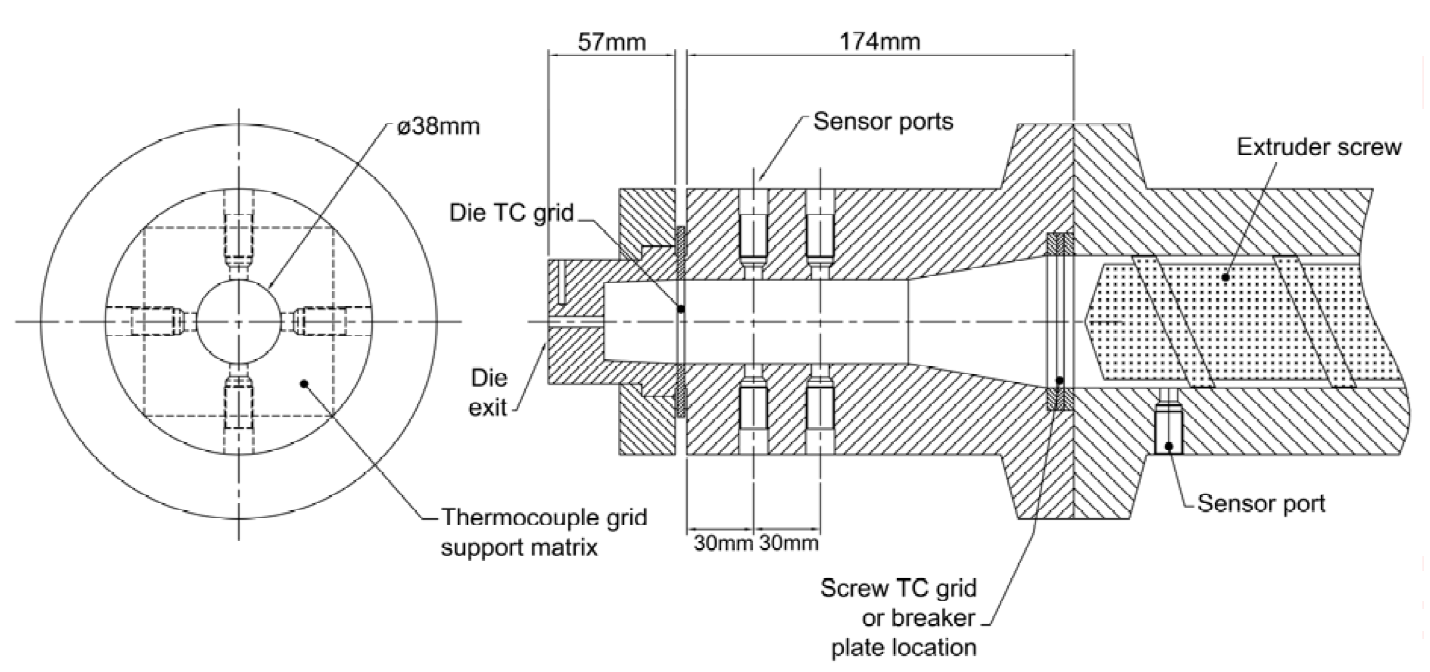
Figure 1 Instrumented extruder die
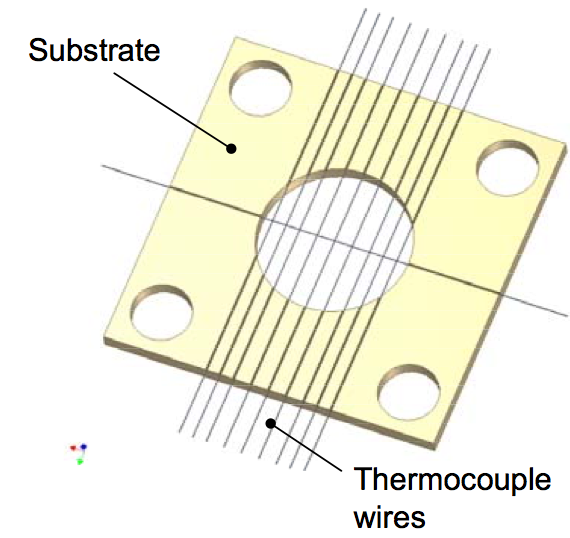
Figure 2 Thermocouple mesh sensor
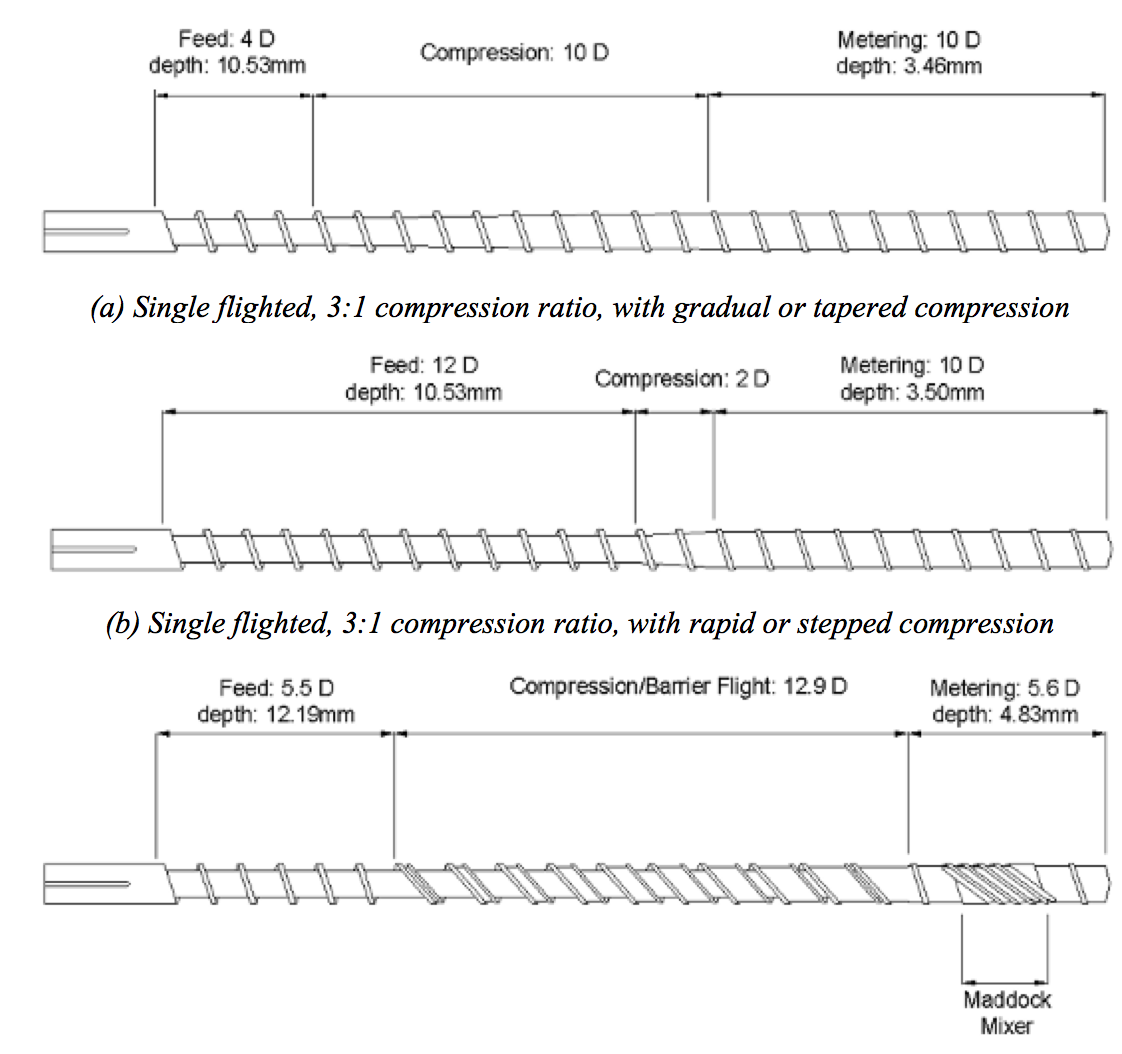
Figure 3 Extruder screw geometries
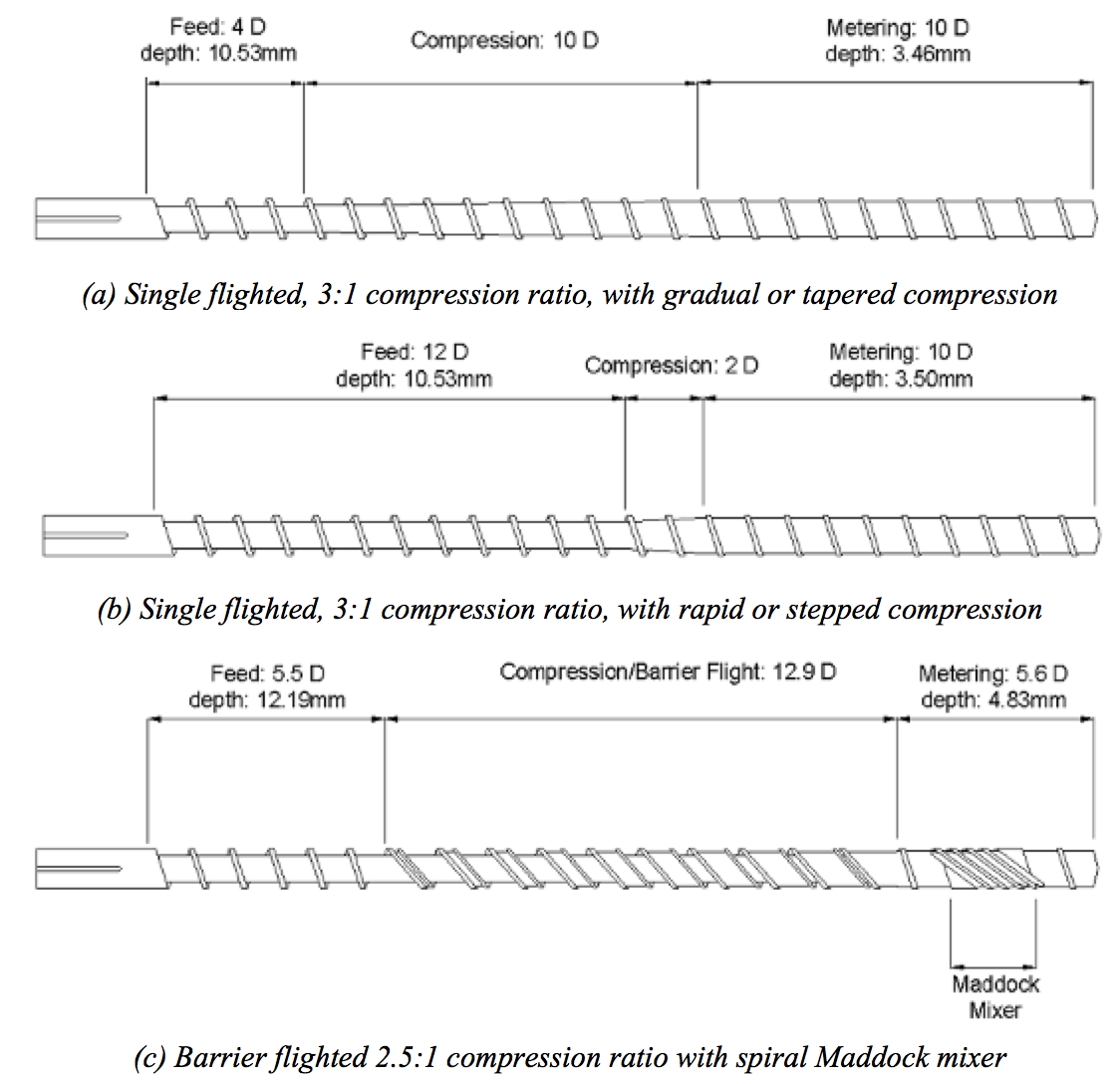
Figure 4 Comparison of complex viscosity at 200°C
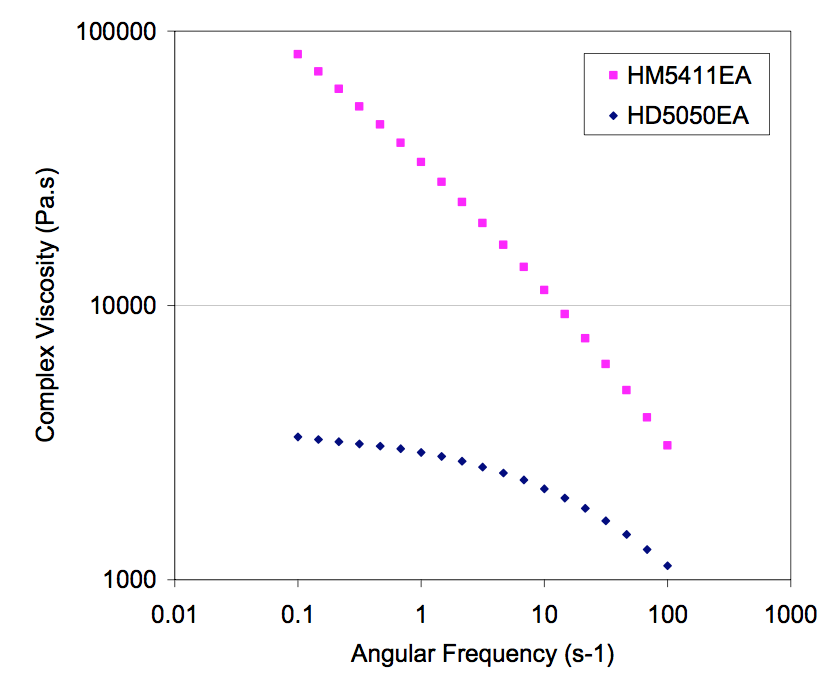
Figure 5 Effect of set temperature on measured melt temperature profile; HD5050EA at screw speeds of 50 and 90rpm
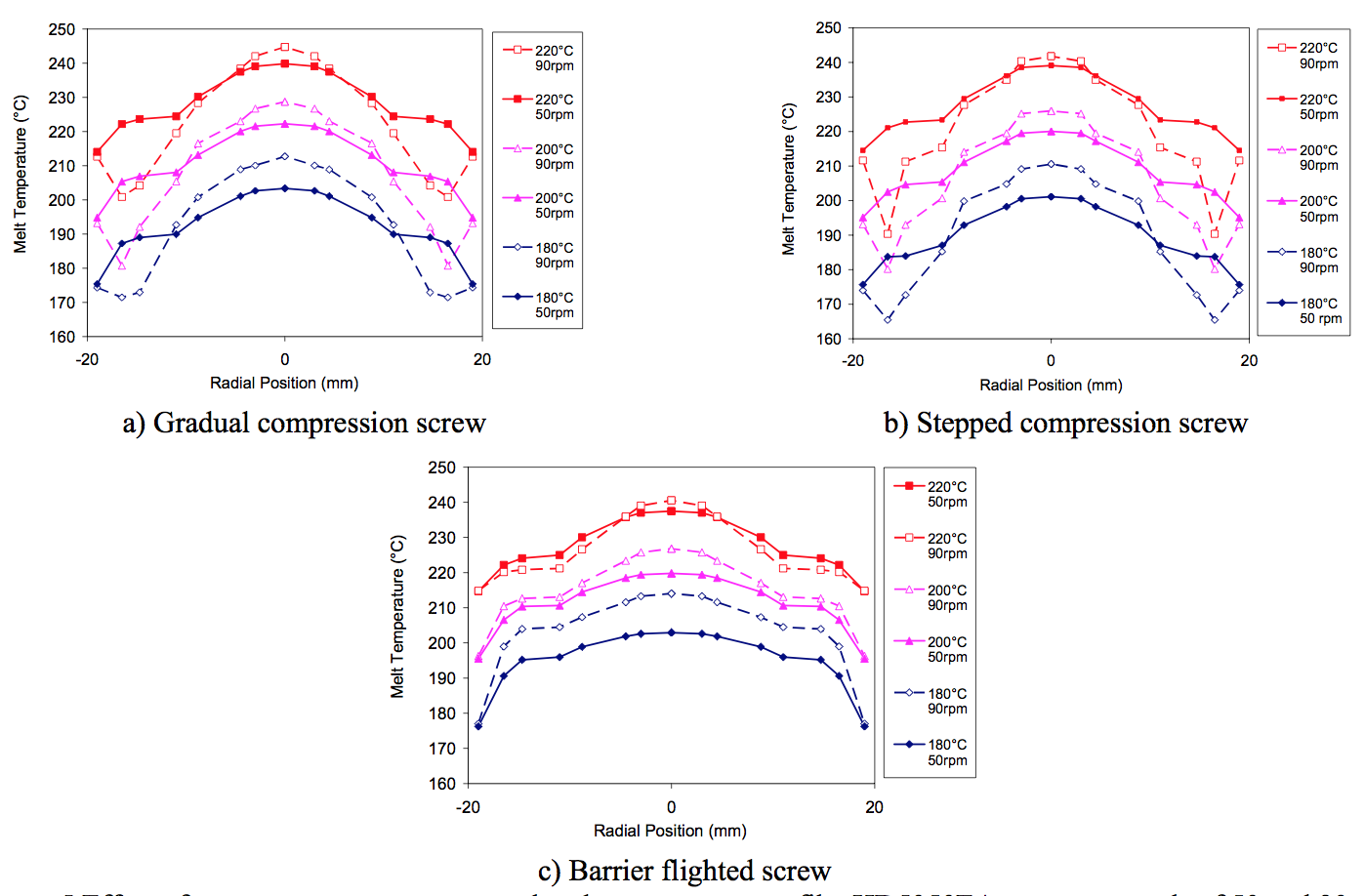
Figure 6 Effect of set temperature on measured melt temperature profile; HM5411EA at screw speeds of 50 and 90rpm
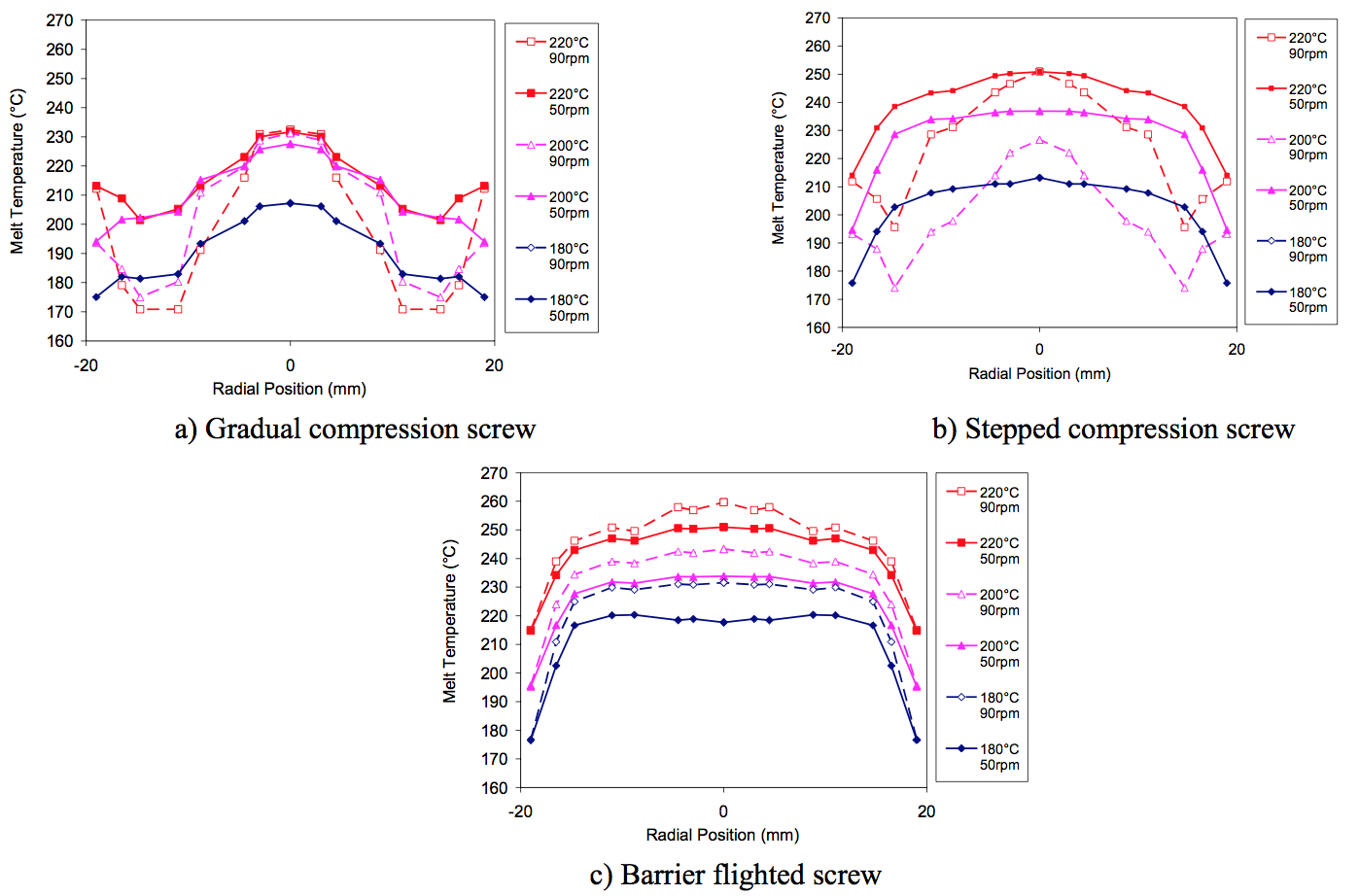
Figure 7 Effect of screw geometry and screw speed on melt temperature profile at a set temperature of 220°C
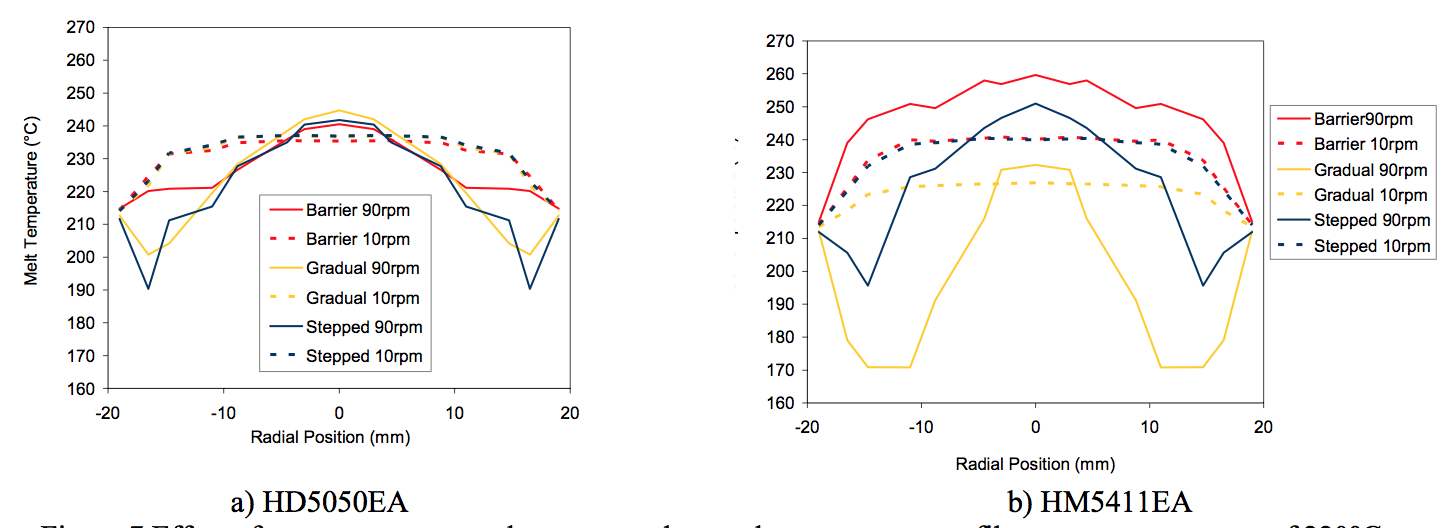
Figure 8 Effect of screw speed on melt temperature profile of HD5050EA at 220°C; stepped compression screw
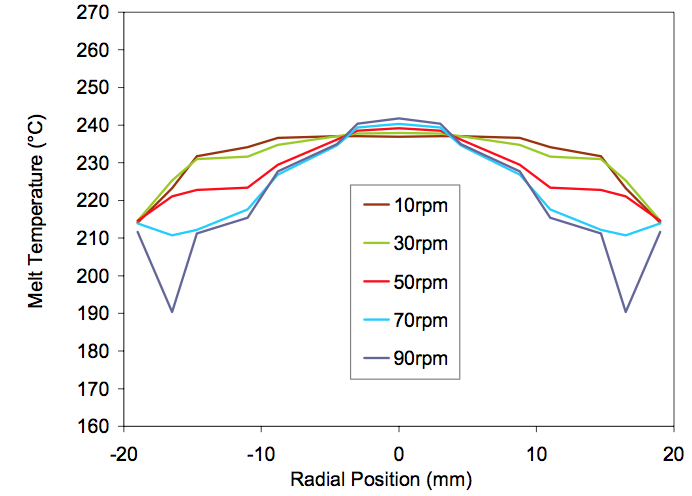
Figure 9 Melt temperature homogeneity; effect of screw geometry and screw rotation speed
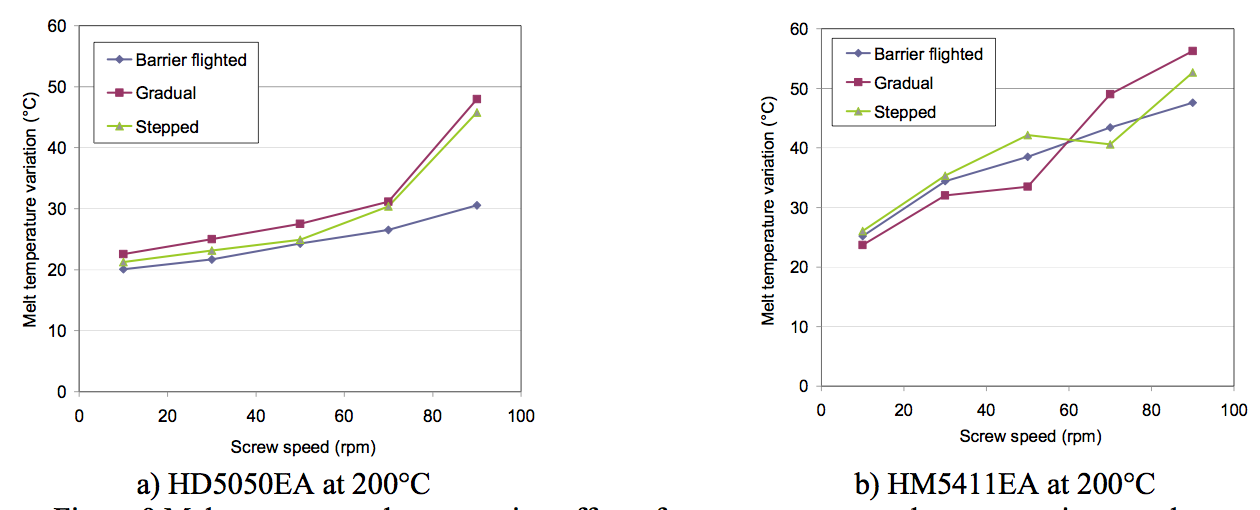
Figure 10 Measured pressure variation; effect of screw geometry and screw rotation speed
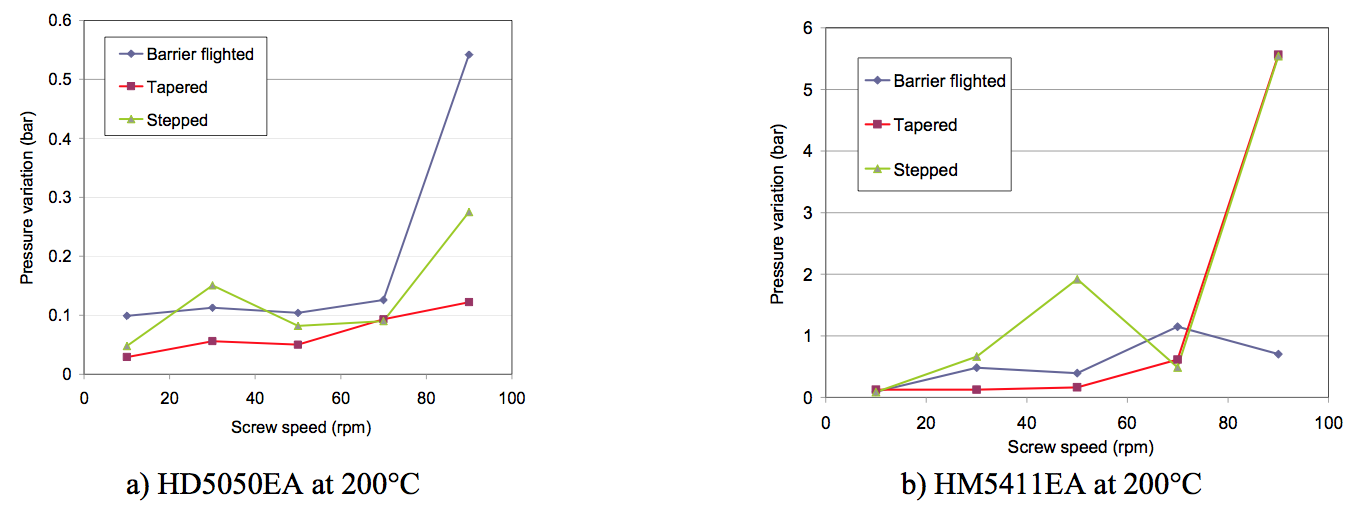
Figure 11 Measured extruder energy consumption; effect of screw geometry and screw rotation speed

Table 1: Extruder set temperatures for HDPE 5050EA for all 3 screw geometries

Table 2: Extruder set temperatures for HDPE 5411EA for the gradual compression screw

Table 3: Extruder set temperatures for HDPE 5411EA for the rapid compression screw

Table 4: Extruder set temperatures for HDPE 5411EA for the barrier flighted screw
Return to
Paper of the Month.