Modeling of Non-Isothermal Film Blowing Process for Non-Newtonian Fluids by Using Variational Principles
Martin Zatloukal
1,2, Roman Kolarik
1,21 Polymer Centre, Faculty of Technology, Tomas Bata University in Zlín, nám. T. G. Masaryka 275,
762 72 Zlín, Czech Republic
2 Centre of Polymer Systems, Tomas Bata University in Zlín, nám. T. G. Masaryka 5555,
760 01 Zlín, Czech Republic
Abstract
In this work, non-isothermal film blowing process
analysis for non-Newtonian polymer melts has been
performed theoretically by using minimum energy
approach and the obtained predictions were compared
with both, theoretical and experimental data (internal
bubble pressure, take-up force, bubble shape, velocity and
temperature profiles) taken from the open literature. For
this purpose, recently proposed generalized Newtonian
fluid depending on three principal invariants of the
deformation rate tensor, D, and its absolute defined as (square-root of D*D) has been used. It has been found that film
blowing model predictions are in very good agreement
with the corresponding experimental data.
Introduction
The film blowing process is an important polymer
processing operation which is widely used for thin
polymer films production [1-29]. These biaxially oriented
films of a small thickness are used in commodity
applications, such as food wrapping and carrier bags in
food processing, medical films, scientific balloons,
garbage bags and waste land fill liners in the waste
industry. The relationships between the machine design,
processing parameters, material and the extensional
stresses within the extending bubble are still not fully
understood although they have been investigated by many
researchers from the late 1930´s [1-14]. The most popular
way to optimize the film blowing process is modeling. The
first film blowing model was developed by Pearson and
Petrie [20, 22] for isothermal process and Newtonian fluid
where the film is assumed to be a thin shell in tension in
the axial and circumferential directions. This model
became the basis of the most subsequent film blowing
models [15-17, 24, 26, 30-36]. However, numerical
instabilities [26, 29], inability to describe the full range of
the bubble shapes [27] and existence of anomalous predictions [37-38] were identified in the open literature if
one tried to solve the Pearson-Petrie equations with
particular constitutive equations. It has been recently
found that these problems can be overcome by the use of
the Zatloukal-Vlcek model [30-36] which describes the
formation of the bubble, due to the internal bubble
pressure and the take-up force, in such a way that the
resulting bubble satisfies the minimum energy
requirements.
The main aim in this work is to investigate predicting
capabilities of the Zatloukal-Vlcek model if nonisothermal
conditions and non-Newtonian fluid behavior
are taken into account. The studied model behavior will be
compared with Tas’s PhD thesis experimental data [18]
and predictions of the following two different Pearson and
Petrie based models: Sarafrazi and Sharif model [16]
(eXtended Pom-Pom constitutive equation is used; a
variable heat transfer coefficient and stress induced
crystallization is taken into account and Beaulne and
Mitsoulis model [15] (integral constitutive equation of the
K-BKZ type is utilized; constant heat transfer coefficient
and no crystallization effects are assumed).
Mathematical modeling
Zatloukal-Vlcek model
The Zatloukal-Vlcek model is based on the assumption
that bubble during blowing can be viewed as a elastic
membrane (characterized by the one constant value of
compliance J where the thickness is neglected) which is
bended due to the internal load, p, and take-up force, F in such a way, that bubble shape satisfies minimum energy
requirements [34]. Under these assumptions, the model
yields analytical expressions for bubble shape, take-up
force and internal bubble pressure which are summarized
in Table 1. The model is given by the following four
physical parameters: freezeline height, L, bubble curvature, pJ (which is given by the bubble compliance, J, and the internal load, p), the blow-up ratio, BUR, and the
die radius,
R
0. The function, which occurs in both equations for bubble shape and take-up force, depends on parameter A according to Table 2. Just note that in Eq. 1
in Table 1, y represents the bubble radius at particular distance from the die exit x (x=0 at the die exit; x=L at the freezeline height).
Non-isothermal film blowing with non-Newtonian fluid
where Q is the volume flow rate, y(x), the radius of the
bubble, h(x), the thickness of the film and v(x) is the film
velocity, all as functions of the distance from the die x.
Secondly,

where
means the extra stress tensor, D represents the deformation rate tensor and stands for the viscosity, which is not constant (as in the case of standard
Newtonian law), but it is allowed to vary with the first invariant of the absolute value of deformation rate tensor
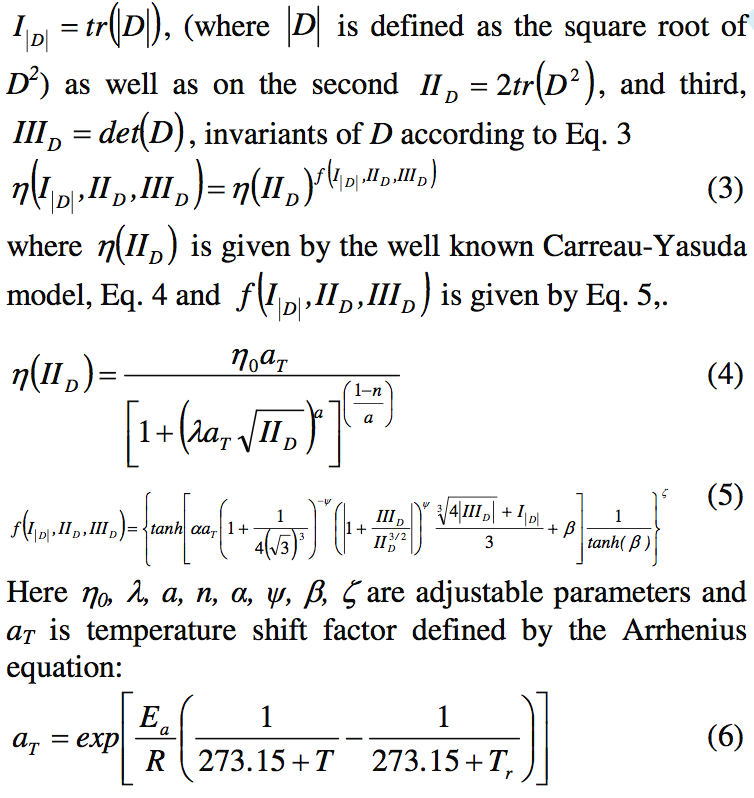
where E
a is the activation energy, R is the universal gas
constant, T
r is the reference temperature and T is local bubble temperature. It is not difficult to show that the
equation of continuity together with the generalized
Newtonian model yields the following expression for the
internal force at the freezeline in the machine direction:

Energy Equation:
With the aim to take non-isothermal conditions into
account, cross-sectionally averaged energy equation taken
from [40], has been considered:

where Cp stands for the specific heat capacity, ρ is the polymer density, y means the local bubble radius, m is
the mass flow rate, HTC represents the heat transfer coefficient, T is the bubble temperature, T
air means the air
temperature used for the bubble cooling, σ
B stands for the Stefan-Boltzmann constant, ε represents the emissivity, τ is the extra stress tensor,
(upsidedown delta)v means velocity gradient tensor, ΔH
f indicates the heat of crystallization per unit mass and Φ is the average absolute crystallinity degree of the system at the axial position, x.
In order to reduce the problem complexity, the axial
conduction, dissipation, radiation effects and
crystallization are neglected. For such simplifying
assumptions, the Eq. 9 is reduced in the following, the
simplest version of the cross-sectionally averaged energy
equation:

where the local bubble radius y is given by Eq. 1 in
Table 1. The Eq. 10 applied for the whole part of the
bubble takes the following form:

where T
die and T
solid represents the temperature of the melt
at the die exit and solidification temperature of the
polymer, respectively. After integration from die
temperature, T
die, up to freezeline temperature, T
solid, we
can obtain equation defining the relationship between
freezeline height, L, and heat transfer coefficient, HTC,
which take the following simple analytical expression:

With the aim to get equations for the temperature
profile along the bubble, it is necessary to apply the Eq. 10
for any arbitrary point at the bubble i.e. in the following
way:

After the integration of Eq. 13, the temperature profile
takes the following analytical expression:

Velocity profile calculation:
With the aim to calculate the velocity profile and the
film thickness in the non-isothermal film blowing process,
the force balance in vertical direction (gravity and upward
force due to the airflow are neglected) proposed by
Pearson and Petrie is considered in the following form:

where σ
11 is the total stress in the machine direction and F and Δp are defined by Eqs. 4 in Table 1,
F
total = |F| and Eq. 5 in Table 1. The deformation rate tensor in the
bubble forming region takes the following form:
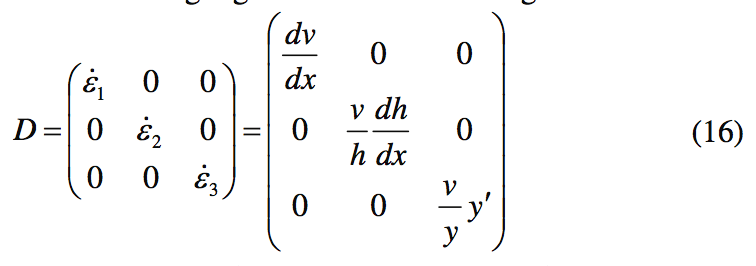
where v and h is bubble velocity and thickness,
respectively. Assuming that h << y, then

By combination of Eqs. 2, 16, 17, the σ
11 takes the
following form:

After substituting Eq. 18 into Eq. 15, the equation for
the bubble velocity in the following form can be obtained.

where v
d is bubble velocity at the die exit. Having the
velocity profile, the deformation rates and the thickness
can be properly calculated along the bubble.
Modeling versus experimental data
In this part, the above described film blowing model
will be tested by using experimental data taken from the
Tas’s PhD thesis [18]. Moreover, theoretical predictions
will be compared with two different film blowing models
[15-17] (those predictions will be taken from the
literature) which has already been utilized for the same
experimental data set.
Material definition
In this work, LDPE L8 taken from Tas’s PhD thesis
[18] is considered (Table 3). Material characteristics
together with corresponding viscoelastic Phan-Thien-Tanner (PTT) model parameters are provided in [18]. It
should be mentioned that predictions of the PTT model
[41] for steady state shear and steady uniaxial extensional
viscosities have been used as the measurements for LDPE
L8 in order to obtain all adjustable parameters of the
proposed model (Eq. 3-5), which is utilized here as the
constitutive equation. This procedure has been chosen due
to the fact that steady state rheological data for tested
LDPE L8 is not available in Tas’s PhD thesis.
In Figure 1, it is clearly visible that the used
generalized Newtonian model has very good capabilities
to describe steady shear and steady uniaxial extensional
viscosities for the Tas’s LDPE L8 sample which justifies
its utilization in the film blowing modeling. The
generalized Newtonian model parameters are provided in
Table 4 and the parameter
has been chosen to be 20 as
suggested in [39].
Film blowing experiment versus model prediction
In this section, proposed model predictions for the
bubble shape (Figure 2), film velocity (Figure 3) and
temperature profiles (Figure 4), for the processing
conditions summarized in Table 4, are compared with
Tas’s experimental data [18] together with theoretical
predictions by Sarafrazi and Sharif [16] model and
Beaulne and Mitsoulis model [15] which are based on the
classical approach of Pearson and Petrie [20].
It should be mentioned that two possible numerical
schemes have been tested for the proposed model. First
procedure consider that the bubble shape (i.e. pJ, BUR) is
a priory known and take-up force F and internal bubble
pressure Δp are unknowns parameters whereas in the
second case, Δp is known and bubble shape (i.e. pJ, BUR) and F are unknown parameters.
As can be clearly seen in Figures 2-4, both numerical
approaches leads to very similar predictions for all
investigated variables (bubble shape, velocity and
temperature) and it can be concluded that the agreement
between the proposed model predictions are in very good
agreement with the corresponding experimental data.
Moreover, tested model predictions are comparable with the Sarafrazi/Sharif [16] model predictions (which is
based on the advanced eXtended Pom-Pom constitutive
equation; a variable heat transfer coefficient and stress
induced crystallization).
Complete set of calculated variables in the proposed
model for theoretical predictions depicted in Figures 2-4
are summarized in Table 5. It is nicely visible that
predicted F and Δp for all tested polymers and processing
conditions are in fairly good agreement with the
corresponding Tas’s experimental data. These predictions
are comparable with Sarafrazi/Sharif [16] model
predictions and even better than Beaulne and Mitsoulis
model [15] behavior which is based on the viscoelastic
integral constitutive equation of the K-BKZ type assuming
constant heat transfer coefficient and no crystallization
effects. Just note that for the die volume rate calculation
(from the experimentally known mass flow rate), the
following definition of the LDPE density taken from [18]
was used:

Conclusion
It has been shown that minimum energy approach
(considering non-isothermal processing conditions and
recently proposed generalized Newtonian model) can be
taken as the useful modeling tool for the film blowing
process due to its qualitative as well as qualitative
prediction capabilities in terms of internal bubble
pressure, take-up force, bubble shape, velocity and
temperature profiles.
Acknowledgments
The authors wish to acknowledge GA CR and for the
financial support of Grant No. P108/10/1325.
References
1. S. Kim, Y.L. Fang, P. G. Lafleur and P. J. Carreau,
Polym. Eng. Sci. 44, 283-302 (2004).
2. R. S. Mayavaram, “Modeling and simulation of film
blowing process”, Ph.D. Thesis, A&M University
Texas, 2005.
3. K. Cantor, Blown Film Extrusion, Munich: Cark
Hanser Verlag, 2006, p. 165.
4. C. D. Han and J. Y. Park, J. Appl. Polym. Sci. 19, 3277 (1975).
5. C. D. Han and J. Y. Park, J. Appl. Polymer Sci. 19,
3291 (1975).
6. Y. L. Yeow, J. Fluid Mech 75, 577-591 (1976).
7. C. D. Han and R. Shetty, Ind. Eng. Chem. Fund. 16,
49 (1977).
8. T. Kanai and J. L. White, Polym. Eng. Sci. 24, 1185
(1984).
9. W. Minoshima and J. L. White, J. Non-Newtonian
Fluid Mech. 19, 275 (1986).
10. T. Kanai and J. L. White, J. Non-Newtonian Fluid
Mech. 19, 275 (1986).
11. T. J. Obijeski and K. R. Puritt, SPE ANTEC Tech.
Papers 1, 150 (1992).
12. P. A. Sweeney and G. A. Campbell, SPE ANTEC
Tech. Papers 461, 461 (1993).
13. T. Kanai and G. A. Campbell, Film Processing:
Progress in Polymer Processing, Munich: Hanser
Gardner Publications, 1999.
14. T. I. Butler, SPE ANTEC Tech. Papers 1, 1120 (2000).
15. M. Beaulne and E. Mitsoulis, J. Appl. Polym. Sci. 105,
2098-2112 (2007).
16. S. Sarafrazi and F. Sharif, International Polymer
Processing. 23, 30-37 (2008).
17.I. A. Muslet and M. R. Kamal, J. Rheol. 48, 525-550
(2004).
18. P. P. Tas, “Film blowing from polymer to product”, Ph.D. Thesis, Technische Universitat Eindhoven,
1994.
19 .R. K. Gupta, “A new non-isothermal rheological
constitutive equation and its application to industrial
film blowing”, Ph.D. Thesis, University of Delaware,
1981.
20. J. R. A. Pearson and C.J.S. Petrie, J. Fluid. Mech. 40,
1 (1970).
21. J. R. A. Pearson and C.J.S. Petrie, J. Fluid. Mech. 42,
609 (1970).
22.J. R. A. Pearson and C.J.S. Petrie, Plast. Polym. 38, 85
(1970).
23. C. J. S. Petrie, “Film blowing, blow moulding and
thermoforming,” in Applied Science, edited by J. R. A.
Pearson and S.M. Richardson, London, 1983, p. 217.
24.C. D. Han and J. Y. Park, J. Appl. Polym. Sci. 19,
3277 (1975).
25.C. J. S. Petrie, Am. Inst. Chem. Eng. J. 21, 275 (1975).
26. X. L. Luo and R. I. Tanner, Polym. Eng. Sci. 25, 620
(1985).
27.B. K. Ashok and G. A. Campbell, Int. Polym. Proc. 7, 240 (1992).
28. S. M. Alaie and T. C. Papanastasiou, Int. Polym. Proc. 8, 51 (1993).
29.J. M. Andr´e, Y. Demay, J. M. Haudin, B. Monasse
and J. F. Agassant, Int. J. Form. Proc. 1, 187 (1998).
30. M. Zatloukal, J. Non-Newtonian Fluid Mech. 113,
209 (2003).
31. M. Zatloukal and J. Vlcek, J. Non-Newtonian Fluid
Mech. 123, 201-213 (2004).
32. M. Zatloukal, J. Vlcek, P. Saha, Annual Technical
Conference - ANTEC, Conference Proceedings 1, 235-239 (2004).
33. M. Zatloukal and J. Vlcek, Annual Technical
Conference - ANTEC, Conference Proceedings 1, 139-142 (2005).
34. M. Zatloukal and J. Vlcek, J. Non-Newtonian Fluid
Mech. 133, 63-72 (2006).
35. M. Zatloukal, H. Mavridis, J. Vlcek and P. Saha,
Annual Technical Conference - ANTEC, Conference
Proceedings 2, 825-829 (2006).
36. M. Zatloukal, H. Mavridis, J. Vlcek and P. Saha,
Annual Technical Conference - ANTEC, Conference
Proceedings 3, 1579-1583 (2007).
37. C. C. Liu, D. C. Bogue, J. E. Spruiell, Int. Polym.
Process. 10, 226 (1995).
38. C. C. Liu, D. C. Bogue, J. E. Spruiell, Int. Polym.
Process. 10, 230 (1995).
39. M. Zatloukal, J. Non-Newtonian Fluid Mech. 165
(2010) 592-595.
40. A. K Doufas and A.J. McHugh, J. Rheol. 45, 1085
(2001).
41. N. Phan-Thien, R. I. Tanner, J. Non-Newtonian Fluid
Mech. 2 (1977) 353–365.
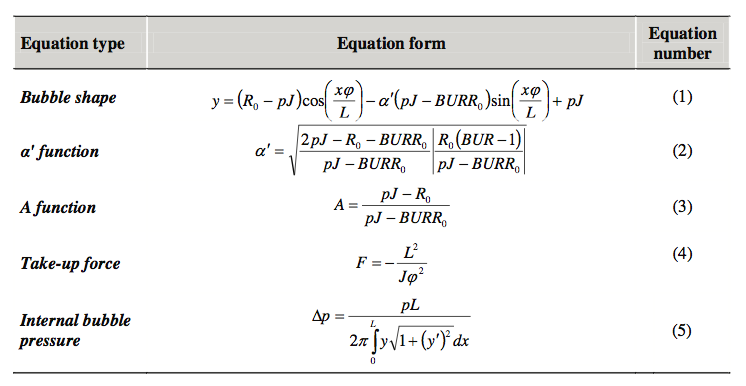
TABLE 1. A Summary of the Zatloukal-Vlcek mode

TABLE 2. Relationship between A and phi functions.

TABLE. 3. Characteristics of the L8 Stamylan LDPE used in the experiments by T as [18].

TABLE 4. Film blowing model parameters for Tas’s experiments No. 29.
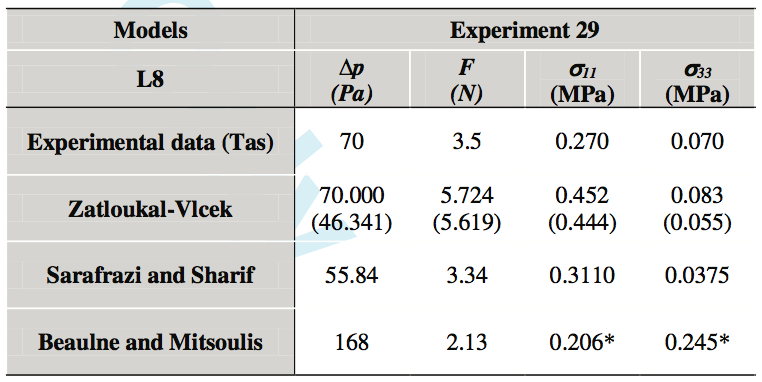
TABLE 5. Summarization of Tas’s experimental data [18], Zatloukal-Vlcek [39] (the calculated results for the fixed bubble shape pJ and internal bubble pressure (delta)p are provided in the brackets and without brackets, respectively), Sarafrazi/Sharif [16] and Beaulne/Mitsoulis [15] model predictions for Tas’s LDPEs and processing conditions.

- σ11, σ33 at the freezeline were calculated by using vd, R0, H0, F, Δp, BUR, vf provided in [15] and Pearson and

FIGURE 1. Comparison between the generalized Newtonian model fit (solid lines) [39] and PTT model predictions (symbols) characterizing L8 Stamylan LDPE material according to Tas's Ph.D. thesis [18].
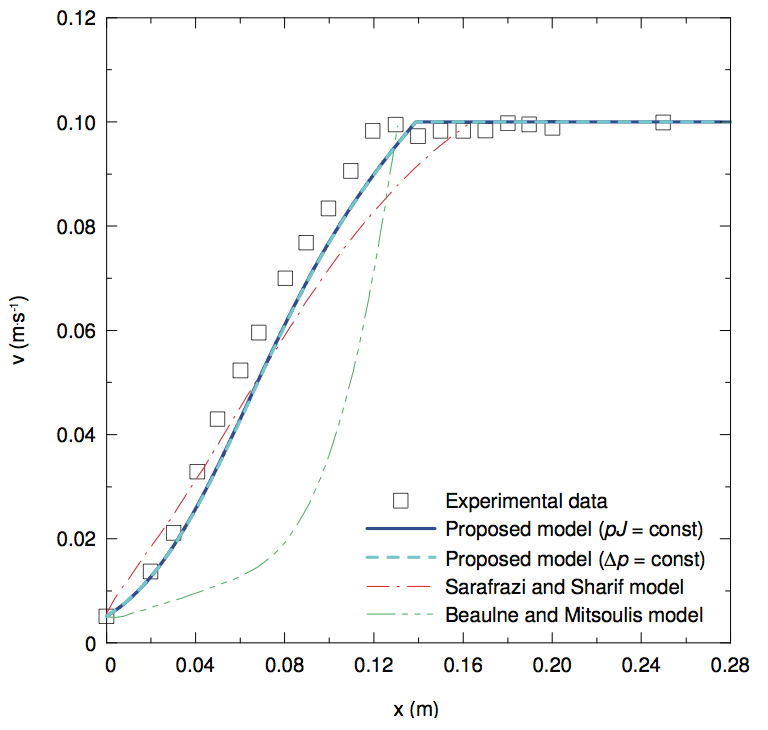
FIGURE 2. Comparison of the bubble shapes between the proposed model prediction [30], experiment No. 29 taken from Tas ́s Ph.D. thesis [18] and the Beaulne/Mitsoulis model prediction [15] and the Sarafrazi/Sharif model prediction [16].
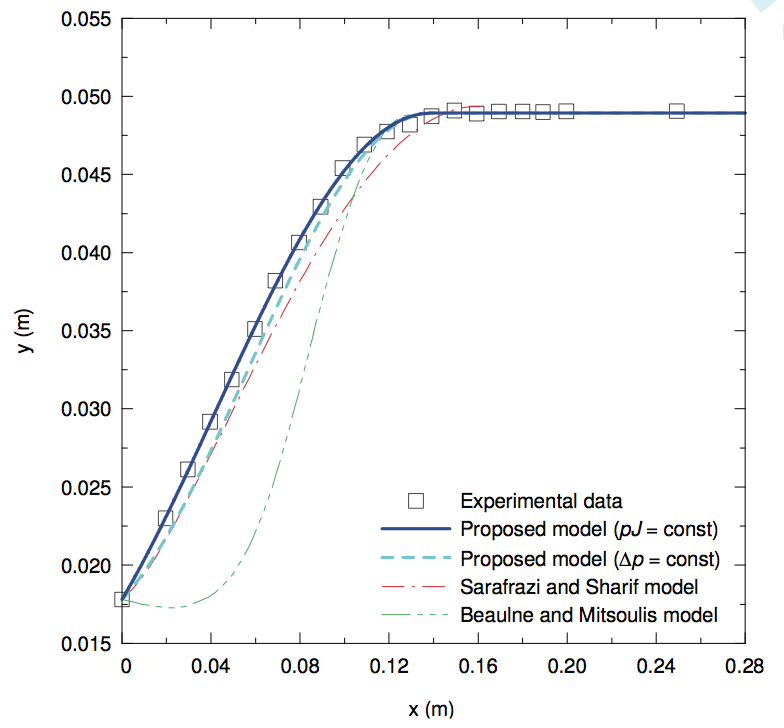
FIGURE 3. Comparison of the velocity profiles between the proposed model prediction [30], experiment No. 29 taken from Tas ́s Ph.D. thesis [18] and the Beaulne/Mitsoulis model prediction [15] and the Sarafrazi/Sharif model prediction [16].
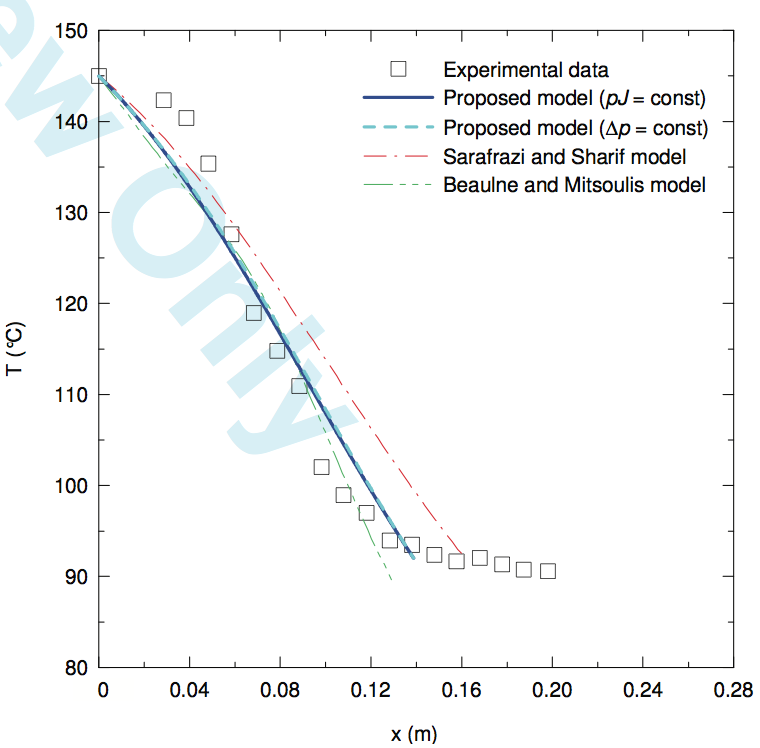
FIGURE 4. Comparison of the temperature profiles between the proposed model prediction [30], experiment No. 29 taken from Tas ́s Ph.D. thesis [18] and the Beaulne/Mitsoulis model prediction [15] and the Sarafrazi/Sharif model prediction [16].
Return to
Paper of the Month.