Comparison of the Melting Behavior of HDPE and PP in Single Screw Extruders¶
María del Pilar Noriega, Tim A. Osswald* and Alberto Naranjo
ICIPC – Plastics and Rubber Institute
Carrera 49 No. 5 Sur-190, Medellin, Colombia, South America
*Polymer Engineering Center (PEC), Department of Mechanical Engineering
University of Wisconsin-Madison, Madison, Wisconsin 53706Abstract
Actual experimental techniques designed to study
melting behavior of polymers inside the screw extruder
suffer from lack of functionality and high time consuming
procedures. Their invasive nature affect friction
characteristics and heat transfer, influencing the outcome
of measured parameters. This paper presents a patented
technique (U.S Patent No. 7314363) that can capture
experimental data and images from inside the extruder at
short response times using a highly instrumented 45 mm
extruder with built-in sensors and small quartz windows.
The melting behavior of polyethylene and polypropylene
were visualized and measured with this non-invasive
technique. A comparison of the melting behavior of both
polymers was obtained.
Background
Maddock and Street carried out their experiments
using a polymer with a high degree of crystallinity
(polyethylene). From observation of the solidified content
of the screw channel a qualitative description of the
melting mechanism could be given. The experimental
technique consisted of abruptly stopping an extruder
operating at steady state, chilling both barrel and screw,
pushing out the screw from the barrel, unwinding the
polymer from the screw and slicing thin representative
sections perpendicular to the flights. To better visualize
the process, a small amount (3 – 5 %) of colored polymer
was added as a tracer to distinguish between the solid and
the molten regions. The experiments also provided some
information on flow patterns, [1, 2]. The model, which
they proposed, describes the melting as a process of
which the major part of the heat transfer takes place
through a thin molten layer, which is formed, at the hot
extruder barrel. Under the condition that the thickness of
the film exceeds the width of the clearance between the
flight and the barrel surface, the melt film will be
removed by the advancing screw flight. A pool of molten
polymer is formed at the pushing side of the flight. The
scraped-off melt is mixed with previously molten material
due to the circulatory flow in this pool, caused by the component of the barrel velocity perpendicular to the
flight.
Tadmor developed a quantitative model based on the
experimental results of Maddock. As previously
mentioned, the solid bed is pushed against the trailing
flight flank. Between the solid bed and the barrel is a
relatively thin melt film. Material melting at the solid/melt
interface enters into this melt film and is dragged toward
the leading flight flank where the majority of the melt
collects in the melt pool, [3, 4]. Most melting occurs at
the interface between the solid bed and the melt film
between the solid bed and the barrel. Melting occurs as a
result of the heat conducted from the barrel and viscous
heat generation in the melt film. The latter is high because
of the high shear rate in the melt film. The high shear rate
is due to the high relative velocity between the barrel
surface and the solid bed, [5]. This model was evaluated
by conducting a series of experiments. Tadmor and coworkers
were able to visualize, flow pattern or circulation
in the melt pool and melt film by cooling down the
extruder barrel, followed by removal of the barrel from
the screw. The model was used to predict the solids bed
profile (SBP) in screw channels of typical extruders.
Pearson and coworkers presented a complete
analytical melting model assuming that the solid bed was
not able to stand large differences of principal stresses
and so account has to be taken explicitly of the
downstream force balance on the solid bed and in the melt
pool. He was the first one to divide the material in the
screw channel into five zones. The zones were marked A,
B, C, D and E. Zone A is the bed of solid polymer
granules surrounded on all four sides by molten polymer.
The solid material constitutes a freely flowing bed of
granules. The existence of zones D and E depends on the
temperature of the screw. Zone C is the thin melt layer
zone, or melt film, and B is the melt pool as used in the
previously described models. Melting takes place at all
four interfaces, AB, AC, AD and AE. The viscous heat
dissipation in the film was not considered in this model,
[6, 7, 8, 9].
Wong, Zhu and coworkers studied the dynamic
characteristics of the breakup of the solid bed during the
melting process in a single screw extruder. Their
observations confirmed that as a result of the increasing
pressure gradient in the screw channel, the stresses
exerted on the solid bed exceed the mechanical strength
of the bed itself. In their research they found the solid bed
strength as a function of bed temperatures, [10, 11]. They
carried out their experiments in an extruder with its barrel
equipped with glass windows or ‘glass extruder’.
Derezinski developed a melting rate function based
on the performance data of operating extruders to
establish average general terms of the energy equation /12/.
Other Authors have investigated extensions of the
above mentioned melting mechanisms or studied new
melting mechanisms like dispersed solids melting,
dissipative melting and mix-melting, [13, 14, 15]. These
mechanisms have been found more suitable for twin
screw extruders rather than single screw extruders.
Dispersed solids melting (DSM) is considerably more
efficient and the melting time is significantly shorter than
contiguous solids melting [16].
Experimental
Optical Technique for In-Line-Measurement of
Polymer Melting:The main focus of the present research is the process
visualization based on remote viewing into small diameter
inside the extruder barrel. The first step in designing the
process was to select and characterize a suitable optical
setup, which could detect the phase change based on the
differences in the density and optical properties of the
polymer. This selection was a major step in the success of
the visualization.
Three remote viewing possibilities were investigated
including some of the following components like lenses,
rod optics, fiber optics, illumination and color video
systems:
• A micro-camera or lipstick camera of ∅ 7 mm
with flexible fiber optic light guide and
illuminator,
• A flexible fiberscope of ∅ 8 mm with a videolight
source combination unit, and
A rigid boroscope of ∅ 8 mm with fiber optic light
guide and cold light source.
All the three possibilities required a special holder to
locate the instrument in the extruder barrel. The function
of the holder is to preserve the instrument at high
processing temperatures and high extruder pressures. It is also clear that the holder is a mini-heat exchanger because
it should keep the instrument at its operating temperature.
The holder tip is a circular quartz window in contact with
the polymer inside the extruder barrel for allowing
visualization. Its geometry is ∅ 10 mm ± 0.05 mm and
thickness of 6 mm ± 0.05 mm. Fig. 1 shows the final
holder concept and design after several heat transfer
calculations and trials. The main holder components are:
the shell, the core and the circular quartz window. The
shell was manufactured in stainless steel of 300 series and
has welded inlet and outlet for air cooling. For viewing
into very small, straight and restricted areas, rigid
boroscopes with rod lenses produce exceptionally clear
images and they are less expensive than fiberscopes. A
rigid boroscope of ∅ 8 mm was selected considering
optical coverage, holder geometry and holder locations
every 2D along the extruder barrel. The operating
temperature of a micro-camera system is in the range
between – 10 °C and 40 °C due to the camera plastic
sheathing. This low temperature resistance discarded this
possibility. Fig. 2 shows a photograph of the new extruder
setup showing the boroscope, illuminator, holders at
different L/D positions along the barrel and the air
cooling system.
Calibration:
The calibration of the whole optical setup was also a
very important topic to be addressed in the present
research. The purpose of calibration is to determine the
relationship between image quantities (pixels) and the
scene that is being imaged. Calibration ensures that
measurements obtained from images can be used to
accurately infer measurements of observed processes. In
our application, the scene to be imaged is at a fixed
distance from the camera (or rather, from the objective
lens) and is roughly parallel to the image plane. These
constraints make the calibration process simpler than
“generic” camera calibration, [17]. The involved optics in
the present In-Line technique requires a circular quartz
window, several rod lenses inside the boroscope and the
video camera lens. The distance object-lens was kept
constant for all the experiments as needed. The only
quantity of interest here involves the measurement of
length; hence, the determination of the relationship
between pixels and units of length (mm) at the several
extruder barrel positions to be imaged is required. A
simplified calibration procedure was developed. The
accuracy of the results was verified by comparing the
measured screw flight width with a caliper vs. the length
of the screw flight measured with the optical setup. The
obtained relationship between pixels and units of length
was 1 mm = 129.884 pixels. Finally the conversion factor
k is equal to 0.031 mm/pixel. This value is in the range of
other similar optical systems between 0.01 and 0.035
mm/pixel, [17]. The accuracy of the obtained results was verified by comparing the screw flight width, e = 4.5 mm,
vs. the length of the screw flight measured from the
image. The obtained length was 610.23 pixels equivalent
to 4.69 mm. There is an acceptable error of 4 %.
Fig. 3 shows the type of images to be analyzed and
measured in this polymer melting research in single screw
extruders. From left to right, the solid bed, melt pool,
screw flight, narrow melt layer and solid bed can be
clearly observed in the obtained image.
Results
Some images were captured from videos for
illustration of the present research. For example, at 10
rpm four videos were recorded at barrel positions, 6D,
8D, 10D and 12D. Further videos were not recorded
because the HDPE and PP materials were completely
molten at 12 D. Two videos per barrel position (L/D)
were recorded checking for reproducibility. Observations
from both videos were the same.
Two images for HDPE at 6D were captured from the
video on both sides of the screw flight and they are shown
in Fig. 4. The material flow direction was from the right
to the left. As expected the HDPE and PP materials were
completely solid and the polymer granules and screw
flight were noticeable. Considering the solids bed profile,
this measurement is equivalent to X/W = 1 after Tadmor
nomenclature. Fig. 8 shows two images for PP at 6D.
Two images for HDPE at 8D were extracted from the
video on both sides of the screw flight and they are
presented in Fig. 5. As expected the HDPE material was
partially molten and the polymer granules were
compacted to a solid bed. The left picture showed the melt
pool and the screw flight and the right picture showed the
screw flight, narrow gap of molten polymer and the
compacted solid bed. The solid bed appeared white and
opaque, while the molten material appeared transparent;
therefore the screw root was observable. The narrow gap
of molten polymer on the right picture of Fig. 5 was not
clear and reproducible observed in Tadmor ‘pushout’ or
cooling experiments, [18]. Pearson and coworkers
described this situation in their model. The screw flight
was always clear in all the images. Considering the SBP,
this measurement is equivalent to X/W < 1. On the
contrary, the PP material at 8D was still solid with
rubbery appearance and the polymer granules and screw
flight were noticeable. Fig. 9 shows an image for PP at
8D.
Two more images for HDPE were captured at 10D
from the video on one side of the screw flight, namely,
the melt pool side, and they are presented in Fig. 6. The
HDPE material was appreciably molten in this barrel position. Since the melt pool was transparent, the screw
root and even its curvature were observed. With regard to
solids bed profile, this measurement is equivalent to X/W
<< 1. Fig. 7 shows one image at 10D on the other side of
the screw flight, namely, the solid bed side. From the left
to the right, the screw flight, molten material and solid
bed were clearly identified. It is noticeable that the
amount of molten material on this side of the flight was
wider in this position than in previous position L/D=8.
The PP material at 10D showed more quantity of melt
than solid and the high elasticity of the melt and screw
flight were noticeable. Fig. 10 shows an image for PP at
10D.
At L/D=12 both polymer materials were completely
molten. The image looked like an empty screw due to the
high transparency of the melt. Considering the solids bed
profile, this measurement is equivalent to X/W = 0.
Solids bed profiles (SBP) could be obtained for the
experiments at 10, 20, 30 and 40 rpm. Table 1 shows the
experimental values of X/W versus L/D for HDPE to be
compared with melting models and additional
experimental observations.
A primary finding of these measurements is a full
description of the mechanisms that take place during
melting. In our observations, melting begins when the
granules near the barrel surface approach the melting
temperature, at which point the melt is smeared across the
whole surface. It is observed that as melting progresses
the formation of the melt pool is delayed for a few turns
due to the fact that before a melt pool forms, the melt fills
the gaps between the granules. This is in agreement with
Tadmor and Agassant [19], who actually never measured
this ‘delay zone’ but proposed its existence. In the present
research, this delayed zone has been clearly observed. The
filling of the porous regions between polymer granules is
equivalent to a solid bed melt saturation process. This
melt saturation or seepage probably occurs from all four
sides, but primarily from the barrel surface side, where
most of melt is generated. Once the solid bed is fully
saturated the melt pool starts to grow on the channel side
with lowest pressure, since the natural tendency of the
solid bed region is to be pushed against the leading flight,
or region of highest pressure.
The images taken at one position during one set of
processing conditions, can be assembled as a mosaic to
visualize the state of melt throughout the whole
circumference of the extruder. This is equivalent to
unwrapping an extruder slice, the width of a quartz
window. Fig. 11 represents the position L/D=8 inside the
solid bed melt saturation delay zone. The figure clearly
demonstrates that the solid bed is fully covered by a melt
film that extends over the screw flight. Fig. 12 shows from top to bottom the screw flight, the melt pool and the
solid bed during the solid bed reduction process, after the
saturation delay zone.
If we compare the experimental results with
Tadmor’s models and do not include the delay caused by
the solid bed melt saturation process, as is done today, the
analytical and the experimental results do not agree, as
shown in Fig. 13. However if Tadmor’s model is
modified, such that the melt pool grows after
experimentally determined delay zone, and not when the
melt film first forms, the experimental results and
modified model agree quite well, as shown in Fig. 14.
In these experiments, PP showed a higher viscoelastic
behavior in the molten state than HDPE. It could be also
observed that PP was very sticky against the quartz
windows, as shown in Fig. 15, specially above its melt
temperature. This occurrence has been also reported by
some authors in the literature. Fig. 15 shows an image for
PP at 12D, where the molten material is against the quartz
window.
Conclusions
The optical technique used to analyze polymer
melting proved successful for studying single screw
extruders. It was possible to distinguish between granules,
solid bed and molten material in the screw channel due to
the differences in optical properties between the melt and
the solid. HDPE and PP as semi crystalline materials were
white and opaque as a solid and totally transparent in the
molten state.
The presented and patented non-invasive technique
(U.S Patent No. 7314363) allowed visualization and InLine-measurements
of solid bed width and melt pool
width in z-direction and can also provide direct
observation of different polymer melting behavior inside
extruders, [20, 21]. Therefore, solid bed profiles could be
measured and be compared with Tadmor’s analytical
melting models. The extruder heat transfer was not
affected in this case due to the small diameter of the
boroscope holder opposite to the ‘push-out’ technique,
[18] and the glass extruder technique, [10, 11].
The important finding of this research is a full
description of the mechanisms that take place during
melting. Melting begins when the granules near the barrel
surface approach the melting temperature. At this point
the melt is smeared across the whole surface. It is
observed as melting progresses that the formation of the
melt pool is delayed for a few turns due to the fact that
before a melt pool forms, the melt fills the gaps between
the granules. This is in agreement with Tadmor and
Agassant [19], who actually never measured this ‘delay zone’ but proposed its existence. This delayed zone has
been clearly observed. The filling of the porous regions
was called solid bed melt saturation process. This melt
saturation or seepage probably occurs from all four sides,
but primarily from the barrel surface side, where most of
melt is generated. Once the solid bed is fully saturated the
melt pool starts to grow on this channel side with lowest
pressure, as the natural tendency of the solid bed region is
to be pushed against the leading flight, or region of
highest pressure.
The formation of a thin melt layer on the passive
flight allows inferring that the solid bed is surrounded by
molten polymer but the actual optical technique does not
allow this visualization and measurement.
Tadmor’s melting model was modified, such that the
melt pool grows after the experimentally determined
delay zone, and not when the melt film first forms, the
experimental results and modified model agree quite well.
All the obtained video images allowed a better
understanding of polymer melting in extruders and the
mechanisms involved like granules conveying, solid bed
compaction, melt formation, solid bed melt saturation,
decrease of solid bed, solid bed break-up and finally,
elasticity and/or stickiness of the melt. The videos have a
high educational value in polymer extrusion or polymer
processing and are useful for troubleshooting.
References
/1/ B. H. Maddock, A Visual Analysis of Flow and
Mixing in Extruder Screws, SPE- Journal 15 (1959),
pp. 383 – 389
/2/ L.F. Street, Plastifying Extrusion, International
Plastics Engineering, Vol. 1, (1961), pp. 289-296
/3/ Tadmor, Z., “Fundamentals of Plasticating Extrusion:
A Theoretical Model for Melting”, Polymer
Engineering and Science, Vol. 6, pp. 185 - 190, 1966
/4/ Tadmor, Z., Duvdevani, I.J. and Klein, I., “Melting in
Plasticating Extruders- Theory and Experiments”,
Polymer Engineering and Science, Vol. 7, pp. 198 –
217, 1967
/5/ Tadmor, Z. and Klein, I., “Engineering Principles of
Plasticating Screw Extrusion”, Van Nostrand
Reinhold, New York, 1970
/6/ Shapiro, J. and Pearson, J.R.A., “A dynamic model
for melting in plasticating extruders”, Imperial
College, Polymer Engineering Science Group, Report
No 5, April, 1974
/7/ Shapiro, J., Halmos, A.H., and Pearson, R.A.
“Melting in single screw extruders”, Polymer, Vol.
17, pp. 905-918, 1976.
/8/ Shapiro, J., Halmos, A.L. and Pearson, J.R.A.,
“Melting in single screw extruders”, Polymer, Vol.
17, pp. 905-918, 1976
/9/ Halmos, A.L., Pearson, J.R.A. and Trottnow, R.
“Melting in single screw extruders”, Polymer, Vol.
19, pp. 1199-1216, 1978
/10/ Wong, A.C.Y., Zhu, F., Liu, R. and Liu, T., “Breakup
of solid bed in melting zone of single screw
extruder. Part 1- Mathematical model”, Plastics,
Rubber and Composites Processing and Applications,
Vol. 26, pp. 336-342, 1997
/11/ Wong, A.C.Y., Zhu, F., Liu, R. and Liu, T., “Breakup
of solid bed in melting zone of single screw
extruder. Part 2 - Strength of solid bed and
experimental results”, Plastics, Rubber and
Composites Processing and Applications, Vol. 26,
pp. 343-350, 1997
/12/ Derezinski, S., “A melting rate model based on
extrusion data”, SPE ANTEC’99, Vol. 1, pp.184 –
187, 1999
/13/ Bruker, I. and Balch, G.S., “Melting mechanism in
single screw extrusion”, Polymer Engineering and
Science, Vol. 29, pp. 258-267, 1989.
/14/ Amellal, K. and Lafleur, P.G., “Computer simulation
of conventional and barrier screw extruders”,
Plastics, Rubber and Composites Processing and
Applications, Vol. 19, pp. 227-239, 1993
/15/ Huang, H. and Peng, Y., “Theoretical modeling of
dispersive melting mechanism of polymers in an
extruder”, Advances in polymer technology, Vol. 12,
pp. 343-352, 1993
/16/ Rauwendaal, C., “Comparison of two melting
models”, Advances in Polymer Technology, Vol. 15,
No. 2, pp. 135-144, 1996
/17/ Ferrier, N., “Video Imaging of Extruder Melting”, email
communication, ME- University of WisconsinMadison
2001.
/18/ Tadmor, Z. and Gogos, C., “Principles of Polymer
Processing”, John Wiley and Sons, Inc., 1979
/19/ Agassant, J.F. et. al., “Polymer Processing: Principles
and Modeling”, Hanser Publishers, Munich,
Germany, pp. 173, 1991
/20/ Noriega, María del Pilar, et. al., “Method and device
to visualize in-line and quantify the polymer melting
in plasticating screw machines without significantly
affecting its thermal regime”, U.S Patent No.
7314363, January 1, 2008.
/21/ Noriega, María del Pilar, et. al., “Dispositivo para
visualizar en línea y método para cuantificar la fusión
de polímeros en máquinas de plastificación con
tornillo sin afectar significativamente su régimen
térmico”, Colombian patent No.15348, March 31,
2009.
Acknowledgments
Thanks are also due to the Instituto de Capacitación e
Investigación del Plástico y del Caucho (ICIPC) in
Medellín, Colombia and COLCIENCIAS for their
financial support to develop this research project.
Nomenclature
D Extruder diameter
L/D Extruder length
W Channel width
X Solid bed width
SBP Solids bed profile
Key Words: Single screw extruder, polymer melting,
delay zone, HDPE, PP
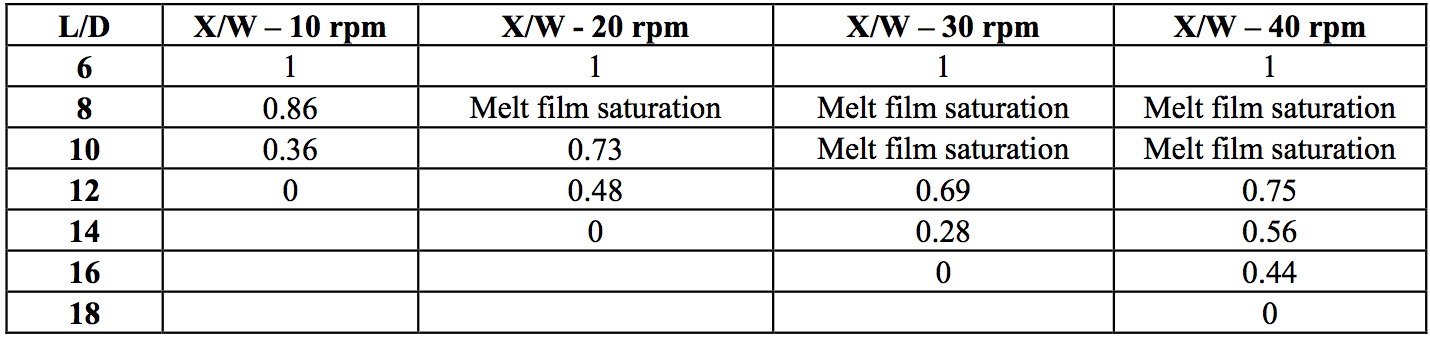
Table 1: Experimental values of X/W vs. L/D for HDPE
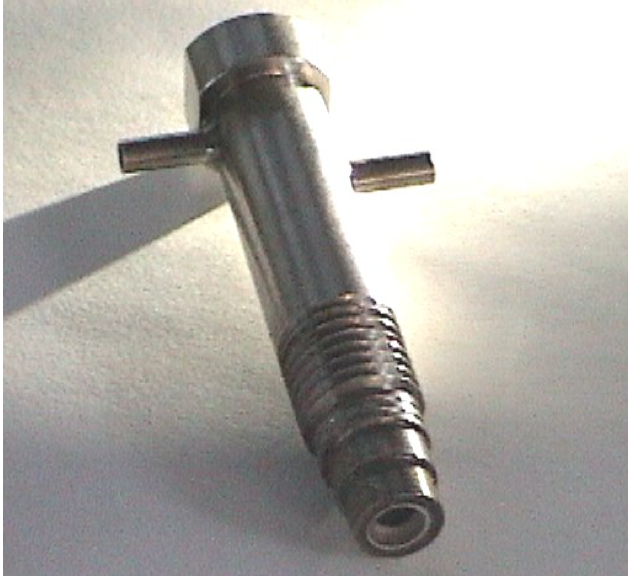
Figure 1: Holder shell with quartz window
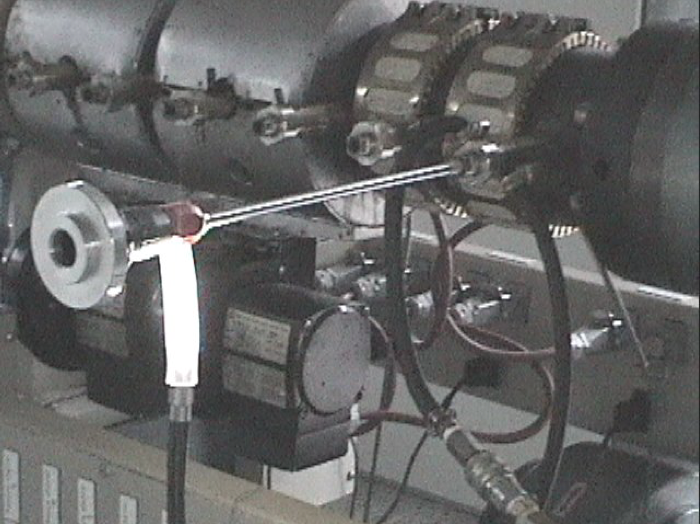
Figure 2: Extruder setup with holders and rigid boroscope

Figure 3: Image of the solid bed, melt pool and screw flight from inside the extruder
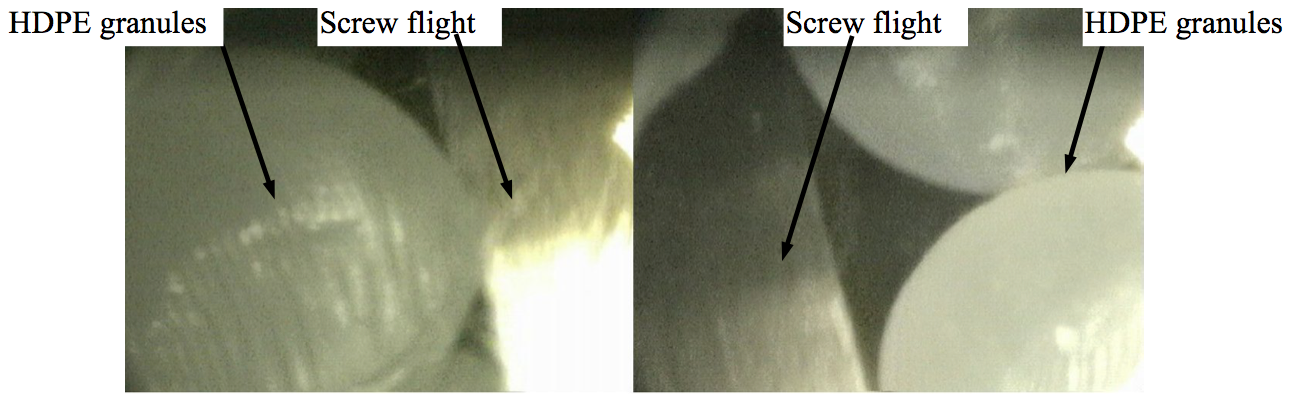
Figure 4: Images for HDPE at 10 rpm and L/D=6
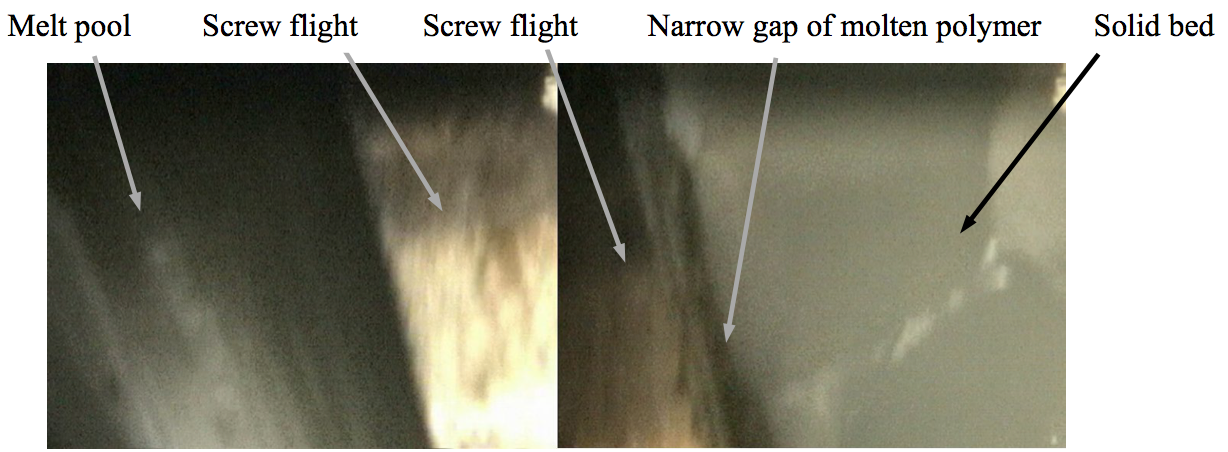
Figure 5: Images for HDPE at 10 rpm and L/D=8
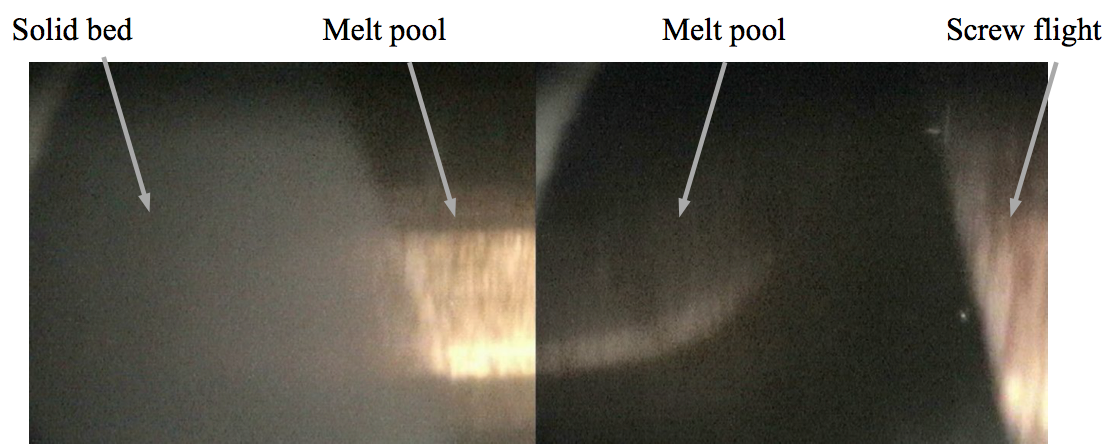
Figure 6: Images for HDPE at 10 rpm and L/D=10 on melt pool side
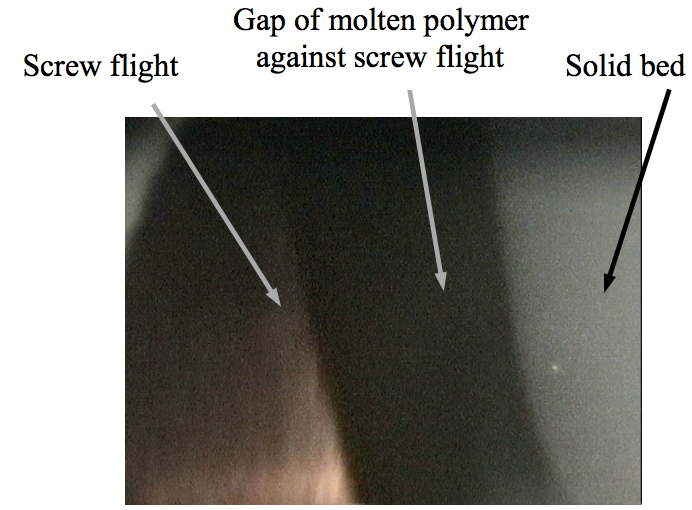
Figure 7: Image for HDPE at 10 rpm and L/D=10 on the other screw flight side
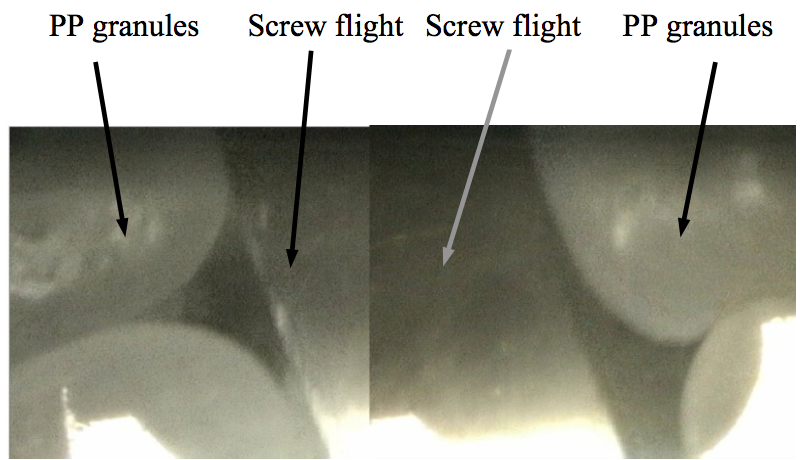
Figure 8: Images for PP at 10 rpm and L/D=6
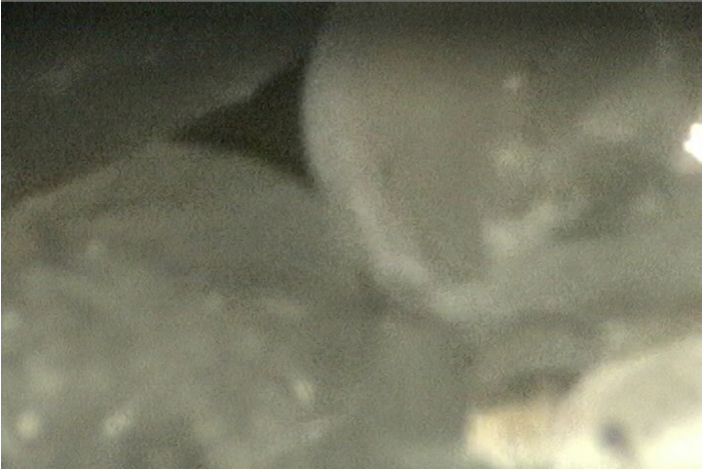
Figure 9: Image for PP at 10 rpm and L/D=8
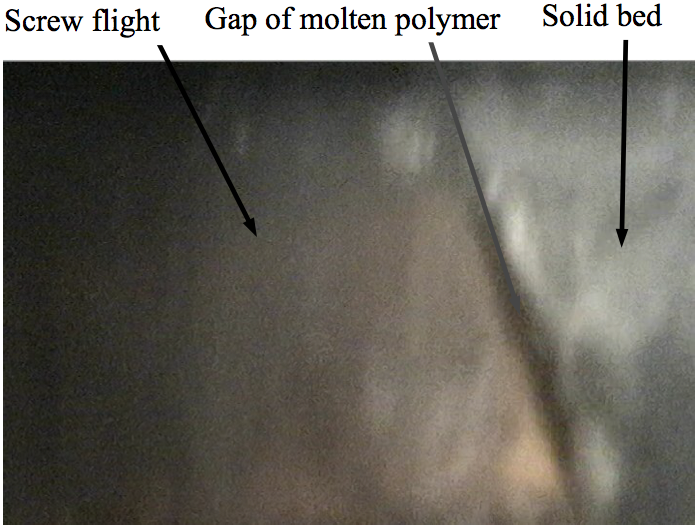
Figure 10: Image for PP at 10 rpm and L/D=10
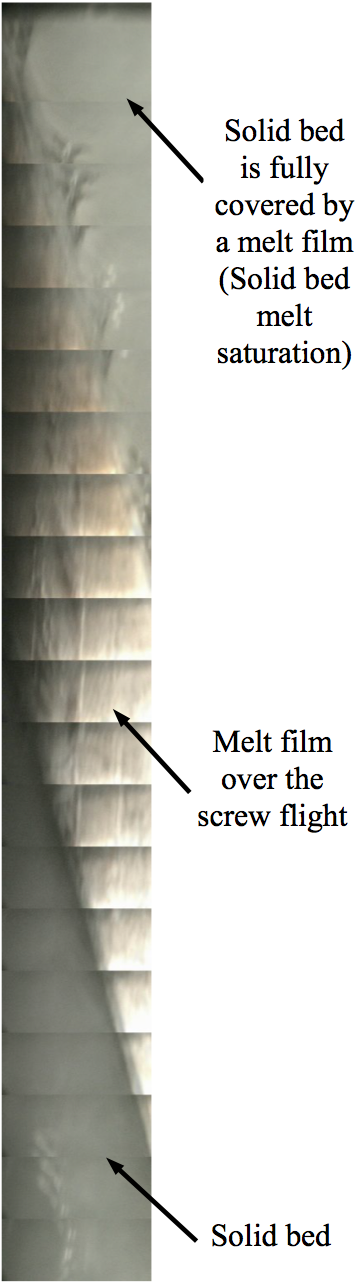
Figure 11: Mosaic of individual photos for HDPE at 20 rpm and L/D=8, ‘Delay Zone’
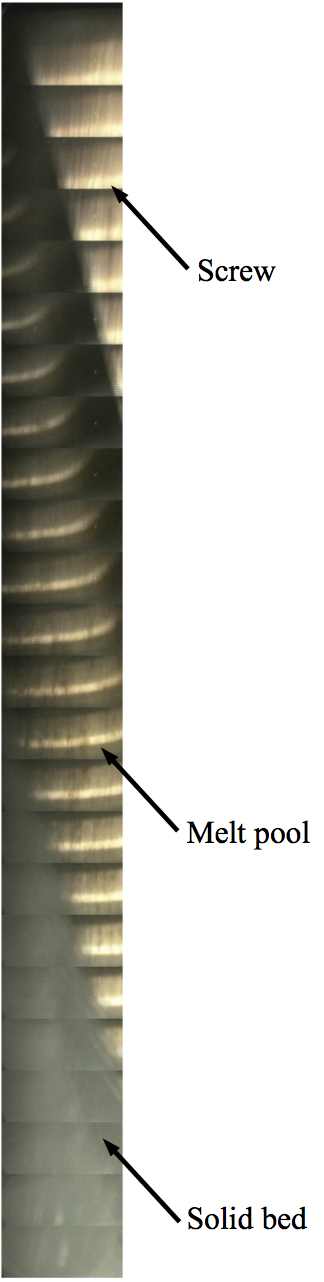
Figure 12: Mosaic of individual photos for HDPE at 20 rpm and L/D=10
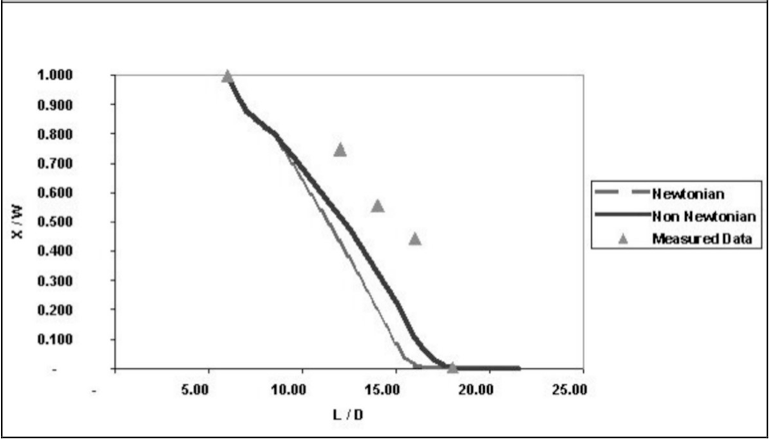
Figure 13: Experimental and classical modeled SBP for HDPE at 40 rpm
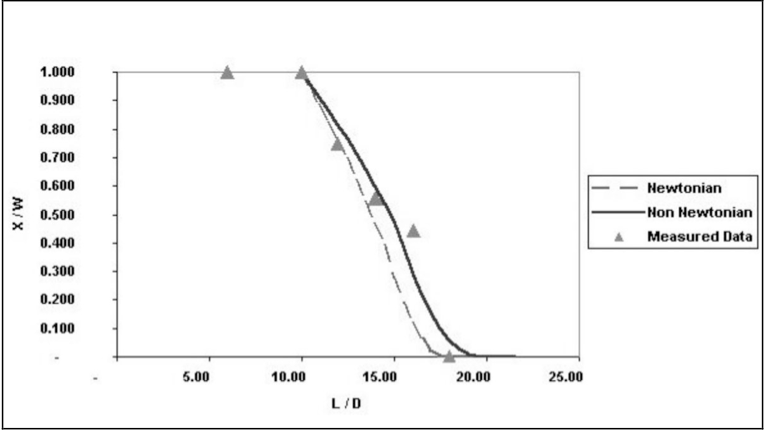
Figure 14: Experimental and modified modeled SBP for HDPE at 40 rpm
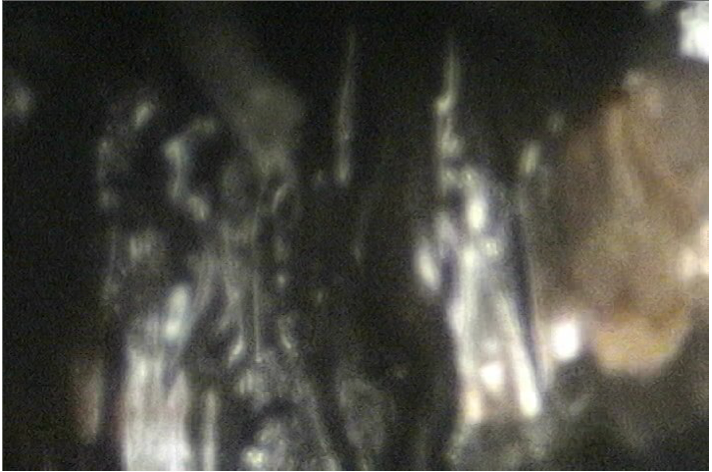
Figure 15: Image for PP at 10 rpm and L/D = 12
Return to
Paper of the Month.