1995 Coextrusion Layer Thickness Variation - Effect of Polymer Viscoelasticity on Layer Uniformity
Joseph Dooley and Kevin Hughes - The Dow Chemical Company, Midland, MI
AbstractThe effect of polymer viscoelasticity on the layer thickness uniformity of multilayer coextruded structures was investigated using a unique feedblock technology. This type of feedblock produces a coextruded structure consisting of an array of 49 individual strands (7 rows by 7 columns) of one polymer surrounded by a matrix of another polymer. These strands are excellent tracers of flow paths which can be used to determine movement within a flowing viscoelastic polymer stream.
IntroductionCoextrusion is a process in which two or more polymers are extruded and joined together in a feedblock or die to form a single structure with multiple layers. This technique allows the processor to combine the desirable properties of multiple polymers into one structure with enhanced performance properties. The coextrusion process has been widely used to produce multilayer sheet, blown film, cast film, tubing, wire coatings, and profiles (1-6).
Previous work on the layer thickness uniformity of coextruded structures has focused on the effects of differing polymer viscosities in the individual layers (7-11). These differences result in a phenomenon known as "viscous encapsulation" in which the less viscous layer tends to encapsulate the more viscous layer producing non-uniform layer thicknesses.
In this study, the effect of the viscoelasticity of the polymers studied on the layer thickness uniformity of multilayer coextruded structures was investigated using a unique feedblock technology. This work extends the previous research done by the authors on the geometric effects in the flow of coextruded polymeric structures (12,13). In order to minimize the viscosity effects, the coextrusion experiments were conducted using a single material pigmented differently in each extruder to allow observation of interface movements.
ExperimentalThe resins chosen for this study were a high impact polystyrene resin (STYRON* 484), a low density polyethylene resin (LDPE 641I), and a polycarbonate resin (CALIBRE* 300-22) all manufactured by The Dow Chemical Company. The rheological properties of these resins were discussed previously (12,13). Coextruded structures were made using the same material in each extruder with different colored pigments added to each to allow determination of the interface location in the coextruded structure.
The primary coextrusion line used in this study consisted of a 31.75 mm (1.25 inch) diameter, 24:1 L/D single screw extruder and a 19.05 mm (0.75 inch) diameter, 24:1 L/D single screw extruder. These extruders were attached to feedblocks that were designed to produce different coextruded structures. Attached to the exit of the feedblock was a die containing one of the different channel geometries studied.
Five different channel geometries were used in this study; a square channel, a circular channel, a teardrop shaped channel, a rectangular channel, and a rectangular manifold channel. These geometries have been described in more detail previously (12,13). The square, circular, teardrop, and rectangular geometries were chosen since they are used in the design of feedblocks and dies while the rectangular manifold channel is meant to simulate half of a coat-hanger type die. The length of each of the die channels was 60.96 cm (24 inches).
Two types of feedblocks were used in this study. The first feedblock produced a two layer structure with a 20% cap layer and an 80% substrate layer. The second feedblock was designed to produce a unique coextruded structure consisting of an array of 49 individual strands (7 rows by 7 ·columns) of one polymer surrounded by a matrix of another polymer. This second feedblock allows tracing of flow paths within a particular geometry by following the distortions of the individual strands from the entry to the exit of the channel which can be used to predict layer interface location(s) in coextruded layered structures. This feedblock not only allows tracing for interface locations for coextrusion flows, but also can be used to show the flow patterns in monolithic viscoelastic polymer flows. This paper will focus primarily on the 49 strand coextruded structure results.
For a typical experiment, the coextrusion line was run for a minimum of thirty minutes to ensure that steady-state conditions had been reached. The normal extrusion rate was approximately 4.5 kg/hr (10.0 lb/hr) for the polystyrene resin in the various channels which would give a wall shear rate in the range of 15 to 20 reciprocal seconds. Both the polystyrene and polyethylene resins were extruded at 204°C while the polycarbonate resin was extruded at 260°C. When steady state was reached, the extruders were stopped simultaneously and the coextruded material was cooled while still in the die channel. After it had cooled to room temperature, the polymer "heel" was removed from the die and examined. This procedure allowed the major deformations of the interfaces to be analyzed.
ResultsAn initial coextrusion experiment was run through the two layer feedblock only to ensure that the layers were uniform in thickness at the exit of the feedblock before they entered the die. Results from experiments using the two layer feedblock have been discussed previously (12,13) but will be briefly reiterated here for comparison purposes. Figure 1 shows the layer profile for the polystyrene resin extruded from both extruders. The substrate layer of polystyrene was pigmented black and the cap layer pigmented white so that the interface could be clearly distinguished between the two layers. Note that the layers are very uniform in thickness producing a flat interface.
The. next experiment consisted of running the same polystyrene resin through the two layer feedblock system with an attached die containing a square class-sectional shape. (0.95 cm x 0.95 cm). Cross-sectional cuts of this sample at 7.6cm (3 inch) intervals downstream from the feedblock are shown m Figure 2. This figure shows how the layers continue to rearrange as the material flows down the channel. The shapes of the interfaces shown in these figures cannot be explained by viscous encapsulation principles. A series of experiments revealed no significant influence of the presence of low levels of pigments on the layer rearrangement. It should also be reiterated at this point that the same polymer was being extruded in each layer of this structure in order to minimize any effects due to differences in viscosity.
The initial coextrusion experiment conducted with the 49 strand feedblock consisted of operating it with no die attached to ensure that the strands were uniform in diameter and location at the exit of the feedblock before they entered the die. Figure 3 shows the strand profile for the polystyrene resin at the end of the feedblock. The 49 strands of polystyrene were pigmented black and the matrix polystyrene pigmented white so that the interfaces could be clearly distinguished between the two. Note that the positions of the strands at the exit of the feedblock clearly show the 7 row by 7 column pattern and the strands are fairly uniform.
The next experiment consisted of running the same polystyrene resin through the 49 strand feedblock system with an attached die with a square cross-sectional shape. Cross-sectional cuts of this sample taken at the entry to the channel (shown on the left in the figure) and at 50 cm downstream from the feedblock (on the right in the figure) are shown in Figure 4. This figure clearly shows that the strand movement is symmetrical within each quadrant as material moves along the channel walls into the corners and then toward the center of the channel along the 45° diagonal line.
The strands shown in Figure 4 rearrange progressively as the polymer flows down the channel producing a more distorted strand profile as the distance travelled increases. This phenomenon is shown in Figure 5. In this figure, the interfaces are shown at 7.6 cm (3 inch) intervals from the entry of the channel (viewed from the top left hand corner to the bottom right corner of the figure, respectively).
Results similar to the polystyrene sample were obtained for the polyethylene resin extruded through the. square channel. This is shown in Figure 6 by samples taken at the entry and exit of the die. However, very little layer rearrangement was observed in the sample produced using the polycarbonate resin as is clearly shown in Figure 7.
When the resins were run through the circular die channel, essentially no strand movement was observed for any of the resins. This is shown in Figure 8 for the polystyrene resin.
When the resins were run through the die channel with the teardrop cross-section, substantial strand movement was again observed for the polystyrene and polyethylene resins but not for the polycarbonate resin. Sections cut from the polystyrene and polycarbonate samples taken from the teardrop channel are shown in Figures 9 and 10.
Processing the resins through the die channel with the rectangular cross-section again showed substantial strand movement for the polystyrene and polyethylene resins but not for the polycarbonate resin. Sections cut from the entry and exit of the rectangular polystyrene sample are shown in Figure 11.
The amount of strand movement appears to be quite different when compared to the results of the square channel. However, as was observed with the square channel, the strands continue to rearrange as the polymer flows down the channel. This is shown in Figure 12 for the polystyrene sample. This sample is shown with cuts made at intervals of 7.6 cm (3 inches) down the channel with the cut on the left being nearest the feedblock while the cut on the right was taken near the ex.it of the die.
When the three resins were extruded through the rectangular manifold channel, a significant amount of strand movement occurred once again in the polystyrene and polyethylene samples but not in the polycarbonate sample. Figures 13, 14, and 15 show a series of cross-sectional cuts made at 7.6 cm (3 inch) intervals down the rectangular manifold channel for the polystyrene, polyethylene, and polycarbonate samples, respectively. Again the cut on the left was made nearest to the feedblock while the cut on the right was near the end of the manifold.
DiscussionAs was discussed previously, (12,13) one hypothesis that has been advanced to explain the movement of the layers or strands in the polystyrene and polyethylene resins is the possible existence of secondary flows of the polymers in the channels. Secondary flows (flows perpendicular to the main flow) have been predicted for viscoelastic fluids in non-circular channels (14) but were thought to be small in magnitude compared to the bulk flow of the fluid (15). The predicted flow patterns for a viscoelastic fluid flowing through a square channel have been shown previously to contain eight recirculation zones or vortices, two each per quadrant (12, 16-19).
These secondary flow patterns are consistent with the layer rearrangement and strand movement seen in both the polystyrene and polyethylene resins in all of the non-circular channels studied. The polycarbonate resin, however, does not show this movement. This may be because it exhibits less elastic behavior than the other resins, as is indicated by it's lower storage modulus values (12,13).
The absence of any strand movement in the circular channel (even for the highly elastic polystyrene - see Figure 8) is consistent with the secondary flow hypothesis. These secondary flows are driven by imbalances in normal forces which do not occur in radially symmetric geometries (12).
The movement of the strands in the teardrop channel is similar to that seen in the square and rectangular channels except there are only six vortices compared to the eight seen in the square and rectangular channels.
The strand movement observed in the rectangular channel for the polystyrene and polyethylene resins is similar to that seen in the square channel but is elongated along the major axis of the rectangle. This channel geometry appears to cause the vortex associated with the major axis to increase while decreasing the minor axis vortex, correspondingly. Once again, however, the polycarbonate resin did not show much movement of the strands.
The progression of the layer movement for the polystyrene sample in the rectangle is shown in Figure 12. This figure shows that the progression of the layer movements is very similar to that seen in the square channel (Figure 5). The main difference between the square and rectangular samples appears to be the location and magnitude of the vortices found in each quadrant.
The flow patterns for the polystyrene, polyethylene, and polycarbonate samples in the rectangular manifold channel are shown in Figures 13 through 15. It appears that the strand profiles seen in the polyethylene and polystyrene resins in the rectangular manifold channel are produced by a combination of the vortices formed in the corners of fl rectangular channel and the leakage of the material out the bottom of the channel. Once again, however, the polycarbonate resin did not show as much movement of the strands.
The movement of the polystyrene and polycarbonate strands towards the top corners of the manifold are very similar to the movements seen in the rectangular channel shown in Figure 12. This combination of flow patterns will produce a fairly uniform layer or strand pattern near the entry of the manifold but the layers or strands near the end of the channel will be very distorted. This may be one mechanism to explain why coextruded structures of polymers with matching viscosities can sometimes produce products with non-uniform layer thicknesses. This could also explain why measurements of individual layer thicknesses in sheet products tend to show poorer distribution near the edges of the sheet compared to the center.
ConclusionsIt has been shown experimentally that coextruding identical viscoelastic polymers through channels of various geometries can cause the layers or strands to rearrange. This layer movement may be caused by secondary flows that occur in different channel geometries due to the elastic characteristics of the polymer.
These results have many implications for the coextrusion of viscoelastic polymers. Since the layer and strand movements observed occurred without any differences in viscosity between the layers, this implies that layer rearrangement may occur in coextrusions in which the polymer viscosities are well matched. Also, since the strands continue to rearrange as the polymer flows down the channel, these results also imply that this geometric effect will become more pronounced in sheet dies as they are scaled up to larger widths.
The layer rearrangements observed in the three resins studied appear to follow the trend of increasing layer rearrangement with increasing elastic characteristics. In this study, the polystyrene resin showed the most layer rearrangement, followed by the polyethylene resin and finally the polycarbonate resin which showed little movement.
AcknowledgementsThe Authors would like to thank Kun Hyun, Walt Schrenk, and Ravi Ramanathan for many useful suggestions and interesting discussions relating to this work.
References1. L.M. Thomka and W.J. Schrenk, Modern Plastics, (April 1972)
2. C.D. Han, J. Appl. Pol. Sci., 19, (1975)
3. W.J. Schrenk, Plastics Engineering, (March 1974)
4. J.A. Caton, British Plastics, 3, (1971)
5. L.M. Thomka, Package Engineering, 18, (Feb. 1973)
6. C.R. Finch, Plastics Design Forum, 59, (Nov./Dec. 1979)
7. J.H. Southern and R.L. Ballman, App Polym. Sci., 20, (1973)
8. A.E. Everage, Trans. Soc. Rhea., 17, (1973)
9. B.L. Lee and J.L. White, Trans. Soc. Rhea., 18, (1974)
10. J.H. Southern and R.L. Ballman, J. Polym. Sci., 13, (1975)
11. A.A. Khan and C.D. Han, Trans. Soc. Rheo., 20, (1976)
12. J. Dooley and B. Hilton, PIastics Engineering, p.25, (Feb 1994).
13. J. Dooley and R. Ramanathan, Society of Plastics Engineers Technical Papers, Volume XXXX, p. 89, (1994).
14. A.E. Green and R.S. Rivlin, Quart. Appl. Math., 14, (1956)
15. C. D. Han, "Rheology in Polymer Processing," p. 130, Academic Press, New York, (1976)
16. P. Townsend, K. Walters, and W. M. Waterhouse, J. Non-Newtonian Fluid Mech., 1, (1976)
17. A.G. Dodson, P. Townsend, and K Walters, Comput. Fluids, 2, (1974)
18. S. Thangam and C.G. Speziale, Acta Mechanica, 68, (1987)
19. J.A. Wheeler and E.H. Whissler, Trans. Soc. Rheol., 10, (1966)
* Trademark of The Dow Chemical Company
Return to
Best Papers.
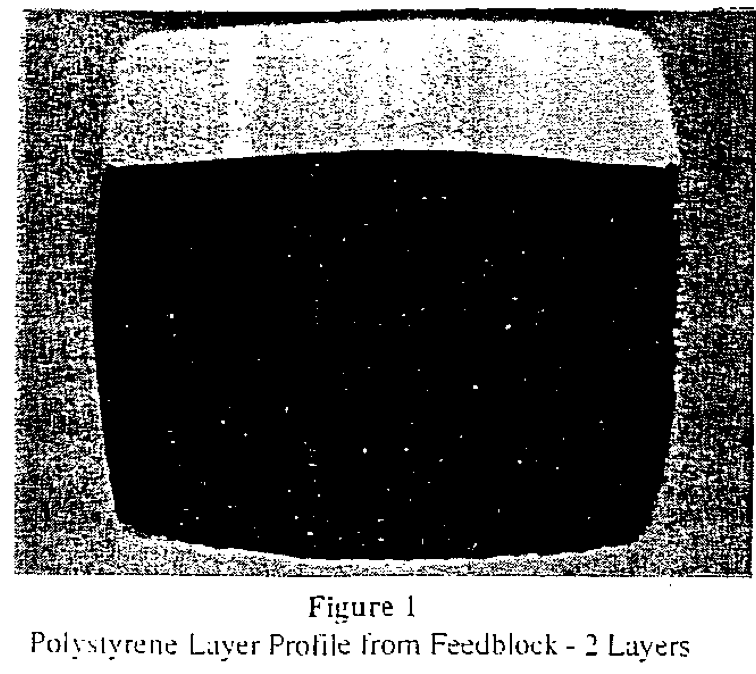
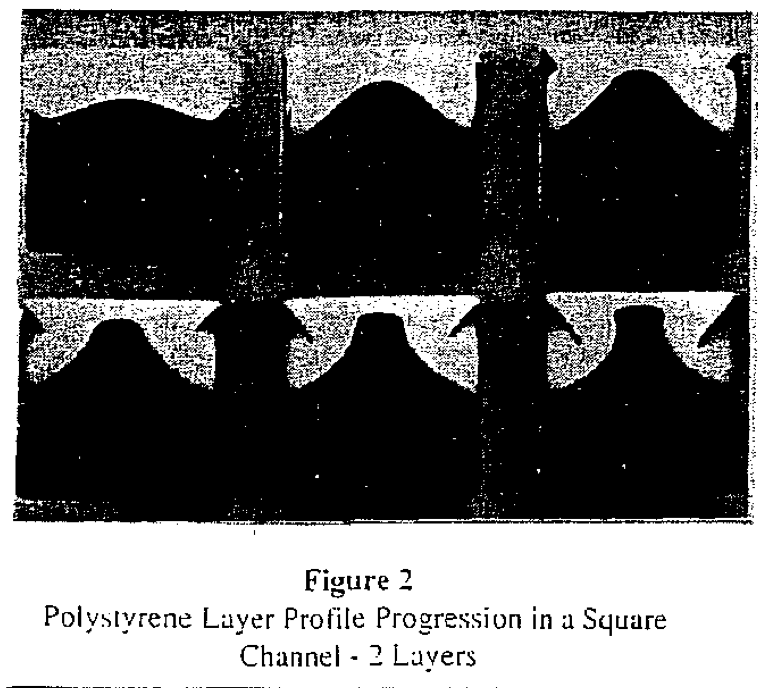
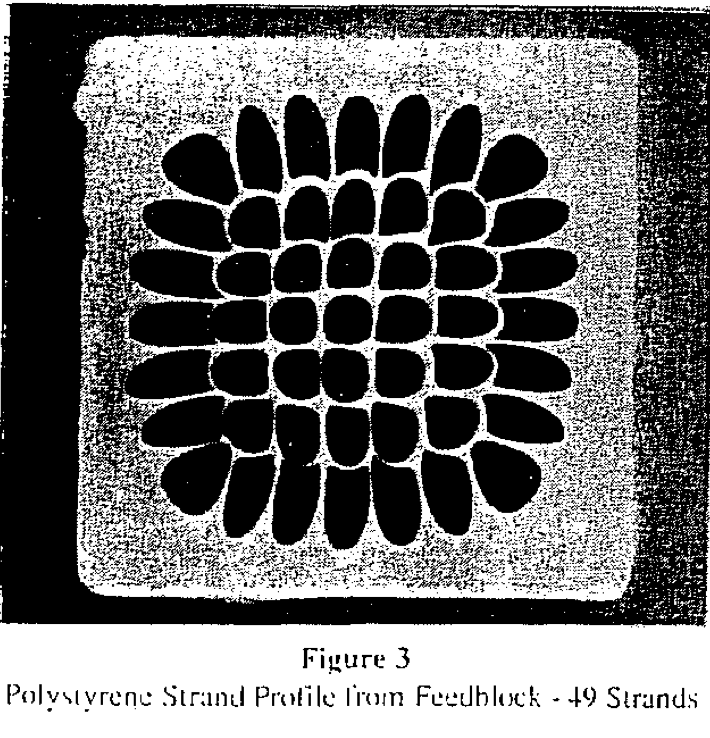
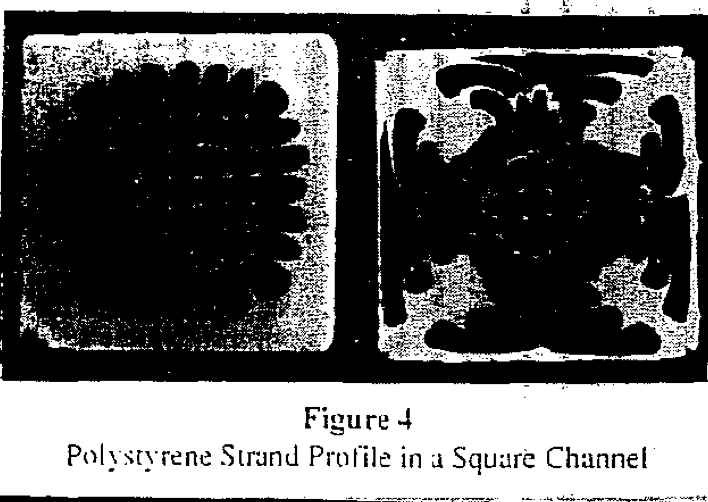
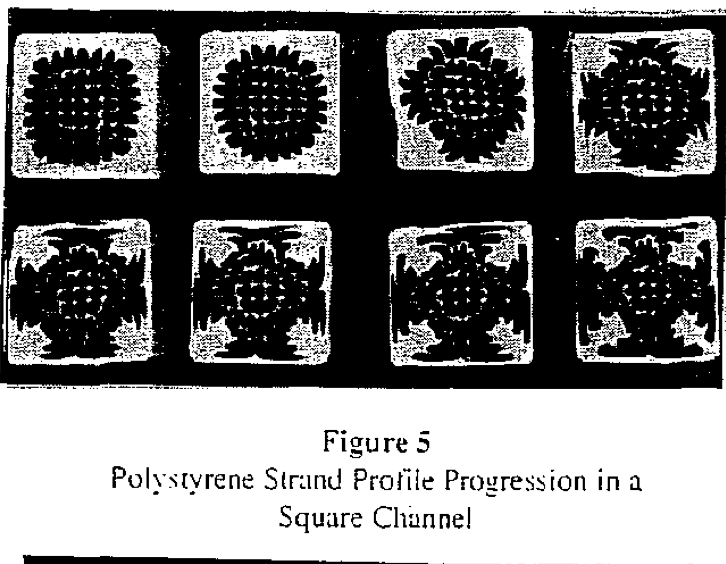
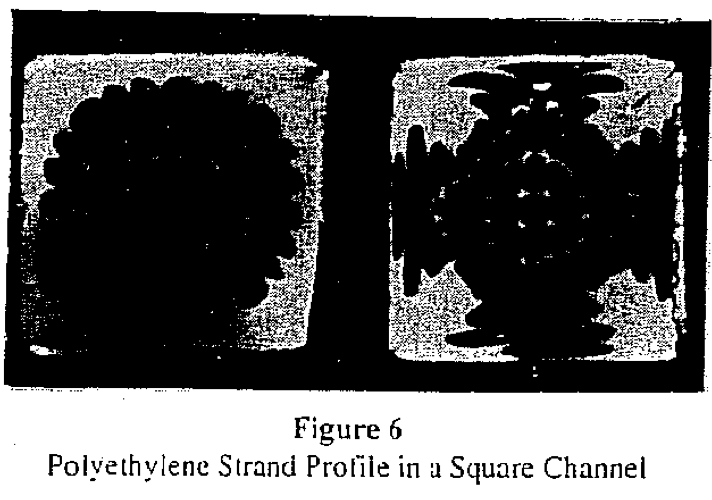
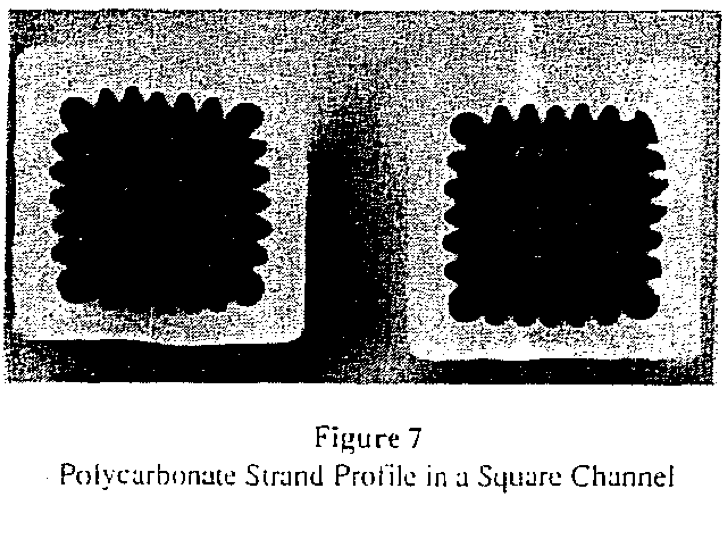
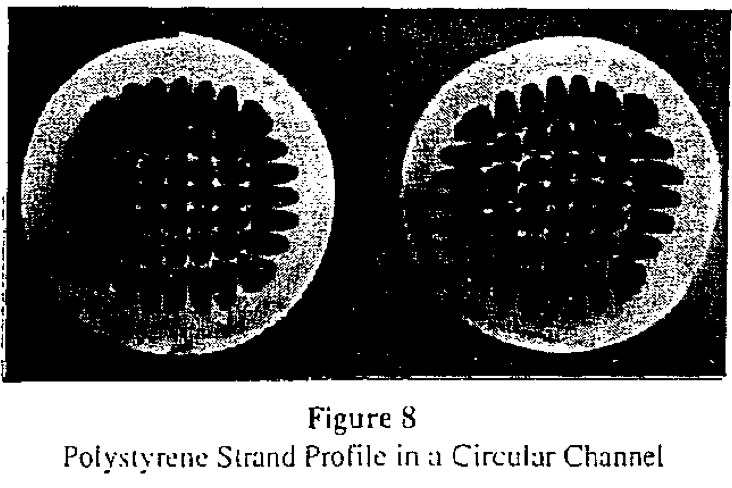
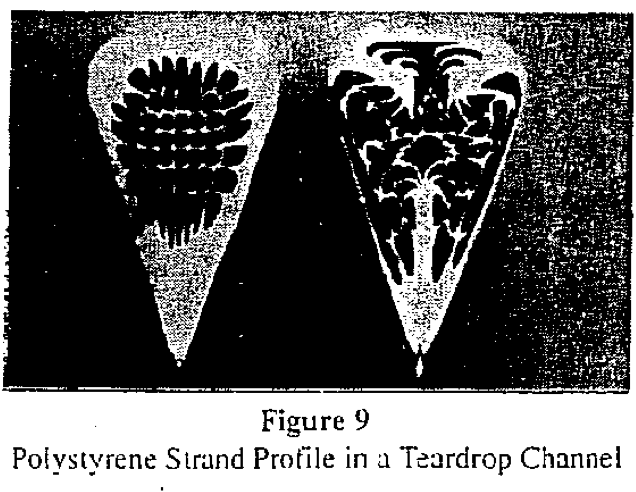
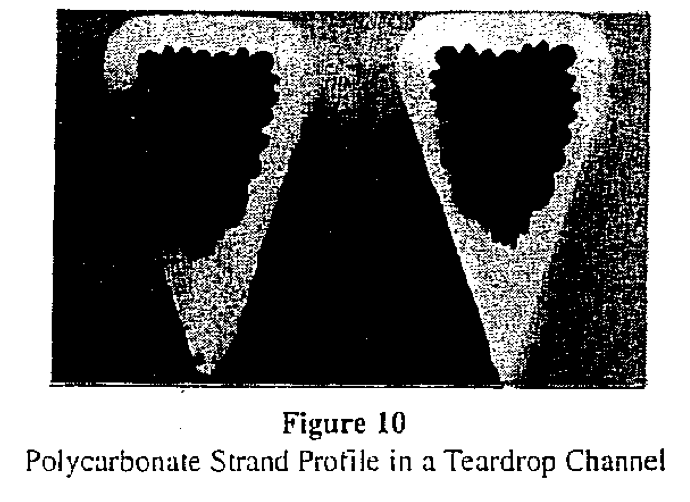
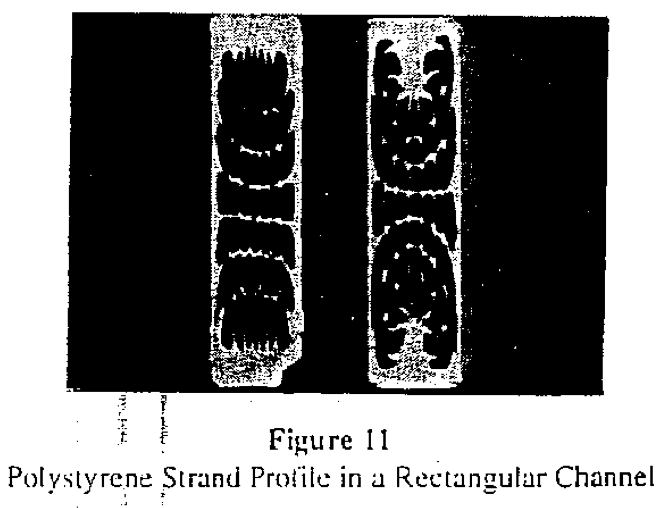
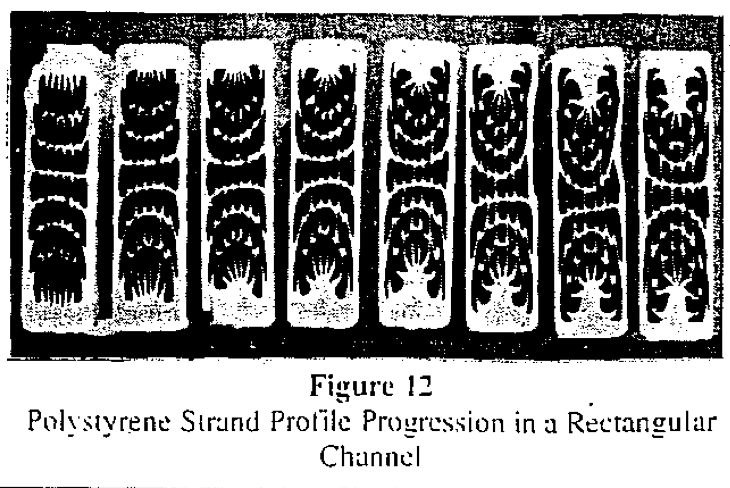
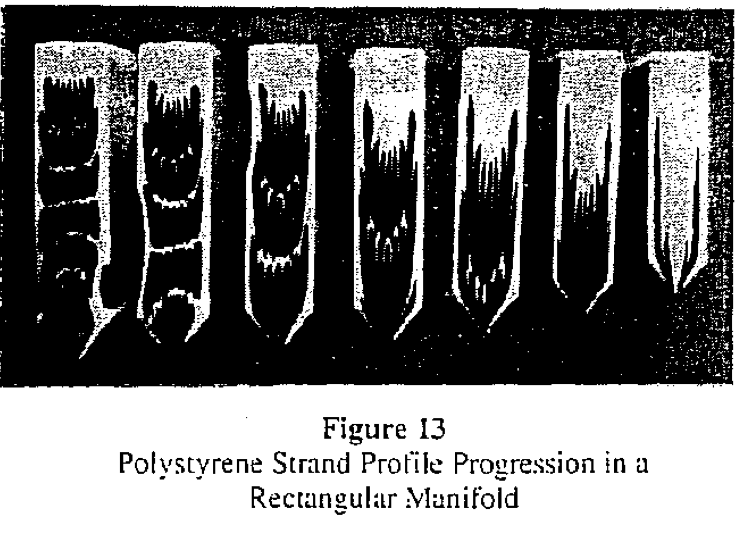
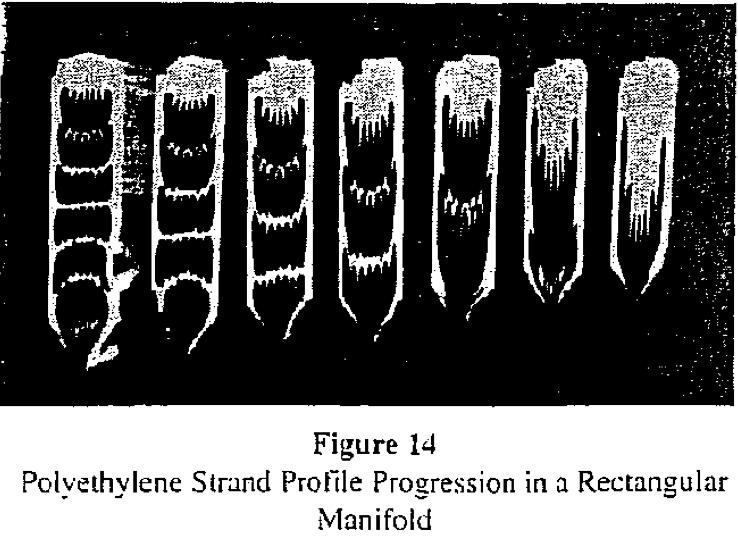
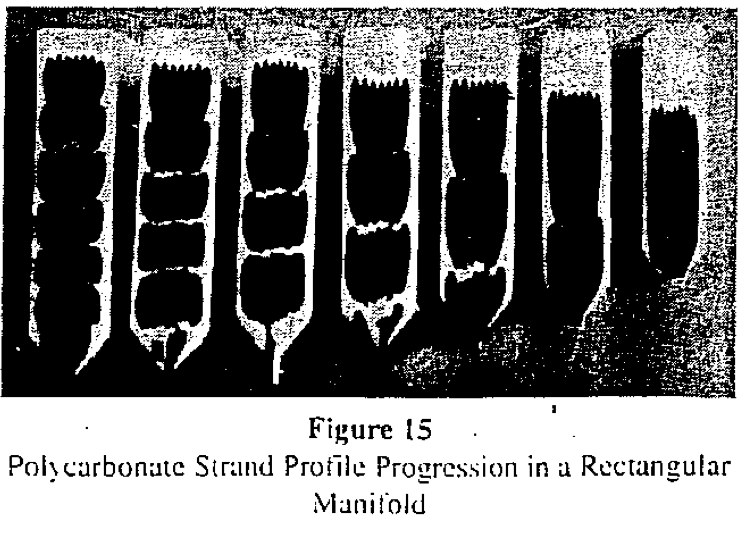